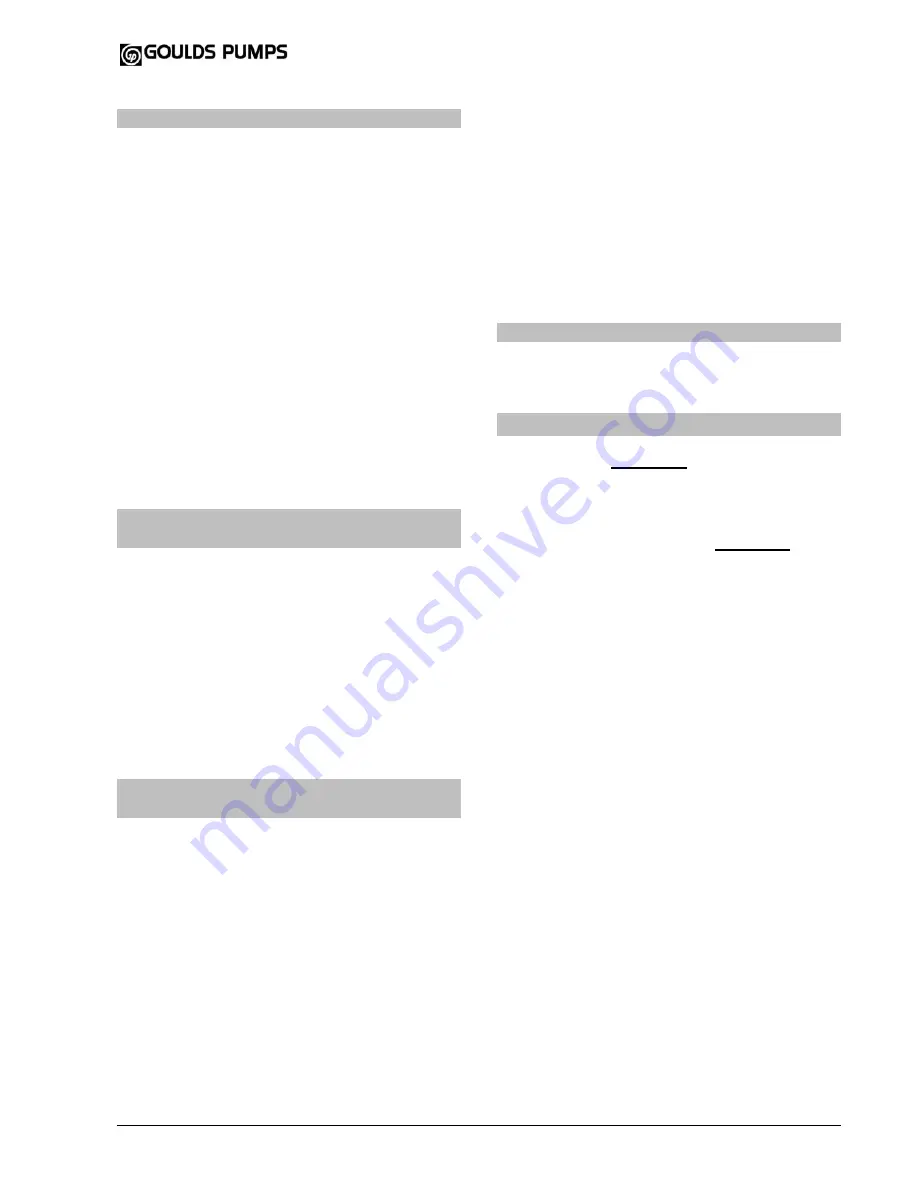
Installation and Operating Instructions
Model
ICM, ICMP
,
oil bath lubrication
9330-051-en
Revision 14
TM 6099 MPE/Wm
Page 19
Date 24/08/2011
7.6.2 Dismantling
bearing
pedestal
¾
Remove oil drain plug
655/1
and drain oil. Remove
any chips from the magnetic oil drain plug.
¾
Clamp drive shaft
213
with its end in the vice.
¾
Undo hex. socket screw
914/1
in counterclockwise
direction.
¾
Pull off drive magnet assembly
858
.
¾
Remove pump from the vice.
¾
Undo rear bearing cover
361
with rotary shaft seal
421/1
.
¾
Undo cover gasket
403
.
¾
Remove wavy spring washer
953/1
.Pull out drive
shaft
213
with both ball bearings
321
.
¾
Both radial ball bearings lie against the shaft collar
so remove singly on a press.
¾
If necessary, push the rotary shaft seals
421/1
out
of the rear bearing cover
361
and
421/2
out of bea-
ring pedestal
330
.
¾
Remove support bracket
183
.
7.6.3 Removing lantern, can and plain
bearing pedestal
¾
Undo housing screwing
901/3, 554/3
.
¾
Do not undo the two screws
901/5
(if installed).
They hold the lantern
344
, can
159
and plain bear-
ing pedestal
339
together.
¾
Pull the entire slide-in unit out of the housing
100
.
¾
If the housing does not move (e.g. owing to corro-
sion at the centering), remove the two plastic plugs
from the lantern
344
.
¾
Screw in jacking screws M8 and use them to press
off the lantern.
7.6.4 Dismantling lantern, can and plain
bearing pedestal
¾
Place the unit lantern
344
/ plain bearing pedestal
339
/ impeller
230
on the workbench with the im-
peller facing upwards.
¾
Remove the two hex. screws
901/5
or the 3 set-
screws
904/2
(depending on size).
¾
Remove lantern
344
and can
159
.
¾
Place remaining unit on the inner magnet assem-
bly.
¾
Place strap wrench around the impeller and undo
the impeller nut
231
counterclockwise.
¾
Pull off impeller
230
.
¾
Remove key
940/2
, distance washer
551/1
and
intermediate ring
509/2
.
¾
Pull the plain bearing cartridge
310
with plain bear-
ing pedestal
339
out of the inner magnet assembly
859
.
¾
Remove 2
nd
intermediate ring
509/1
from the inner
magnet assembly
859
.
¾
If the inner magnet assembly or inner magnet as-
sembly shaft has to be replaced (split inner magnet
assembly):
Push the inner magnet assembly shaft
220
and
key
940/2
out of the inner magnet assembly
859
with a hydraulic press. Make sure that the thread
for the impeller nut is not damaged.
¾
Undo screws
901/1
and remove plain bearing car-
tridge
310
from the plain bearing pedestal
339
.
7.6.5 Dismantling the plain bearing
The plain bearing cartridge
310
is one unit which - if
necessary - is replaced completely.
7.7 Notes on assembly
All the details in
Section 7.5
are to be observed, in
particular the notes on safety.
Good mechanical engineering practice is to be ob-
served for assembly work.
Use original spare parts. See also
Section 2.3
. Do not
use defective parts.
Treat close-tolerance areas (not on stainless steel
parts) with a corrosion inhibitor. Greas screw threads
prior to assembly.
Check whether all parts fit and only then perform as-
sembly.
Important dimensions are to be checked before as-
sembly, e.g. by fitting parts together as a test.
These important dimensions are centerings, bearing
seats or bearing clearances.
During assembly, gaskets
400
,
401
and
406
are to be
replaced, intermediate rings
509
must be replaced.
Prior to assembly, remove any metallic particles ad-
hering to parts fitted with magnets.
Summary of Contents for ICM
Page 10: ...S 9 ...
Page 34: ......