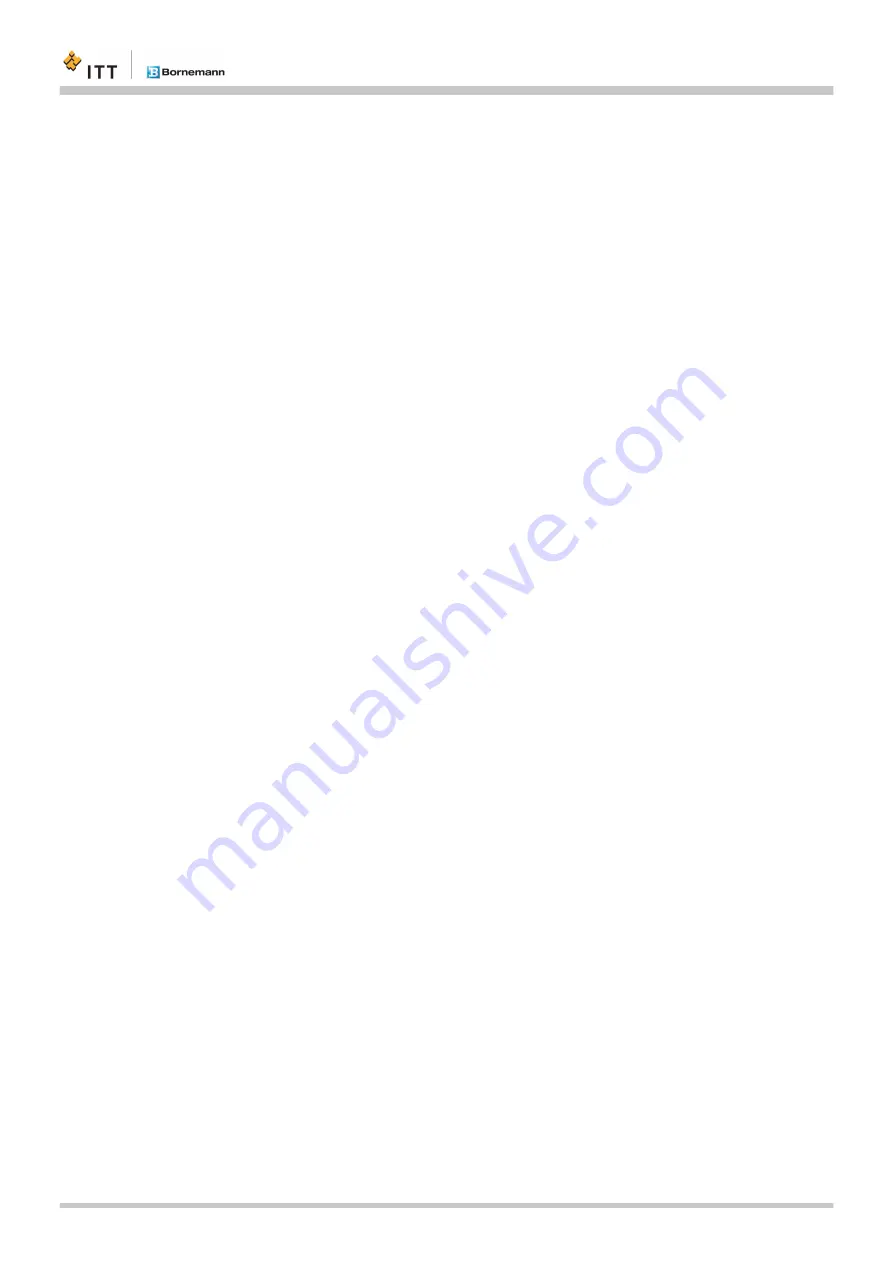
6.4.1 Measures in accordance with the conveyed medium.................... 58
6.5 Recommissioning............................................................................. 58
6.6 Operating the stand-by pump........................................................... 59
6.7 Disposal............................................................................................ 59
........................................................................
7.1 Wearing parts................................................................................... 60
7.2 Monitoring......................................................................................... 60
7.3 Maintaining....................................................................................... 61
7.3.1 Maintenance table......................................................................... 63
7.3.2 Lubrication..................................................................................... 64
7.4 Remove pump and send to manufacturer........................................ 65
7.4.1 Remove pump............................................................................... 66
7.4.2 Return pump to the manufacturer.................................................. 67
7.5 Repair pump..................................................................................... 67
7.5.1 Order spare parts.......................................................................... 68
7.6 Lubrication points............................................................................. 68
7.7 Lubricant........................................................................................... 69
7.7.1 Gear oil, temperature of the medium to be pumped 10 – 300 °C.. 69
7.8 Lubricant amounts............................................................................ 69
7.9 Preservative agents.......................................................................... 70
7.10 Cleaning fluid.................................................................................. 70
............................................................................................
..................................................................................................
9.1 Technical data.................................................................................. 73
9.1.1 Ambient conditions........................................................................ 73
9.1.2 Noise level..................................................................................... 73
9.2 Declaration of no objection............................................................... 74
9.3 Declaration in accordance with the EC machinery directive............. 75
9.3.1 Declaration of conformity in accordance with the EC machinery
9.3.2 Declaration of incorporation in accordance with the EC machi-
nery directive................................................................................. 76
Table of contents
Type SLH-4G, SLHS-4G
5
01/2016 JPB Rev. 5