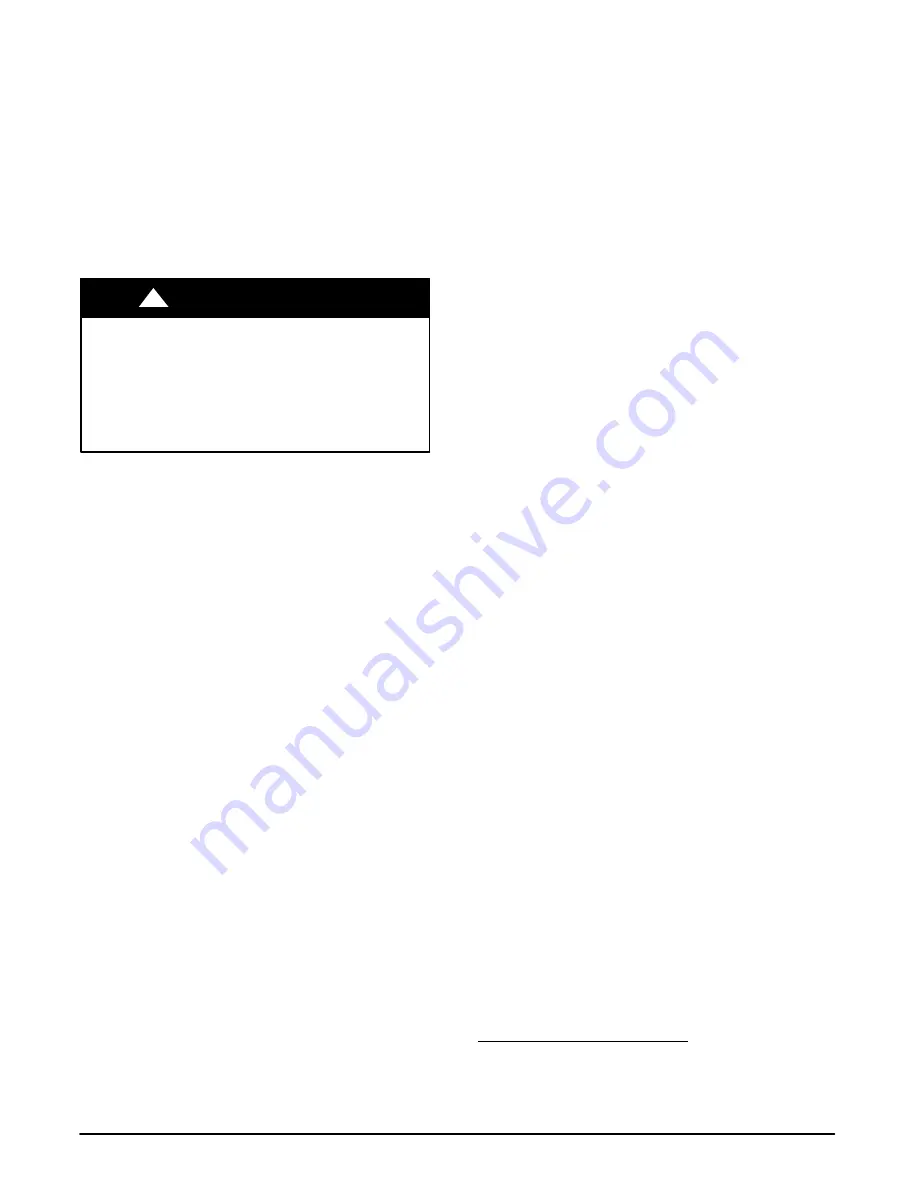
440 04 6000 00
17
Specifications subject to change without notice.
c. Inspect igniter for signs of damage or failure.
d. If replacement is required, remove the screw that
secures the igniter on igniter bracket and remove the
igniter.
6. To replace igniter and bracket assembly, reverse
items 5a through 5d.
7. Reconnect igniter harness to the igniter, dressing the
igniter wires to ensure there is no tension on the
igniter itself. (See Figure 14.)
8. Turn on gas and electrical supplies to furnace.
9. Verify igniter operation by initiating control board self
−
test feature or by cycling thermostat.
