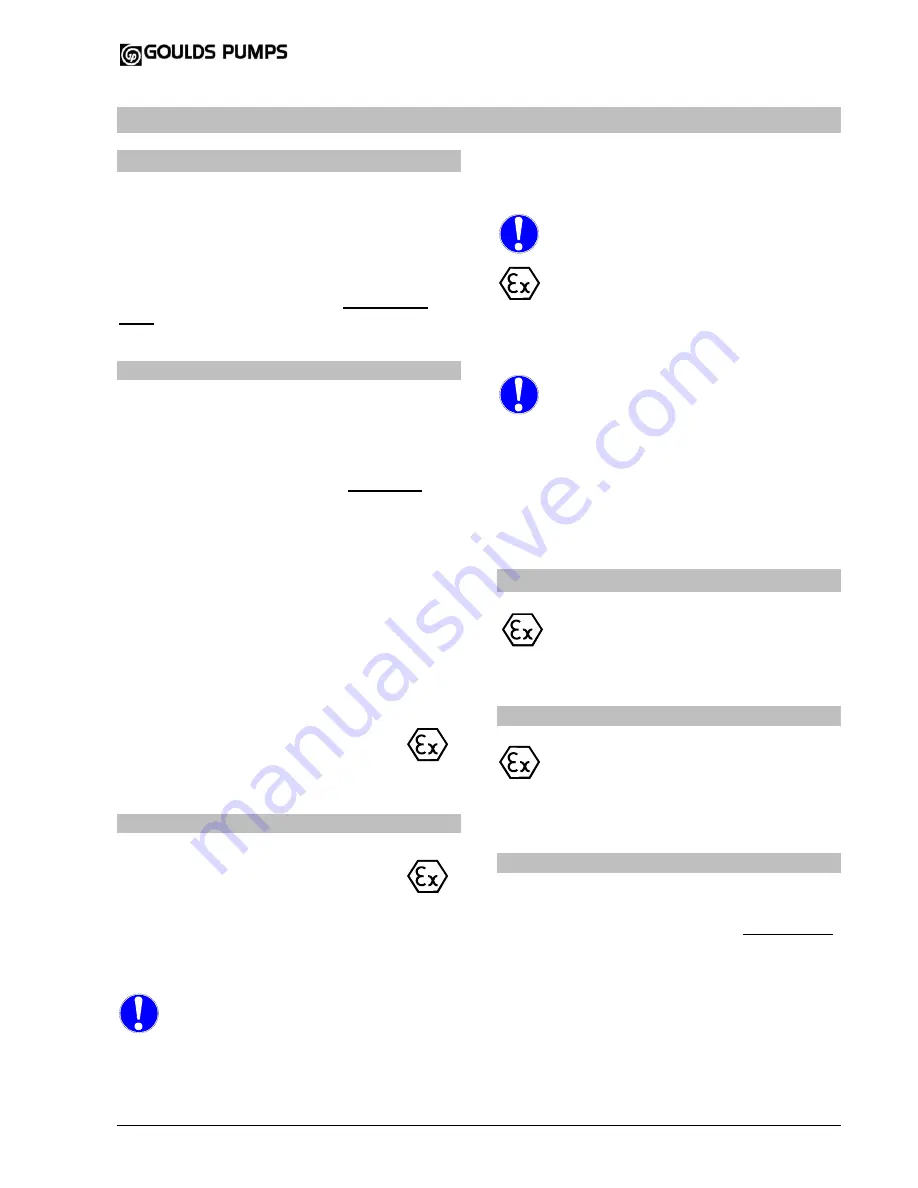
Installation and Operating Instructions
Model
ICM, ICMP
,
oil bath lubrication
9330-051-en
Revision 14
TM 6099 MPE/Wm
Page 14
Date 24/08/2011
6 Commissioning/Shutdown
6.1 Initial
commissioning
Normally, the pumps have already been test-run with
water. Unless special agreements have been made,
there could still be residual amounts of water in the
pump. This must be noted in view of a possible reac-
tion with the medium.
Pour in oil into the bearing pedestal!
For procedure and the oil grade,
Sections 7.2
and
7.8.6.
6.1.1 Filling the pump housing
¾
Check to see whether the screws on the suction
flange, discharge flange, housing flange and drain
flange are tightened. When retightening the hous-
ing screws, make sure that the support bracket is
undone. Otherwise, the pump could be deformed.
For screw tightening torques see
Section 1.2
.
¾
Open the suction line fully so that the medium can
flow into the pump.
¾
Open the discharge valve so that the air in the
pump can escape.
¾
If air cannot be vented into the discharge line, e.g.
a drop in pressure in this line is not permitted,
venting must be performed upstream of the dis-
charge valve.
¾
Monitor the venting operation until no air but only
liquid emerges.
¾
Turn the pump shaft at the coupling several times.
¾
Monitor the venting operation again until no more
air emerges.
¾
Close the discharge valve again until
only the minimum flow rate is obtained
after the motor has been started.
6.1.2 Start-up
¾
Check to see whether the pump shaft
can be readily turned by hand.
¾
Check the direction of rotation of the
motor with the coupling disengaged or a rotary
field instrument.
¾
As viewed from the motor, the direction of rotation
of the pump is clockwise. See also the
direction
of rotation arrow
of the pump.
The pump must not run dry during the check
of the direction of rotation.
¾
Engage coupling, check alignment and secure.
¾
Mount coupling guard.
The pump must be completely filled with liquid.
The maximum admissible flow rate must not
be exceeded.
Otherwise the plain bearings can run dry in
both cases.
¾
Switch the motor on.
¾
Set the desired flow by opening the discharge
valve.
When the motor is running but the pump is not
conveying, this means that the magnetic drive
has stopped.
Switch the motor off immediately to prevent overheat-
ing of the magnets.
Then proceeded as follows:
¾
Close discharge valve down to the position "mini-
mum flow rate".
¾
Start motor again.
If the magnetic drive stops again, look for the cause.
6.2 Operating
limits
The operating limits of the pump/unit in terms
of pressure, temperature, power and speed
are entered in the data sheet and it is impera-
tive to observe them!
6.2.1 Abrasive
media
If liquids with abrasive constituents are con-
veyed, increased wear at the pump is to be
expected.
The inspection intervals should be reduced compared
with the usual times.
6.2.2 Min./max.
flow
rate
The operating range generally recommended lies at
0.3 Q
opt
to 1.1 Q
opt
. Consult the manufacturer for op-
eration outside this range and observe
Section 2.5.2.
Summary of Contents for ICM
Page 10: ...S 9 ...
Page 34: ......