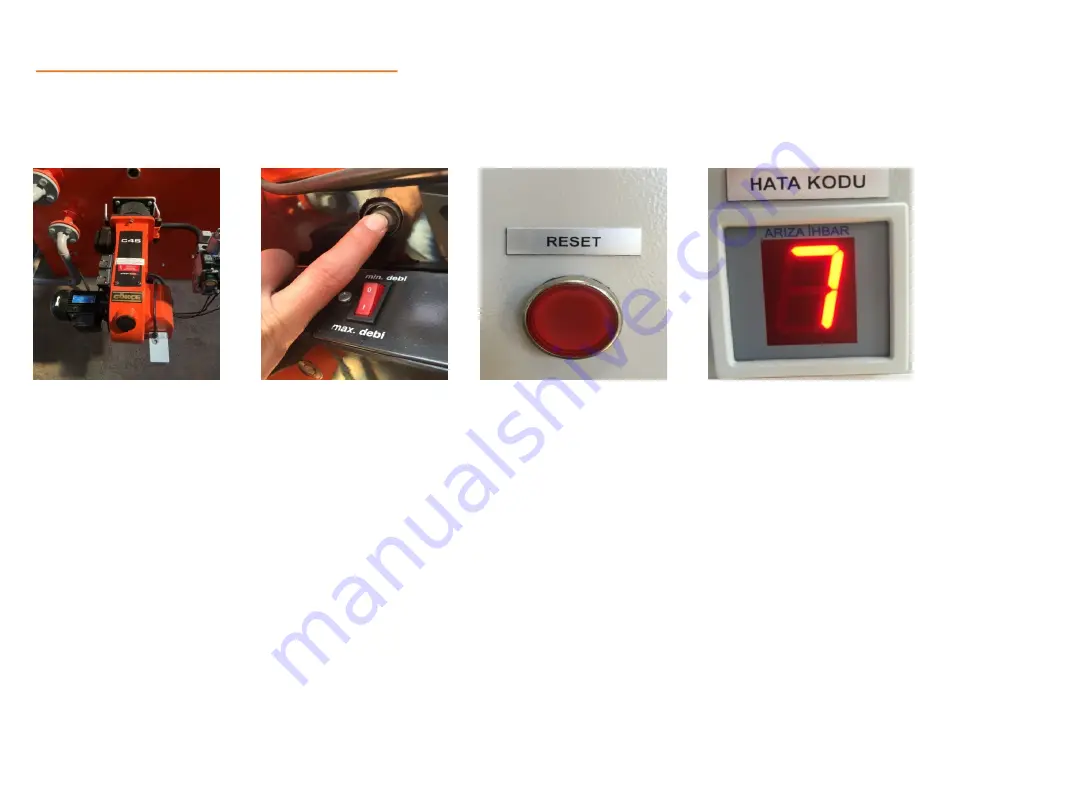
Fault Nb. 7 - Burner Malfunction
Description :
Gas (Natural Gas, LPG, CNG, LNG etc.) or liquid (Fuel-Oil, diesel etc.) burners are used on the steam
generator. Burner failures vary according to the type of fuel you are using. Burner malfunctioned and stopped for
some reason.
Natural Gas Burner
Control Box - Brain
Reset
Fault Code Indicator
Solution
:
* As the burner is in a fault state, fault 7 on the electrical control panel is lit. To eliminate the burner failure, you must first
reset it from the panel and then press the control box (brain) reset button on the burner.
* After this reset, the burner must be re-engaged and illuminated after a series of checks. When it fails again, the same
process is repeated several more times and the burner is restarted.
* The burner must be checked if it still has not started after these reset operations.
* For gas-fired burners, first check whether there is gas at the required pressure on the gas line. If gas is cut off the line, the
cause should be investigated.
* Check that the dirt catchers on the fuel line are clean.
* Electrode and nozzle cleanliness of liquid fuel burners should be checked.
* Fuel-oil burners must be checked for fuel heaters and whether the fuel is sufficiently heated.
* Contact your burner service if there is no fault in the parts up to this point and your burner does not light up after reset.
45
Summary of Contents for SHS Series
Page 10: ...Steam Distribution Connection Diagram 10 Buhar Da l m Kollekt r...
Page 12: ...Condensate Return Connection Diagram 12...
Page 15: ...15 Vent Connection and Blowdown Connection Diagram...
Page 55: ...55...
Page 56: ...56...