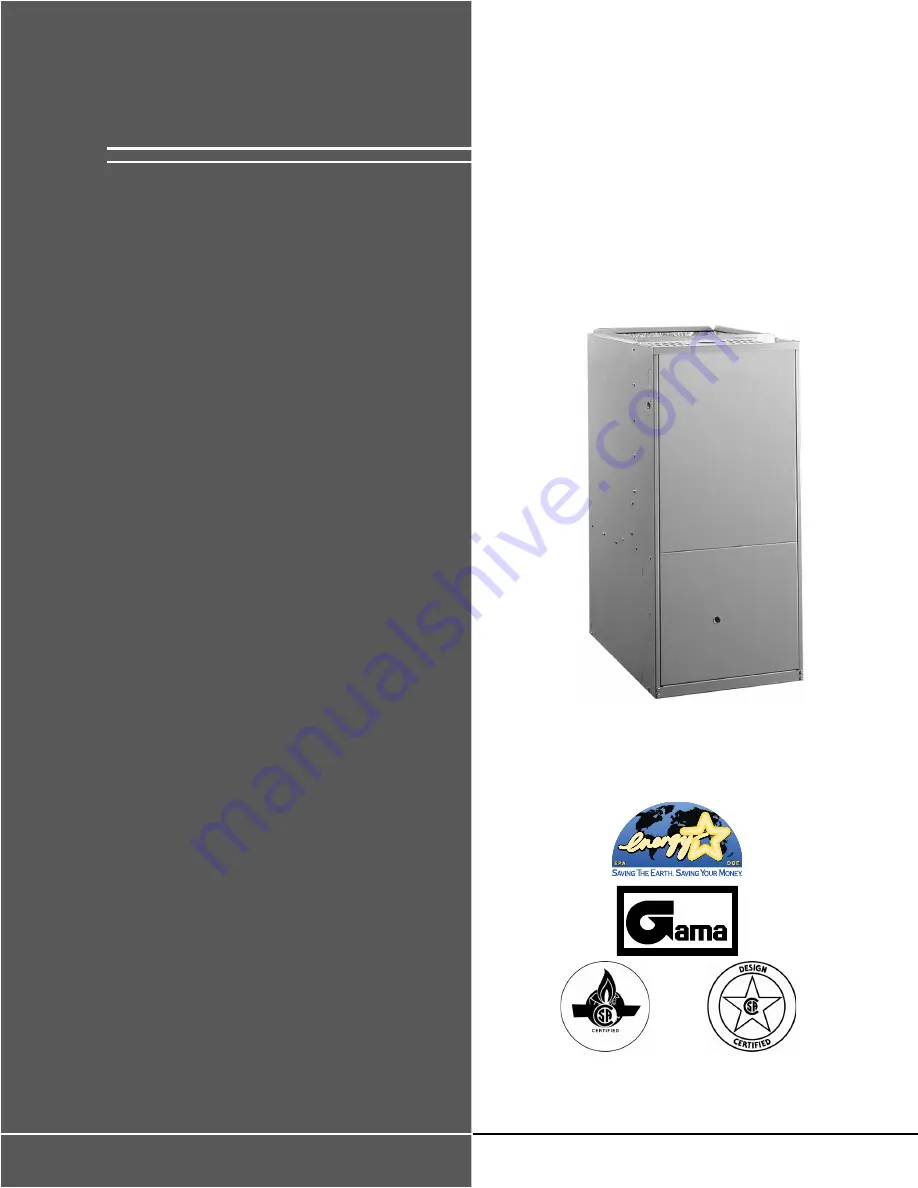
CONTENTS
GENERAL INFORMATION . . . . . . . . . . . . . . . . . . . . . . . 2
SPECIFIC UNIT INFORMATION . . . . . . . . . . . . . . . . . . 3
DUCTWORK . . . . . . . . . . . . . . . . . . . . . . . . . . . . . . . . . . 7
GAS PIPING . . . . . . . . . . . . . . . . . . . . . . . . . . . . . . . . . 11
ELECTRICAL POWER CONNECTION . . . . . . . . . . . . 12
ELECTRICAL CONTROL CONNECTIONS . . . . . . . . . 13
COMBUSTION AIR AND VENT SYSTEM . . . . . . . . . . 14
CONDENSATE PIPING . . . . . . . . . . . . . . . . . . . . . . . . 24
SAFETY CONTROLS . . . . . . . . . . . . . . . . . . . . . . . . . . 25
START-UP AND ADJUSTMENTS . . . . . . . . . . . . . . . . 26
FURNACE ACCESSORIES . . . . . . . . . . . . . . . . . . . . . 31
OPERATION AND MAINTENANCE . . . . . . . . . . . . . . . 33
TROUBLESHOOTING . . . . . . . . . . . . . . . . . . . . . . . . . 36
INSTALLATION
INSTRUCTION
CAUTION: READ ALL SAFETY GUIDES BEFORE YOU
START TO INSTALL YOUR FURNACE.
SAVE THIS MANUAL
HIGH EFFICIENCY
GAS-FIRED FURNACES
TUBULAR HEAT EXCHANGER SERIES
MODELS: P*UR / G9T-UP / FG9-UP (Upflow)
40 - 140 MBH INPUT
MODELS: P*DH / G9T-DH / FG9-DH (Downflow / Horizontal)
40 - 120 MBH INPUT
035-17477-001 Rev. A (801)
EFFICIENCY
RATING
CERTIFIED