10. Replace control door.
Flushing Collector Box and Drainage System
ELECTRICAL SHOCK AND FIRE HAZARD
Failure to follow this warning could result in personal
injury, death, and/or property damage.
Turn off the gas and electrical supplies to the furnace
and install lockout tag before performing any
maintenance or service. Follow the operating
instructions on the label attached to the furnace.
!
WARNING
1. Turn off gas and electrical supplies to furnace.
2. Remove control door.
3. Disconnect pressure switch tube from pressure
switch port.
NOTE
: Ensure the pressure switch tube disconnected from
the pressure switch is higher than the collector box opening
or water will flow out of tube.
4. Remove the collector box plug from the top port on
the upper corner of the collector box. (See Figure 10)
5. Attach a funnel with a flexible tube to port on the
collector box.
6. Flush inside of collector box with water until discharge
water from condensate trap is clean and runs freely.
7. Repeat steps 4 thru 6 with middle plug on upper
corner of collector box.
8. Remove the pressure switch tube from the collector
box.
NOTE
: Do
NOT
blow into tube with tube connected to the
pressure switch.
9. Clean pressure switch port on collect box with a small
wire. Shake any water out of pressure switch tube.
10. Reconnect tube to pressure switch and pressure
switch port.
11. Remove the relief tube from the port on the collector
box and the trap.
12. Clean the relief port on collect box and the trap with a
small wire. Shake any water out of the tube.
13. Reconnect relief tube to trap and collector box ports.
Cleaning Condensate Drain and Trap
NOTE
: If the condensate trap is removed, a new gasket
between the trap and collector box is required. Verify a
condensate trap gasket is included in the service kit or
obtain one from your local distributor.
1. Disconnect power at external disconnect, fuse or
circuit breaker.
2. Turn off gas at external shut-off or gas meter.
3. Remove control door and set aside.
4. Turn electric switch on gas valve to OFF.
5. Disconnect external drain from condensate drain
elbow or drain extension pipe inside the furnace and
set aside.
6. Disconnect the condensate trap relief hose from
collector box port and condensate trap.
NOTE
: If condensate has a heat pad attached to the trap,
trace the wires for the pad back to the connection point and
disconnect the wires for the heat pad.
7. Remove the screw that secures the condensate trap
to the collector box, remove the trap and set aside.
8. Remove the trap gasket from the collector box if it did
not come off when the trap was removed.
9. Discard the old trap gasket.
10. Rinse condensate trap in warm water until trap is
clean.
11. Flush condensate drain lines with warm water.
Remember to check and clean the relief port on the
collector box.
12. Shake trap dry.
13. Clean port on collector box with a small wire.
To re-install Condensate Drain and Trap:
1. Remove adhesive backing from condensate trap
gasket
2. Install gasket on collector box
3. Align the condensate trap with the drain opening on
the collector box and secure the trap with the screw
4. Attach the relief hose to the relief port on the
condensate trap and collector box.
5. Secure tubing to prevent any sags or traps in the
tubing.
6. Connect condensate drain elbow or drain extension
elbow to the condensate trap
7. Connect the leads of the condensate heat pad (if
used)
8. Connect external drain piping to the condensate drain
elbow or drain extension pipe.
9. Turn gas on at electric switch on gas valve and at
external shut-off or meter
10. Turn power on at external disconnect, fuse or circuit
breaker.
11. Run the furnace through two complete heating cycles
to check for proper operation
12. Install control door when complete.
Checking Heat Pad Operation (If Applicable)
In applications where the ambient temperature around the
furnace is 32
_
F (0
_
C) or lower, freeze protection measures
are required. If this application is where heat tape has been
applied, check to ensure it will operate when low
temperatures are present.
NOTE
: The Heat Pad, when used, should be wrapped
around the condensate drain trap. There is no need to use
heat tape within the furnace casing. Most heat tapes are
temperature activated, and it is not practical to verify the
actual heating of the tape. Check the following:
1. Check for signs of physical damage to heat tape such
as nicks, cuts, abrasions, gnawing by animals, etc.
2. Check for discolored heat tape insulation. If any
damage or discolored insulation is evident, replace
heat tape.
3. Check that heat tape power supply circuit is on.
Cleaning Heat Exchangers
The following items must be performed by a qualified
service technician.