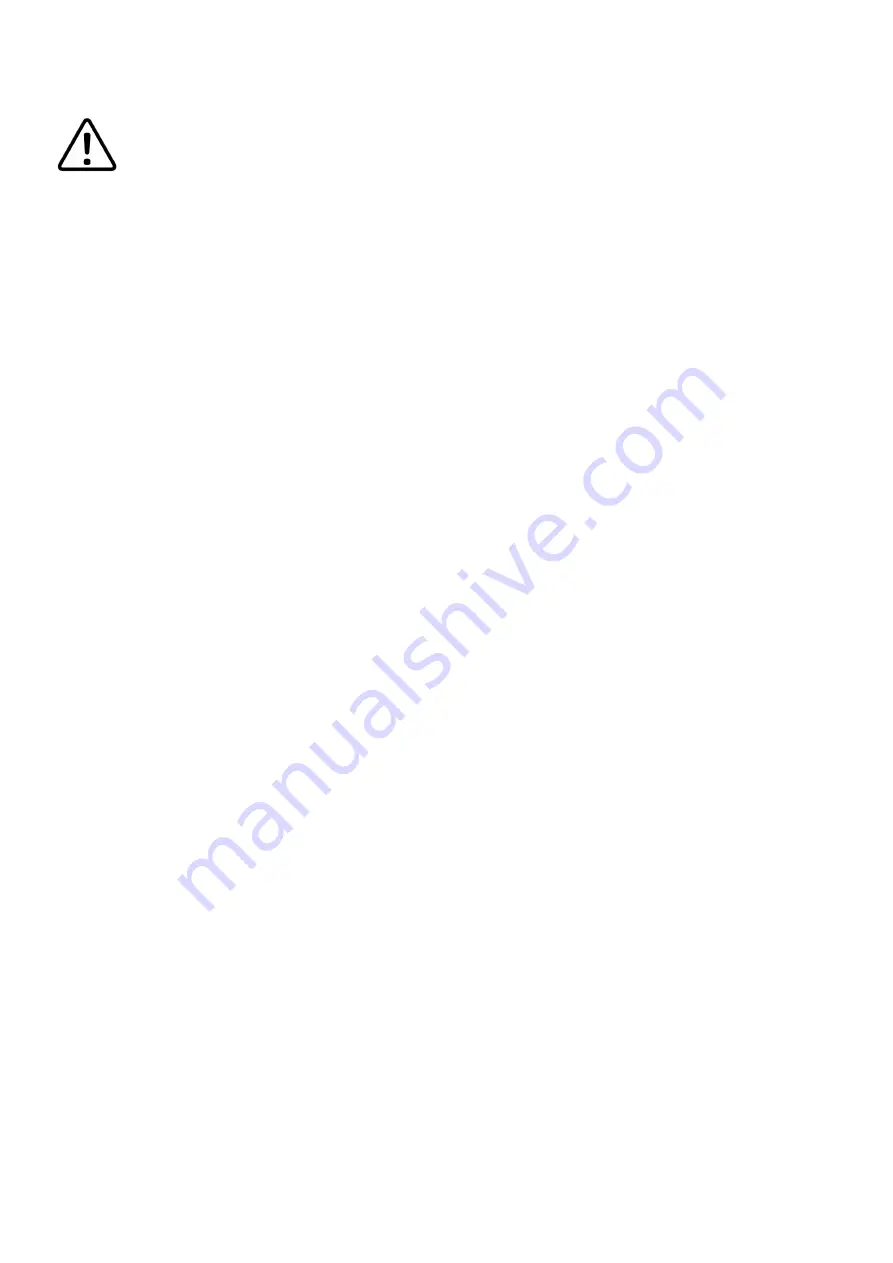
29
GUIDE TO MIG/MAG WELDING
Before starting any welding activity ensure that you have suitable eye protection and
protective clothing. Also take the necessary steps to protect any persons within the welding
area.
Burn back control
In the event that the welder was to stop welding and all functions of the machine stopped simultaneously
then the consumable filler wire would in all likelihood freeze in the weld pool. In order to avoid this
happening the burn back feature is present on this machine.
This facility is usually an adjustable control within these Jasic compact MIG machines and it will allow the
power and gas shield to be maintained on the consumable filler wire when it has stopped feeding thereby
burning clear of the weld.
The Jasic 200CS has an inbuilt burn back facility which is automatically set by the weld parameters
selected by the operator.
Some quick reference handy tips for the MIG/MAG welding process are:
•
When welding, try to use an electrode stick out (the distance between the weld and the contact tip)
of around 6
-
8mm
•
When welding thin materials try and use smaller MIG wire diameters and for thicker materials use
thicker wires
•
Make sure you select the correct MIG wire type for the material to be welded
•
Ensure the MIG welding gun has the correct sized contact tip and type of liner
•
Always ensure you have the correct size drive rolls and torch liner for the wire size selected
•
Select the correct gas to achieve the correct weld characteristics and finish
•
For optimum control of the weld keep the wire at the leading edge of the weld pool
•
Before commencing welding, ensure a comfortable and stable position
•
Try to keep the welding torch as straight as possible when welding to ensure the best feed
•
Carry out daily housekeeping on the condition of the welding torch and drive rolls
•
Keep any consumables clean and dry to avoid contamination such as oxidation and damp