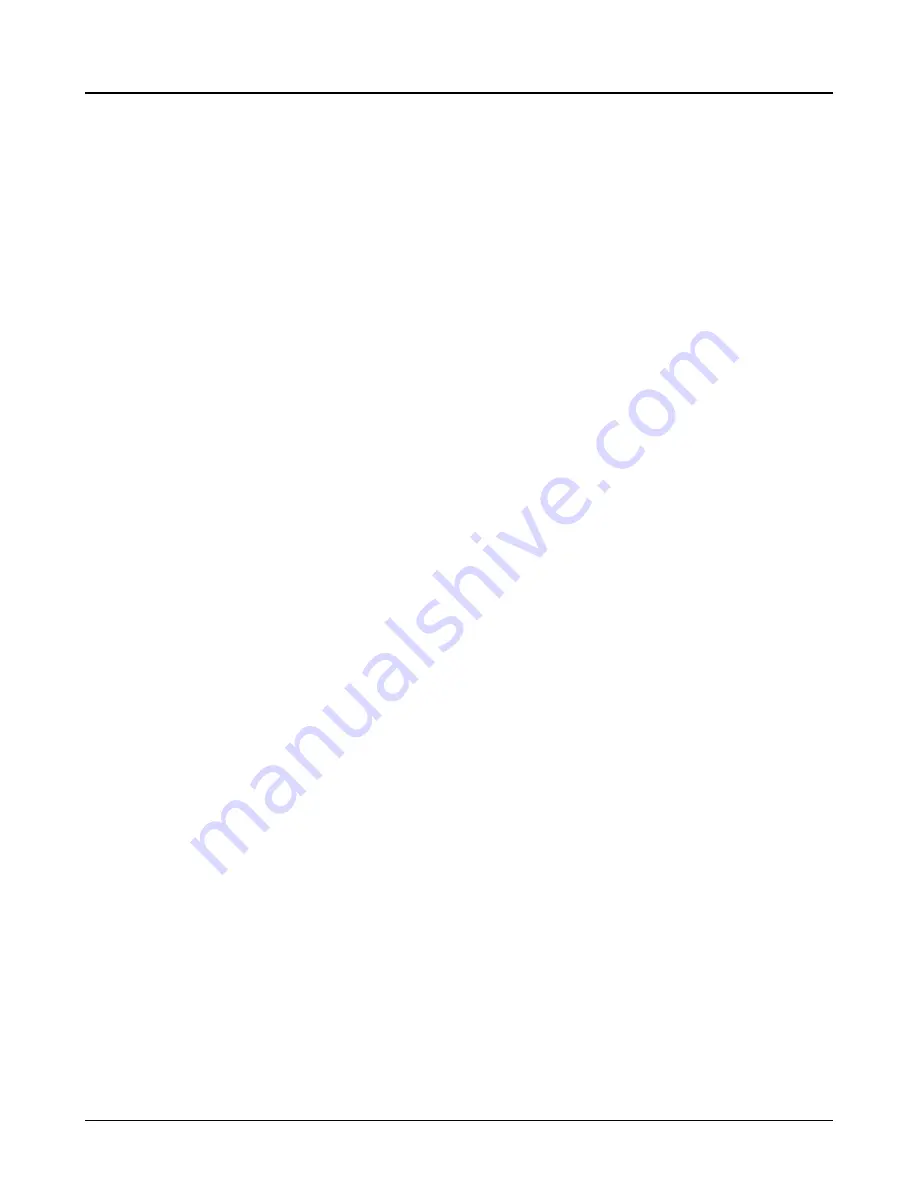
3.8.2 Gas mixing
Pipe
•
Gas addition should always be added in the chemical addition point of the chemical injection pipe
supplied with the mixer.
•
If flow velocity is higher than 9 ft/s, special 8° increasers are required after the mixer.
•
Before any elbows, the flow velocity must be lower than 2 ft/s.
•
Flow velocity into a tower must be 1.5 ft/s or lower.
•
Recommended angle at the bottom of the upflow reactor is 36°.
Chemical Injection Pipe
•
Is two (2') feet long and the same size and material as the mixer.
•
Is part of the mixer design package.
Valves
•
Control valve cannot be after the mixer.
•
Shut off valve should be after the mixer.
•
The inner diameter of the shut off valve(s) must be full port (same size as the inner diameter of the
pipe).
Pipe Supports - Liquid and Gas Mixing
•
Special care needs to be taken when designing pipe supports around the mixer.
•
Often process temperatures are high, causing thermal expansion and high loading
•
Steam addition and steam mixing can cause thermal expansion and high loading.
Mixer Flange Loads
•
Allowable flange loads for the suction and discharge nozzles are available
3.9 Spring mounted baseplates
1.
Raise or support the baseplate above the foundation/floor. Be sure to allow enough room under the
baseplate to install the spring assemblies.
2.
Set the bottom adjusting nuts on each spring stud to the height indicated on the certified dimension-
al drawing.
3.
Insert a washer between the bottom adjusting nut and the spring follower. Install a spring and an-
other follower. Install this sub-assembly from the bottom of the baseplate.
4.
Install the upper half of the spring assembly consisting of a follower, a spring, another follower, and
a flat washer. Now install the top adjusting nut and jam nut. Tighten finger tight.
5.
Repeat steps one through four for all the spring assemblies.
6.
Once all the springs have been installed, lower the unit on to the foundation pads.
3.9 Spring mounted baseplates
22
3501 Installation, Operation, and Maintenance Instructions