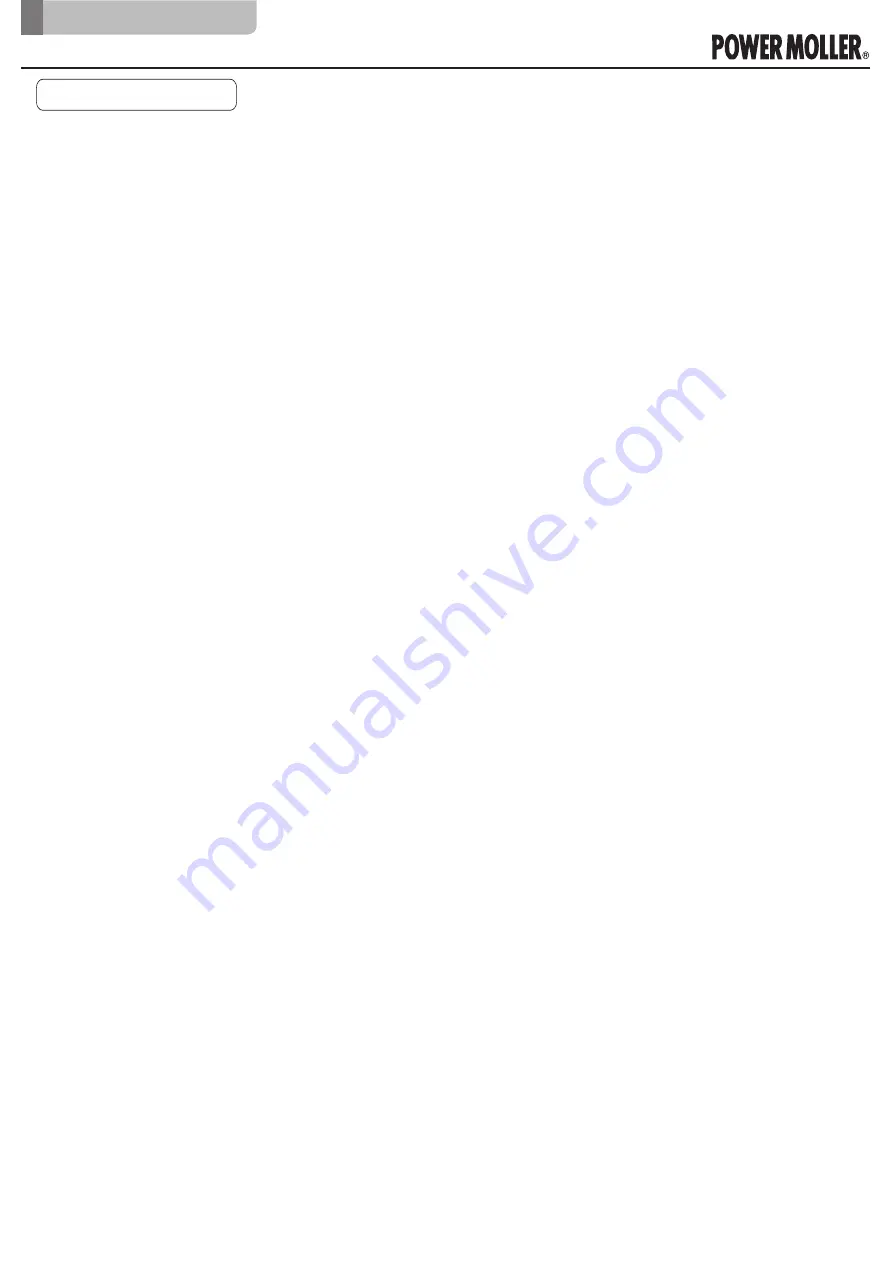
2.4 When a motor does not run
Check the following items in numerical order.
(1) Checking errors
Check the error status of the IB with iCEP or PLC.
1. Check with error monitor in iCEP. Refer to “iCEP User Manual” .
2. Check with PROFINET I/O in PLC. Refer to “Connecting to the PROFINET capable PLC”
documentation.
3. Check with LED indication on IB board. Refer to “2.2 LED indication on IB board” .
(2) JOG operation (Forcible operation)
Perform a forcible operation of the motor by JOG Control of iCEP.
Check the wiring of motor if the motor still does not run. If the wiring is correct, the motor is
broken.
Contact your local distributor.
* JOG operation cannot be performed from PLC.
(3) Checking sensor wiring
This section is only for motors controlled by the condition of a sensor input.
Check that Sensor LED on IB is lighted when sensor is ON. Check its wiring if the LED is not lighted.
If the wiring is correct, replace the sensor with new one. The IB is broken if the LED is not
lighted by sensor ON even after replacement. Contact your local distributor.
* Only PNP type sensor can be used.
(4) Checking Property setting
Check the following property settings with iCEP or PLC.
○
Motor Port Setting
Motor is not driven when “Motor Port” is selected in the settings.
○
Motor Type Setting
Motor is not driven when “N/A” is selected in the settings.
○
Master / Slave Setting
With master setting, motor is driven by ladder logics of own IB.
With slave setting, motor is driven by commands from its master (other IB or PLC).
(5) Checking the write status of ladder logic
○
IB ladder logic
Use the Information screen in iCEP to check the ladder logic name and the build date, and
confirm the intended ladder logic has been written.
○
PLC ladder logic
Follow the PLC manufacturer’s instructions to confirm the program is running correctly.
Original notice - A1.2
20
When a motor doesn not run
IB-P05 Technical documentation
2. Troubleshooting