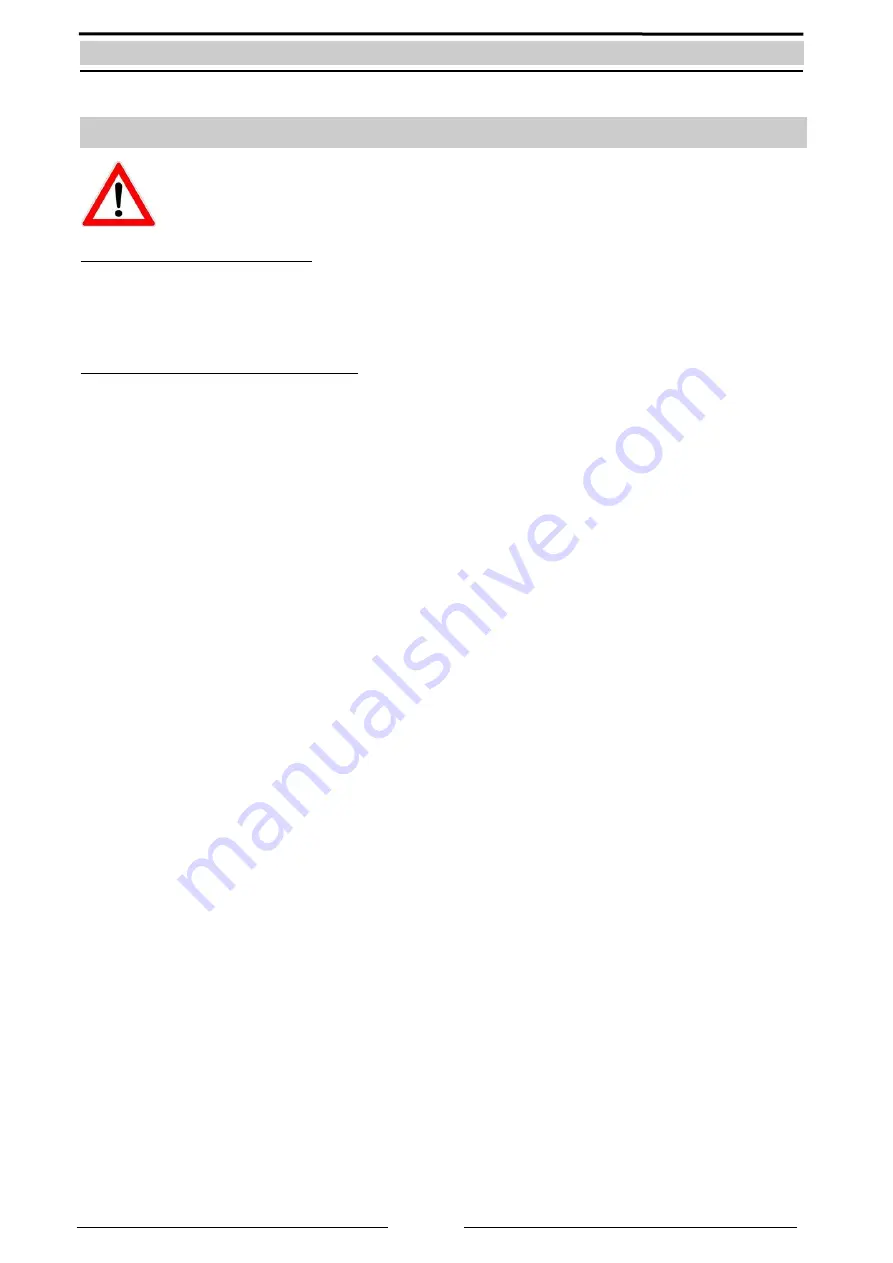
40
11.5 Blower
AQUALOOP blowers are oil less. Never lubricate them.
All blowers have already been precisely adjusted. Never disassemble them.
(Do not try to loosen the hex. bolts on the endcap)
Time to replace the Filter Element
It is recommended that the Filter Element(s) is cleaned or replaced with new one(s) depending on the
extent of its deterioration as determined by the atmospheric conditions particular to each installation.
The filter element(s) should be checked every three months and should be replaced yearly.
Detailed information can be found in the separate blower instruction manual (MEDO LA Blower).
Piston Set Assembly replacement period
It is suggested that the Piston Set Assembly is replaced every 24 months or after 20,000 h depending on
the deterioration of the blower´s pressure and airflow delivery.
There is a groove on each Teflon Seal of the Piston indicating the degree of wear. If one or both grooves
are worn away, replacement of the Piston Set Assembly is recommended.
Detailed information can be found in the separate blower instruction manual which is forwarded with
the blowers.