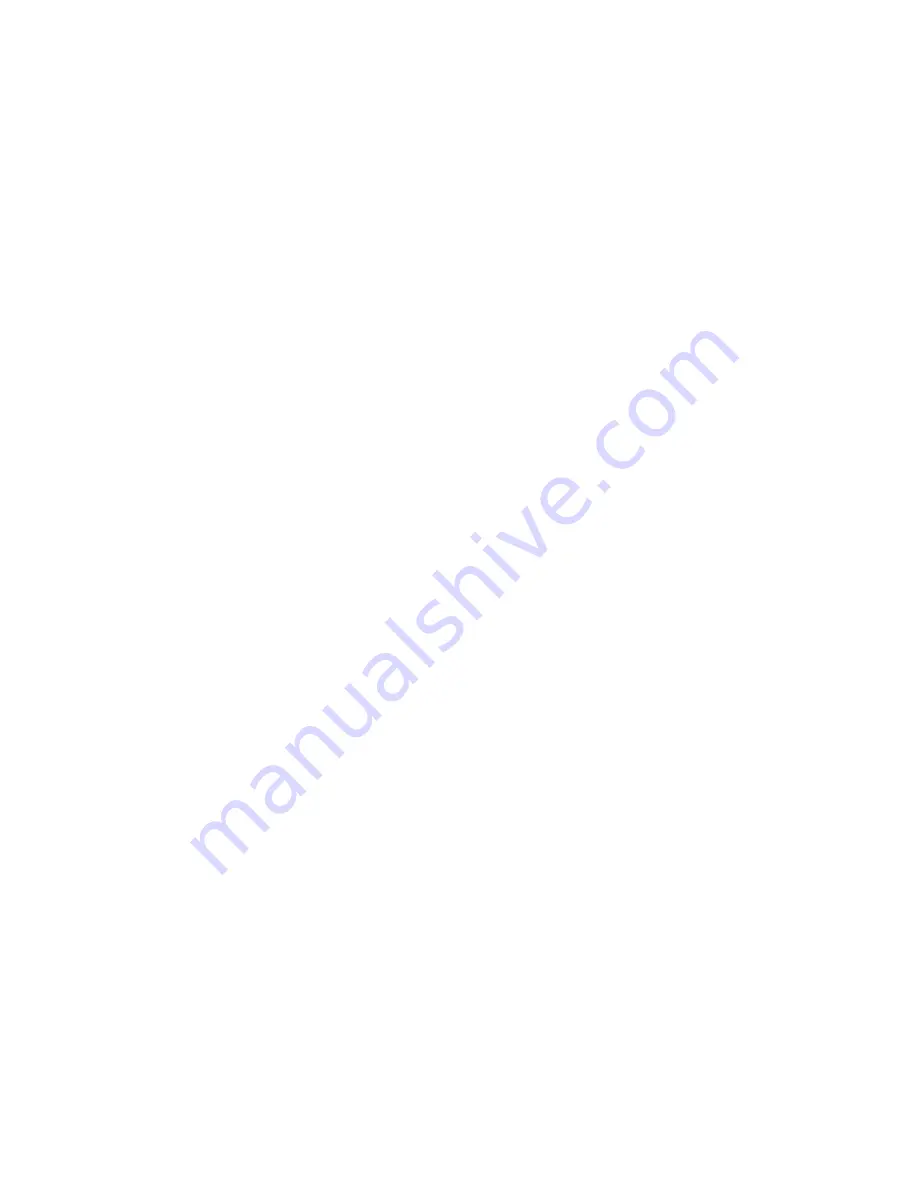
15
2.5 OUTDOOR SHELTERED INSTALLATION
Many times a compressor must be installed outside due
to jobsite conditions or limited space within a
manufacturing facility. When this occurs there are certain
items that should be incorporated into the installation to
help ensure trouble free operation. These items have
been listed below plus Figure 2.5-1 has been included to
show a typical outdoor sheltered installation. The unit
must be purchased with the Outdoor Modification Option
to provide NEMA 4 electrics, TEFC motor, and a cabinet
exhaust on the side of the unit rather than the top to
prevent recirculation of cooling air.
■
The compressor should be on a concrete pad
designed to drain water away. If the concrete pad is
sloped, then the compressor must be leveled. In order
to properly pull cooling air through the enclosure, the
base/skid must be sealed to the concrete pad.
