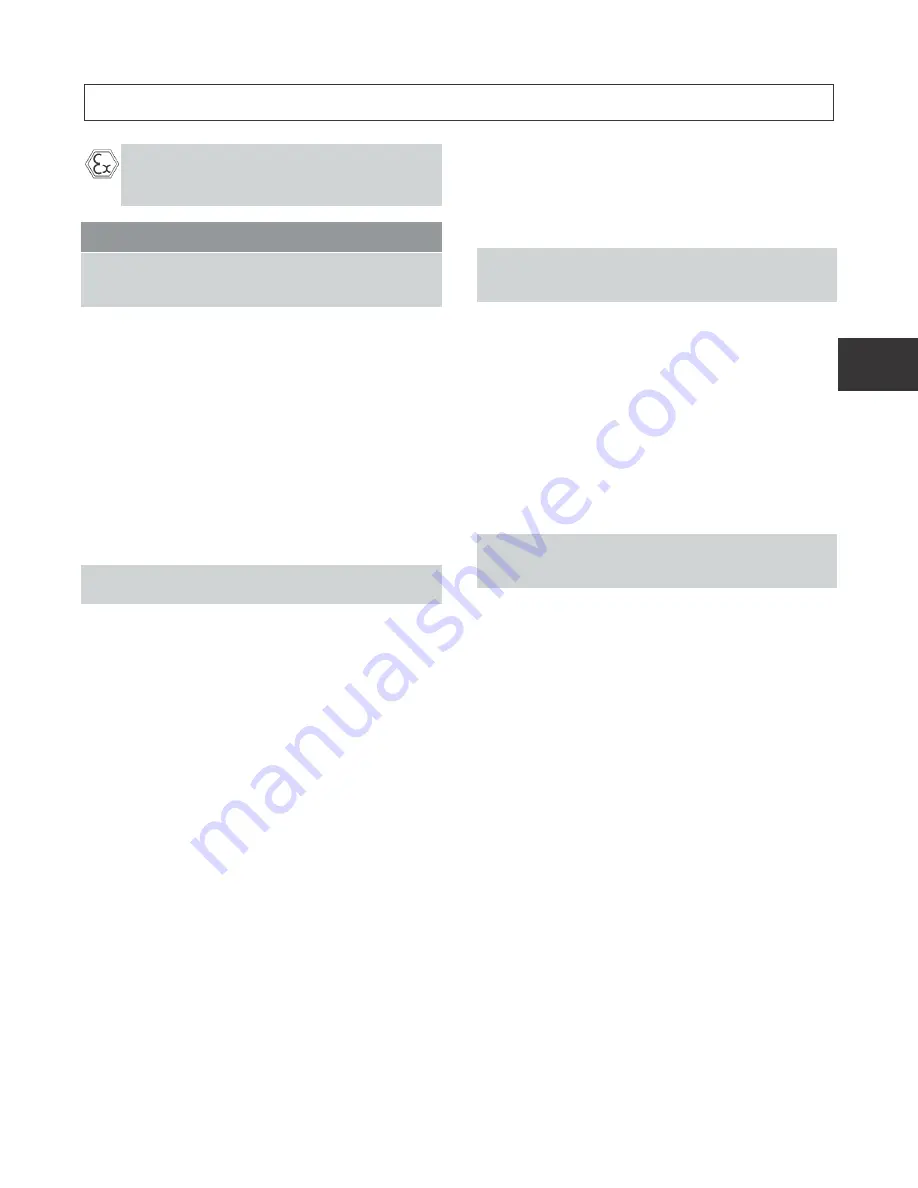
ALIGNMENT
Alignment procedures must be followed to
prevent unintended contact of rotating parts.
Follow coupling manufacturer’s coupling
installation and operation procedures.
s
!
WARNING
Before beginning any alignment procedure, make
sure driver power is locked out. Failure to lock out
driver power will result in serious physical injury.
To remove guard, refer to coupling guard assembly/
disassembly instructions.
The points at which alignment is checked and
adjusted are:
•
Initial Alignment
is done prior to operation when
the pump and the driver are at ambient temperature.
•
Final Alignment
is done after operation when the
pump and driver are at operating temperature.
Alignment is achieved by adding or removing shims
from under the feet of the driver and shifting
equipment horizontally as needed.
NOTE: Proper alignment is the responsibility of
the installer and user of the unit.
Accurate alignment of the equipment must be
attained. Trouble-free operation can be accomplished
by following the procedures in
Appendix III
.
ALIGNMENT CHECKS
Initial Alignment (Cold Alignment)
•
Before Grouting Baseplate
- To ensure alignment
can be obtained.
•
After Grouting Baseplate
- To ensure no changes
have occurred during grouting process.
•
After Connecting Piping
- To ensure pipe strains
haven’t altered alignment. If changes have
occurred, alter piping to remove pipe strains on
pump flanges.
Final Alignment (Hot Alignment)
•
After First Run
- To obtain correct alignment when
both pump and driver are at operating temperature.
Thereafter, alignment should be checked periodically
in accordance with plant operating procedures.
NOTE: Alignment check must be made if
process temperature changes, piping changes
and or pump service is performed.
ALIGNMENT CRITERIA
Good alignment is achieved when the dial indicator
readings as specified in the alignment procedure are:
•
.002 in. (.05 mm) Total Indicated Reading (T.I.R.)
or less when the pump and driver are at operating
temperature (Final Alignment)
•
.0005 in. per inch of dial indicator separation for the
reverse dial indicator or laser method when the
pump and driver are at operating temperature
(Final Alignment).
NOTE: C-Face motor adapter installation
insturctions and alignment criteria are detailed
in Appendix V.
During the installation phase, however, it is necessary
to set the parallel alignment in the vertical direction to
a different criteria due to differences in expansion
rates of the pump and driver.
Table 1
shows
recommended preliminary (cold) settings for electric
motor driven pumps based on different pumpage
temperatures. Driver manufacturers should be
consulted for recommended cold settings for other
types of drivers (steam turbines, engines, etc.)
ANSIFAM IOM - 12/03
29
3
Summary of Contents for Goulds Pumps 3196
Page 1: ...Installation Operation and Maintenance Instructions ANSI FAMILY ...
Page 4: ...4 ANSIFAM IOM 12 03 ...
Page 6: ...6 ANSIFAM IOM 12 03 ...
Page 10: ...10 ANSIFAM IOM 12 03 ...
Page 12: ...This Page Intentionally Left Blank 12 ANSIFAM IOM 12 03 ...
Page 28: ...BASEPLATE LEVELING WORKSHEET 28 ANSIFAM IOM 12 03 ...
Page 44: ...44 ANSIFAM IOM 12 03 ...