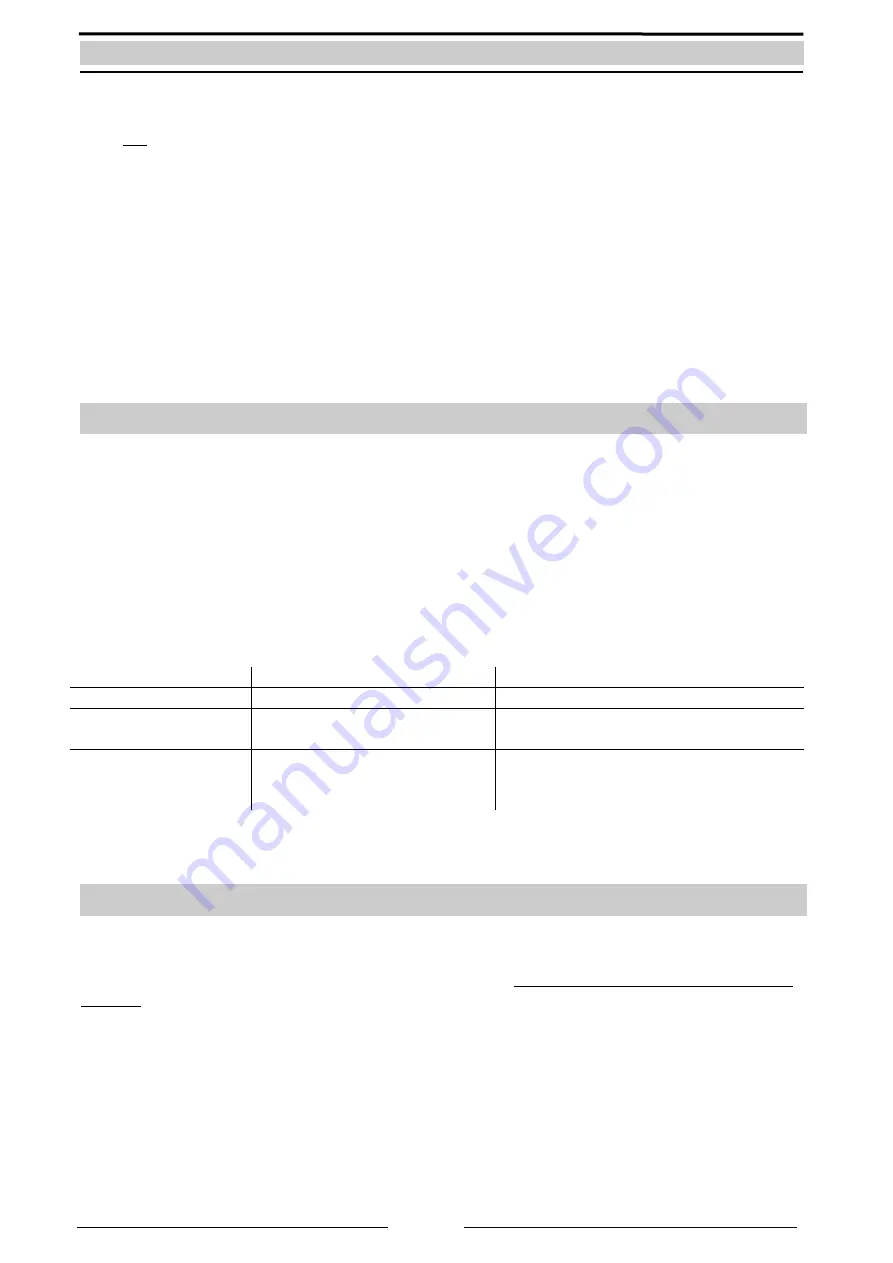
6
Attention:
a.)
Do
not
loosen
the
large
dark
grey
nuts
located
at
the
top
to
open
the
membrane.
The
reassembling
of
the
cartridge
is
very
difficult
without
specialised
tools.
b.)
After
cleaning
please
check,
that
the
external
ring
is
locked
in
the
LOCK
position!
The
hollow
fibres
are
now
exposed
and
can
be
carefully
washed
with
a
water
jet.
Note:
Damaged
or
cracked
fibers
can
simply
be
knotted
by
the
Installer
to
seal
them
and
the
membrane
will
then
pass
the
leakage
test
for
quality
assurance.
1.6.2
Chemical
cleaning
Chemical
cleaning
dissolves
biological
build
‐
up
(fouling)
and
mineral
deposits
(calcium)
accumulated
on
the
hollow
fibres.
Chemical
cleaning
is
done
only
if
the
flow
is
severely
reduced
<
0.22
L/min
=
(300
L/day/MEM).
Chemical
cleaning
of
the
membrane
cartridge
may
be
done
in
two
ways:
In
‐
Situ,
directly
in
the
bioreactor
(usual
method)
Intensive,
in
a
separate
cleaning
container
The
main
differences
between
the
two
cleaning
possibilities
are:
In
‐
Situ
cleaning
Intensive
cleaning
Cleaning
time
2
hrs
12
‐
24
hrs.
Cleaning
result
(greywater
application)
Depends
on
the
initial
state
of
the
membrane
up
to
1.5
L/min
Independent
of
the
initial
state
of
the
membrane
up
to
2.0
L/min
Required
accessories
Filtration
cleaning
connection
and
chemical
container
Separate
cleaning
container,
container
size
depends
on
the
number
of
membranes
on
the
membrane
station
1.6.2.1
In
‐
Situ
cleaning
in
the
bioreactor
(usual
method)
Description:
The
AQUALOOP
membrane
station
remains
in
the
bioreactor.
For
each
membrane,
2
litres
of
cleaning
solution
are
poured
into
the
backwash
tank.
With
a
semi
‐
automatic
cleaning
process
controlled
by
the
controller,
the
membranes
are
cleaned
for
one
hour.
After
flushing
with
clear
water,
the
cleaning
process
is
finished
(see
process
below).
Note:
Throughout
the
chemical
cleaning
cycle,
the
growth
bodies
can
remain
in
the
tank,
the
amount
of
chlorine
used
does
not
affect
the
bacteria
on
the
growth
media,
as
it
removes
only
the
biological
build
‐
up
within
the
membrane.
However,
it
is
important
that
the
amount
of
chlorine
used
should
not
be
higher
than
directed
(s.
section
1.6.3).