■
The roof of the shelter should extend a minimum of
4 ft (1.2 m) around all sides of the compressor to pre-
vent direct rain and snow from falling on the unit.
■
Air-cooled machines must be arranged under the
shelter in a way that prevents air recirculation (i.e. hot
exhaust back to the package inlet).
■
If the installation includes more than one compressor,
the hot air exhaust should not be directed towards the
fresh air intake of the second unit or an Air Dryer.
■
If a standard machine is to be installed outside, the
ambient temperature must never drop below 35°F
(1.7°C).
■
If ambient temperature drops below 35°F (1.7°C) to as
low as –10°F (–23°C) the unit must be supplied with
the Low Ambient Option. Installations below –10°F
(–23°C) ambient are not recommended. The Low
Ambient Option requires a separate power source to
operate internal heaters.
■
Arrange the machine with the Intellisys con-
troller/starter enclosure facing away from the sun as
radiant heat can affect starter/lntellisys performance.
Also direct sunlight and UV rays will degrade the
membrane touch panel. This is not a warrantable
situation.
■
Power disconnect switch should be within line of sight
and in close proximity to the unit. N.E.C. and local
electrical codes must be followed when installing the
power disconnect switch.
■
Condensate drains must never be allowed to drain on
the ground. Run to a suitable sump for future
collection and disposal or separation of lubricant and
water mixture.
■
Incoming power connections must use suitable
connectors for outdoor weather tight service.
■
A minimum of 3 ft (.9 m) clearance must be allowed
on all four sides of the unit for service access.
However 42” (1.06m), or minimum required by latest
NEC or applicable local code, must be maintained in
front of starter box door.
■
If possible, access by a forklift and/or an overhead
beam hoist should be kept in mind (for eventual
service to airend or motor).
■
If the area around the installation contains fine
airborne dust or lint and fibers etc., then the unit
should be purchased with the High Dust Filter Option.
■
Some type of protection such as a fence or security
system, should be provided to prevent unauthorized
access.
Summary of Contents for EP 60
Page 18: ...16 FIGURE 2 5 1 TYPICAL OUTDOOR SHELTERED INSTALLATION ...
Page 31: ...29 NOTES ...
Page 44: ...42 7 0 REFERENCE DRAWINGS 7 1 ELECTRICAL SCHEMATIC FULL VOLTAGE 39899794 REV 02 ...
Page 45: ...43 7 2 ELECTRICAL SCHEMATIC STAR DELTA 39899786 REV 02 ...
Page 46: ...44 7 3 FOUNDATION PLAN AIR COOLED 39894472 REV 03 ...
Page 47: ...45 7 4 FOUNDATION PLAN WATER COOLED 39907894 REV 03 ...
Page 48: ...46 7 5 FOUNDATION PLAN OUTDOOR MOD 39907886 REV 03 ...
Page 49: ...7 6 BASIC FLOW SCHEMATIC AIR COOLED 39899828 REV 02 47 ...
Page 50: ...48 7 7 BASIC FLOW SCHEMATIC WATER COOLED 39899836 REV 02 ...
Page 51: ...49 7 8 TYPICAL SYSTEM FLOW DIAGRAMS TYPICAL SYSTEM FLOW DIAGRAM ...
Page 52: ...50 7 8 TYPICAL SYSTEM FLOW DIAGRAMS ...
Page 53: ...51 7 8 TYPICAL SYSTEM FLOW DIAGRAMS ...
Page 54: ...52 7 8 TYPICAL SYSTEM FLOW DIAGRAMS ...
Page 55: ...53 7 8 TYPICAL SYSTEM FLOW DIAGRAMS ...
Page 59: ...57 DATE RUN TIME WORK DONE QTY UNIT WORK HOURS MEASURE BY 9 0 MAINTENANCE RECORD ...
Page 60: ...DATE RUN TIME WORK DONE QTY UNIT WORK HOURS MEASURE BY MAINTENANCE RECORD 58 ...
Page 61: ...59 DATE RUN TIME WORK DONE QTY UNIT WORK HOURS MEASURE BY MAINTENANCE RECORD ...
Page 62: ...60 DATE RUN TIME WORK DONE QTY UNIT WORK HOURS MEASURE BY MAINTENANCE RECORD ...