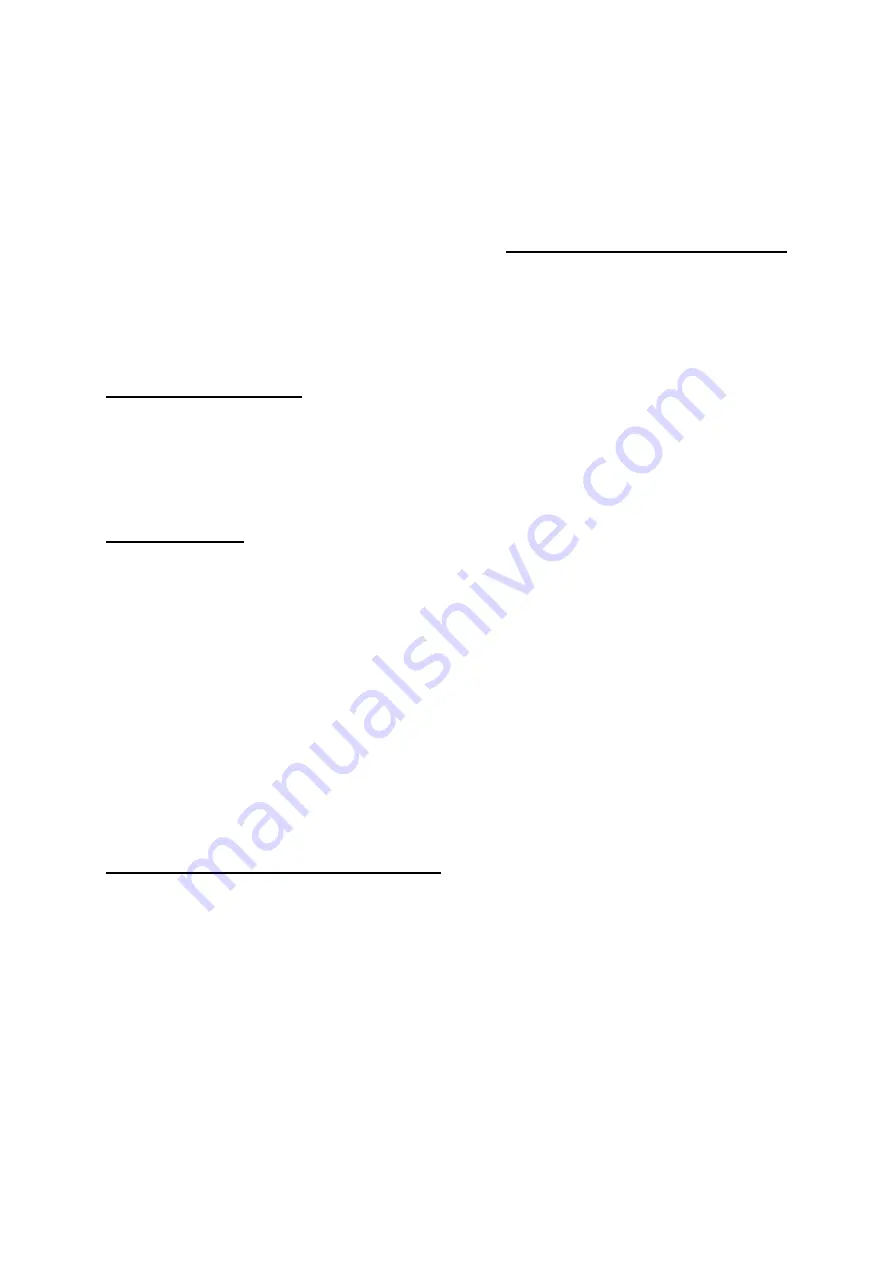
26
6.
Use a 24 mm angled socket spanner to turn the screw on the end of the 16-tooth
pinion to line up the 3 holes in the pinion with the 3 corresponding holes in its hub
located behind.
7.
Clear any screw debris from the 3 holes and collect all this debris.
8.
Fit 3 new screws and nylstop nuts (10mm open-ended spanner and socket spanner).
9.
Slacken the long screw to release the chain, leaving at least 10 mm of clearance
between the chain links and the end of the screw.
10.
Tighten the locknut.
11.
Refit the casing lower cover.
7 – WHEEL INFLATION
1.
Check tightness of wheel nuts and inflation pressure:
- Wheel dimensions: 205x60x15, 5 hole type.
- Tyre pressure 3.2 Bars; check once a week.
8-LUBRICATION
1.
See lubrication chart on page 14 for the location of lubrication points.
2.
The various lubrication points are arranged as follows:
-
1 grease nipple on the upper spindles of the 2 rear door actuators
-
1 grease nipple on each of the 2 shredder bearings
-
1 grease nipple on each of the 2 shaft bearings for the feed conveyor
-
1 grease nipple on the gearbox output shaft
-
2 grease nipples on the rotating chute
3.
Greasing frequency: all nipples once a week.
4.
Oil weekly all hinges that are not fitted with grease nipples.
9- FEED CONVEYOR REDUCTION GEAR
1.
Never drain (lubricated for life)
The reduction gear is lubricated for life. It therefore requires no attention. It has no plug
for refilling, level checking or draining; on build it was filled with the required quantity
of lubricant:
1 kg of grease or
0.870 litre SAE 90 oil
2.
If a repair operation must be carried out inside the casing, either oil or grease can be
installed before reassembly.
Never mix oil with grease; the reducer gear therefore has to be fully drained and cleaned
before refilling with lubricant.