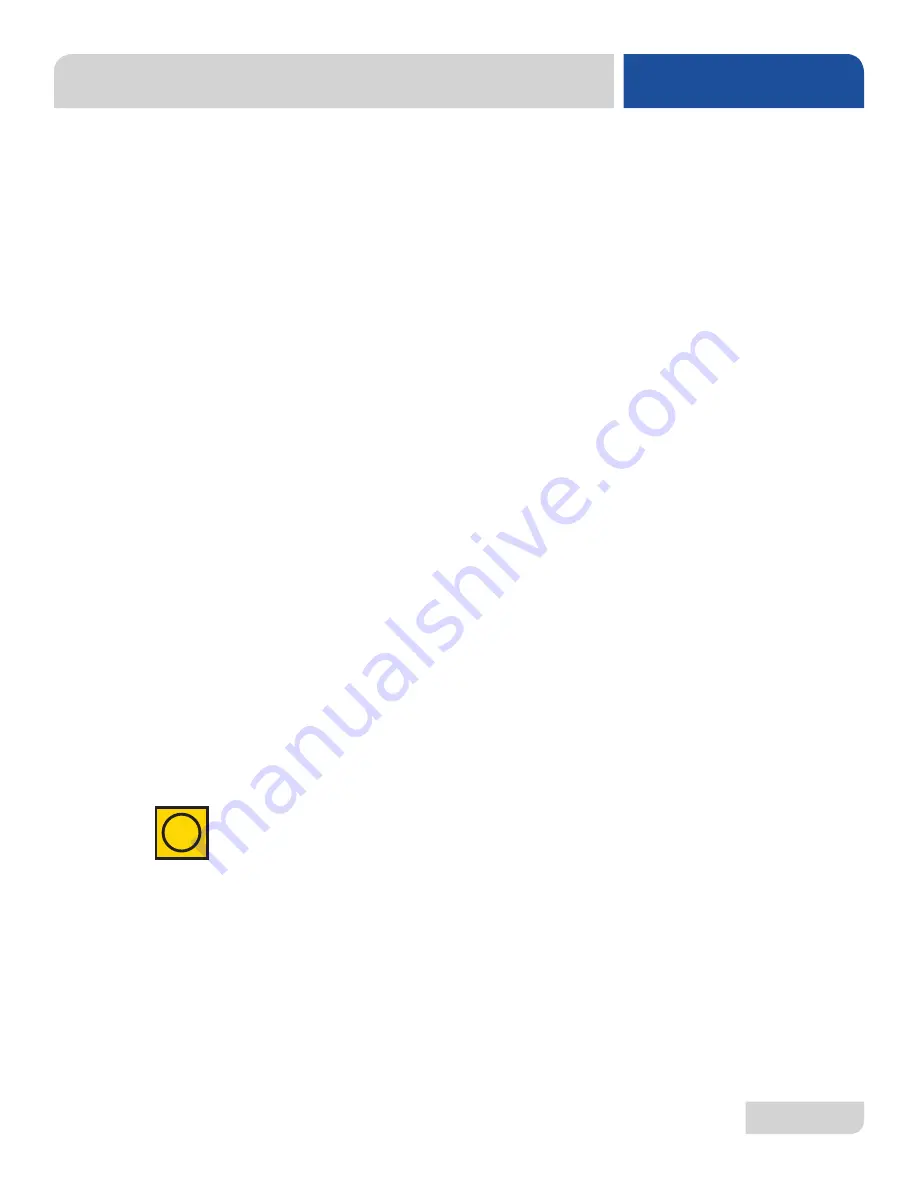
9
07610-004-04-18-R
INSTRUCTIONS
INSTALLATION
Detergent usage and water hardness are two factors that contribute greatly to how
efficiently this dishmachine will operate. Using detergent in the proper amount can
become a source of substantial savings. A qualified water treatment specialist can
determine what is needed for maximum efficiency from the detergent.
1. Hard water greatly affects the performance of the dishmachine, causing the
amount of detergent required for washing to increase. If the machine is installed
in an area with hard water, the manufacturer recommends the installation of water
treatment equipment.
2. Deposited solids from hard water can cause spotting that will not be removed with
a drying agent. Treated water will reduce this occurence.
3. Treated water might not be suitable for use in other areas of operation and it
might be necessary to install a water treatment unit for the water going to the dish-
machine only. Discuss this option with a qualified water treatment specialist.
4. Dishmachine operators should be properly trained on how much detergent is to
be used per cycle. Meet with a water treatment specialist and detergent vendor to
discuss a complete training program for operators.
5. Certain dishmachine models require that chemicals be provided for proper operation
and sanitization. Some models might require the installation of third-party chemical
feeders to introduce those chemicals to the machine. The manufacturer does not
recommend or endorse any brand name of chemicals or chemical dispensing
equipment. Contact a chemical supplier for questions.
6. Some dishmachines come equipped with integral solid detergent dispensers.
These dispensers are designed to accommodate detergents in a certain-sized
container. If applicable, relate this to a chemical supplier upon first contacting them.
7. Water temperature is an important factor in ensuring that the dishmachine functions
properly, and the machine's data plate details what the minimum temperatures must
be for the incoming water supply, the wash tank, and the rinse tank. If minimum
requirements are not met, there is a possibility that dishes will not be clean or sanitized.
8. Instruct dishmachine operators to observe the required temperatures and to report
when they fall below the minimum allowed. A loss of temperature can indicate a
larger problem.
DETERGENT
CONTROL
i
Summary of Contents for AVENGER HT-E
Page 2: ......
Page 38: ...30 07610 004 04 18 R CONTROL PANEL PARTS 1 8 3 2 4 5 6 7...
Page 48: ...40 07610 004 04 18 R WASH DRAIN MOTOR ASSEMBLY PARTS 10 11 12 13 1 2 3 4 5 9 8 6 7...
Page 54: ...46 07610 004 04 18 R RINSE TANK ASSEMBLY PARTS 8 7 6 5 2 3 4 1...
Page 59: ...51 07610 004 04 18 R SCHEMATICS 480 V 60 HZ 3 PHASE...