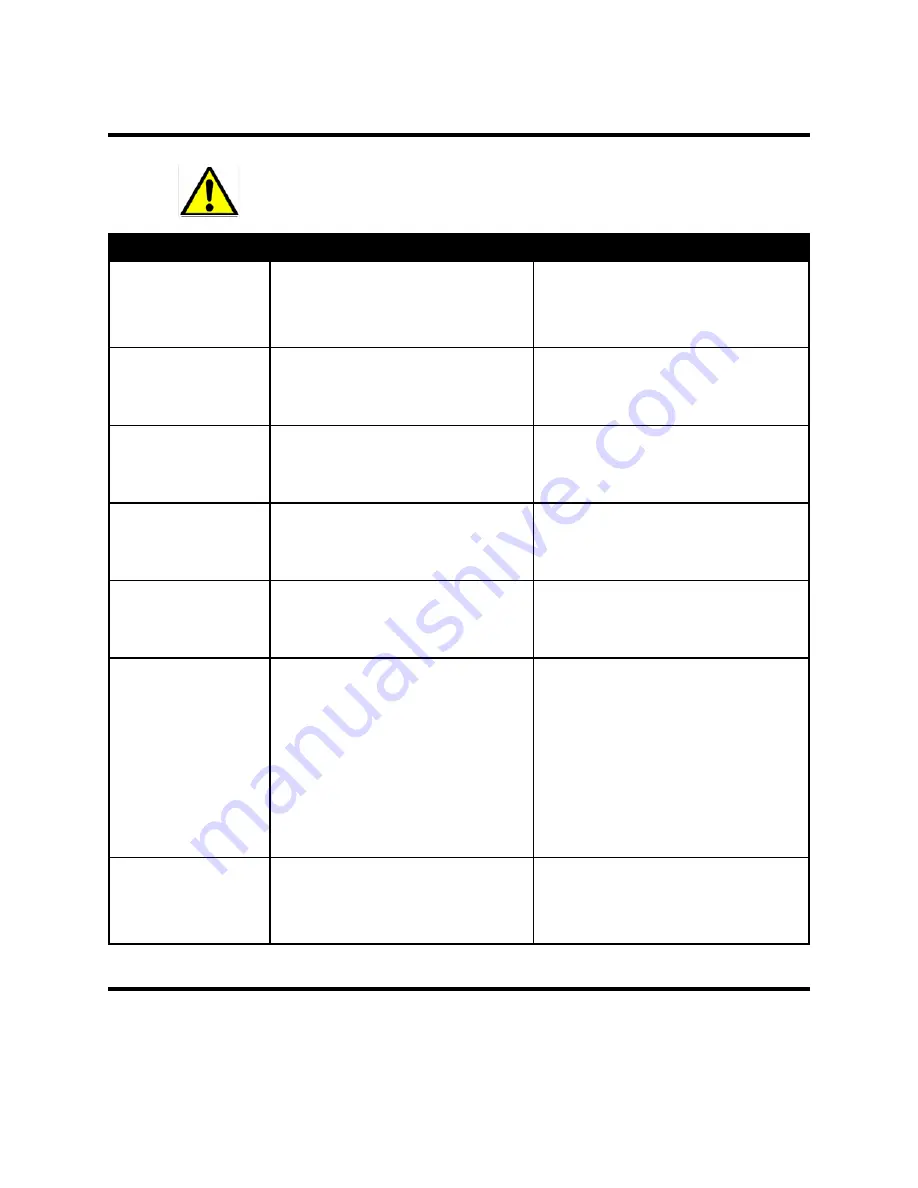
Technical Manual (07610-003-97-40)
TROUBLESHOOTING
23
Page Created: 09-10-2012
Revised: N/A
WARNING:
INSPECTION, TESTING AND REPAIR OF ELECTRICAL EQUIPMENT SHOULD ONLY BE PERFORMED BY A
QUALIFIED SERVICE TECHNICIAN. MANY OF THE TESTS REQUIRE THAT THE UNIT HAVE POWER TO IT
AND LIVE ELECTRICAL COMPONENTS BE EXPOSED.
USE EXTREME CAUTION WHEN
SERVICING THE MACHINE.
PROBLEM
POSSIBLE CAUSE
REMEDY
With master switch on, machine
Begins to rinse without operating
the start switch.
1. Defective timer motor or clutch slipping causing rinse
mircoswitch to remain energized
1. Check timer (
SEE PAGE 26 ON SERVICE INSTRUCTIONS FOR
THE TIMER)
Machine goes through entire
cycle and shuts off, but rinses the
entire cycle of the machine.
1. Defective rinse mircoswitch.
1. Check timer (
SEE PAGE 26 ON SERVICE INSTRUCTIONS
FOR THE TIMER)
Rinse runs continually with
power to the machine turned off.
1. Water inlet solenoid valve allowing water into
machine.
1. Check water pressure during fill, pressure must be
15 psi.
2. Repair or replace water inlet solenoid valve. (See
instructions on servicing solenoid valve)
With master switch off, rinse
runs continually as soon as
machine is powered on.
1. Defective rinse/fill switch.
1. Check rinse switch, replace if it is damaged or not
working correctly.
Rinse temperature to high.
1. Incoming water temperature is to high.
2. Thermostat set to high.
1. Required incoming water temperature 110 degrees,
adjust water temperature to meet machine operating
parameters.
2. Adjust thermostat control in counter clockwise direction
to lower rinse temperature.
Low rinse temperature.
1. Machine using more water than required caused by
excessive incoming water pressure.
2. Incoming water temperature to low.
3. Defective heater switch.
4. Thermostat setting is to low.
5. Defective Heater (element).
6. Defective rinse thermometer.
1. Verify incoming water pressure to machine, pressure
required is 15 psi. Use pressure regulator to adjust
pressure.
2. Required incoming water temperature 110 degrees,
adjust water temperature to meet machine operating
parameters.
3. Check rinse switch, replaces if it is damaged or not
working correctly.
4. Adjust thermostat control in clockwise direction to
increase rinse temperature.
5. Verify heater element is defective, replace only the
elements that are defective.
6. Remove thermometer and check in hot water against
accurate thermometer. If defective replace
thermometer.
Wash reservoir looses water
when not operation.
1. Overflow strainer not properly seated.
2. Bottom of overflow strainer bent out of shape.
3. O-ring missing or damaged at bottom of discharge
(seat that overflow strainer sits in).
1. Place strainer in firmly, insure strainer is seated
properly.
2. Replace strainer.
3. Replace o-ring .
Summary of Contents for 10AB-N70
Page 8: ...Revision Letter Revision Date Made By Applicable ECNs Details...
Page 59: ...APPENDIX A DEMA Nitro Warewash Dispenser A 1...
Page 61: ...Part 1 Nitro Warewash Dispenser User s Manual...
Page 70: ...Part 2 Solid Rinse Bowl Installation Instructions...
Page 75: ...Part 3 Viking Bowl Installation Instructions...
Page 78: ...Part 4 Nitro Warewash Dispenser Training Manual...