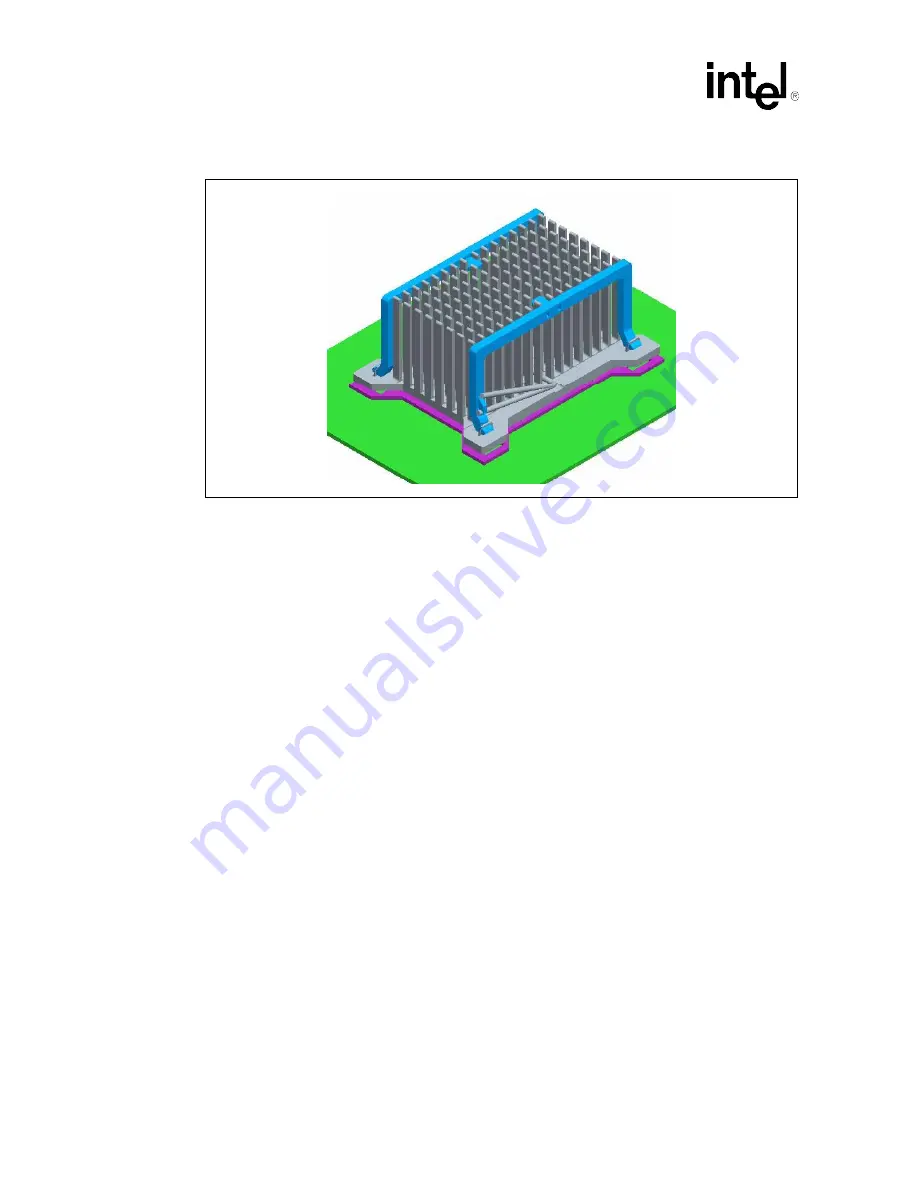
Reference Thermal Solution
26
Intel
®
E7230 Chipset Memory Controller Hub (MCH)
Thermal/Mechanical Design Guide
6.5.2
Extruded Heatsink Profiles
The reference thermal solution uses an extruded heatsink for cooling the chipset MCH.
Figure 6-6
shows the heatsink profile.
Appendix A
lists a supplier for this extruded heatsink. Other heatsinks
with similar dimensions and increased thermal performance may be available. Full mechanical
drawing of this heatsink is provided in
Appendix B
.
6.5.3
Mechanical Interface Material
There is no mechanical interface material associated with this reference solution.
6.5.4
Thermal Interface Material
A thermal interface material (TIM) provides improved conductivity between the die and heatsink.
The reference thermal solution uses Chomerics T-710*, 0.127 mm (0.005 in.) thick, 15 mm x 15
mm (0.60 in. x 0.60 in.) square.
Note:
Unflowed or “dry” Chomerics T710 has a material thickness of 0.005 inch. The flowed or “wet”
Chomerics T710 has a material thickness of ~0.0025 inch after it reaches its phase change
temperature.
6.5.4.1
Effect of Pressure on TIM Performance
As mechanical pressure increases on the TIM, the thermal resistance of the TIM decreases. This
phenomenon is due to the decrease of the bond line thickness (BLT). BLT is the final settled
thickness of the thermal interface material after installation of heatsink. The effect of pressure on
the thermal resistance of the Chomerics T710 TIM is shown in
Table 6-1
. The heatsink clip
provides enough pressure for the TIM to achieve a thermal conductivity of 0.17°C inch
2
/W.
Figure 6-5. Plastic Wave Soldering Heatsink Assembly