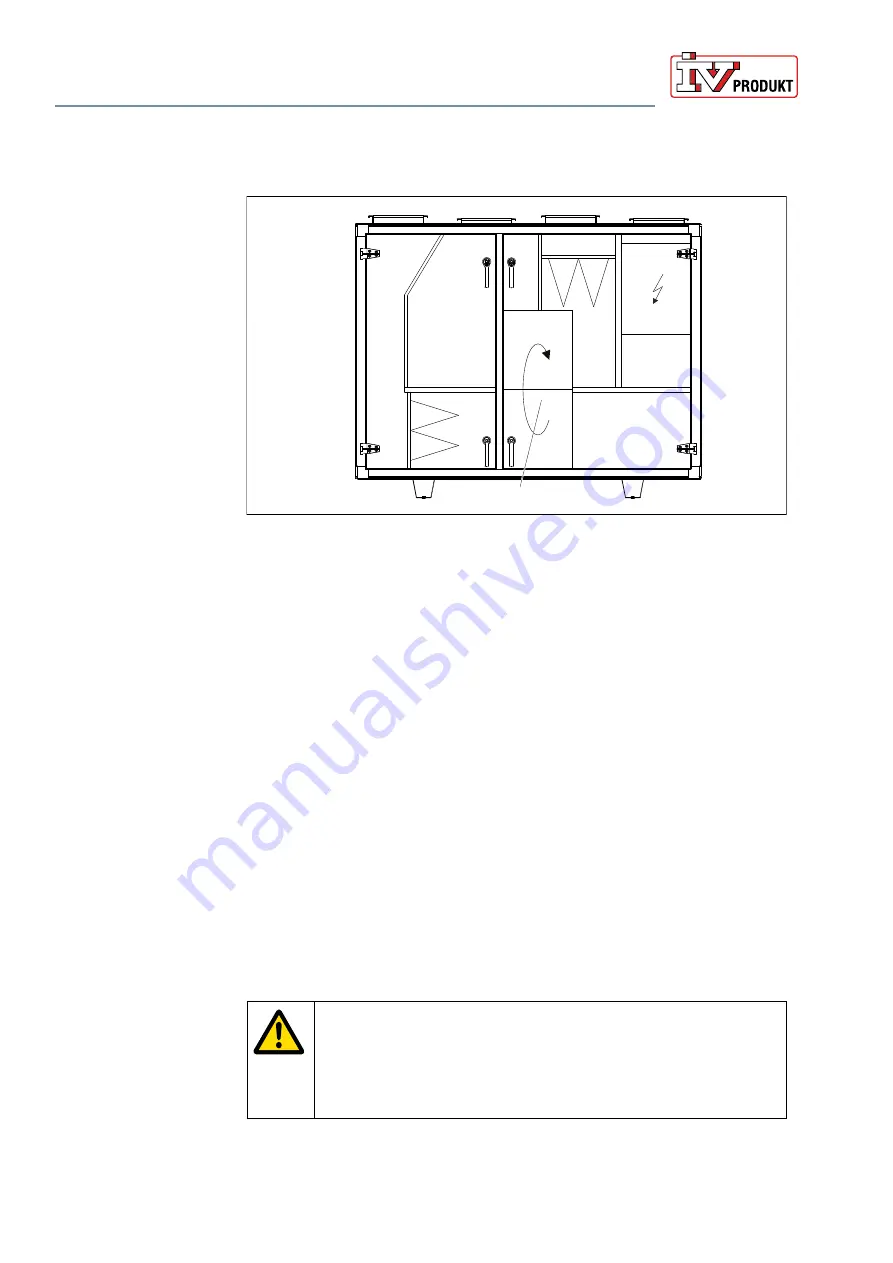
Page 38
Operation and Maintenance
Envistar Top 04-21
DSET.220501.07.en
Continuous product development may give rise to specification changes without notice.
6.3 Rotary heat exchanger (code TXRR)
00013
1
1. Rotary heat exchanger
The purpose of the recovery unit is to recover heat from the extract air and
transfer this heat to the supply air in order to minimise energy use.
Faults in recovery unit functionality result in reduced heat recovery efficiency and
increased energy use and means that the design supply air temperature cannot
be obtained when the outdoor temperature is low
A conceivable reason for reduced recovery efficiency may be that the rotor
rotates too slowly because the drive belt is slipping. The rotor speed should not
be lower than 8 rpm during full energy recovery.
It is not usual for the rotor passages to become fouled with dust, since the rotor
is normally self-cleaning. However, this might occur if the dust is of a sticky na-
ture.
A reduction of the extract air flow, e.g. due to fouling of the extract air filter, en-
tails reduced heat recovery efficiency.
Units in the Home Concept design are equipped with a function to control the
pressure balance of the rotor to ensure the correct leakage function and purging
function. For units supplied with control equipment, the function is connected
and activated at the factory. For units without control equipment, this function
must be connected to the unit.
Inspection
WARNING!
Risk of serious personal injury and/or damage to air handling
unit.
Read and understand the entire chapter "1.5 General safety
messages" before working on, servicing, or inspecting the air
handling unit.
1. Shut down the unit via the service switch in the control equipment, safety
switch in the 0 position.