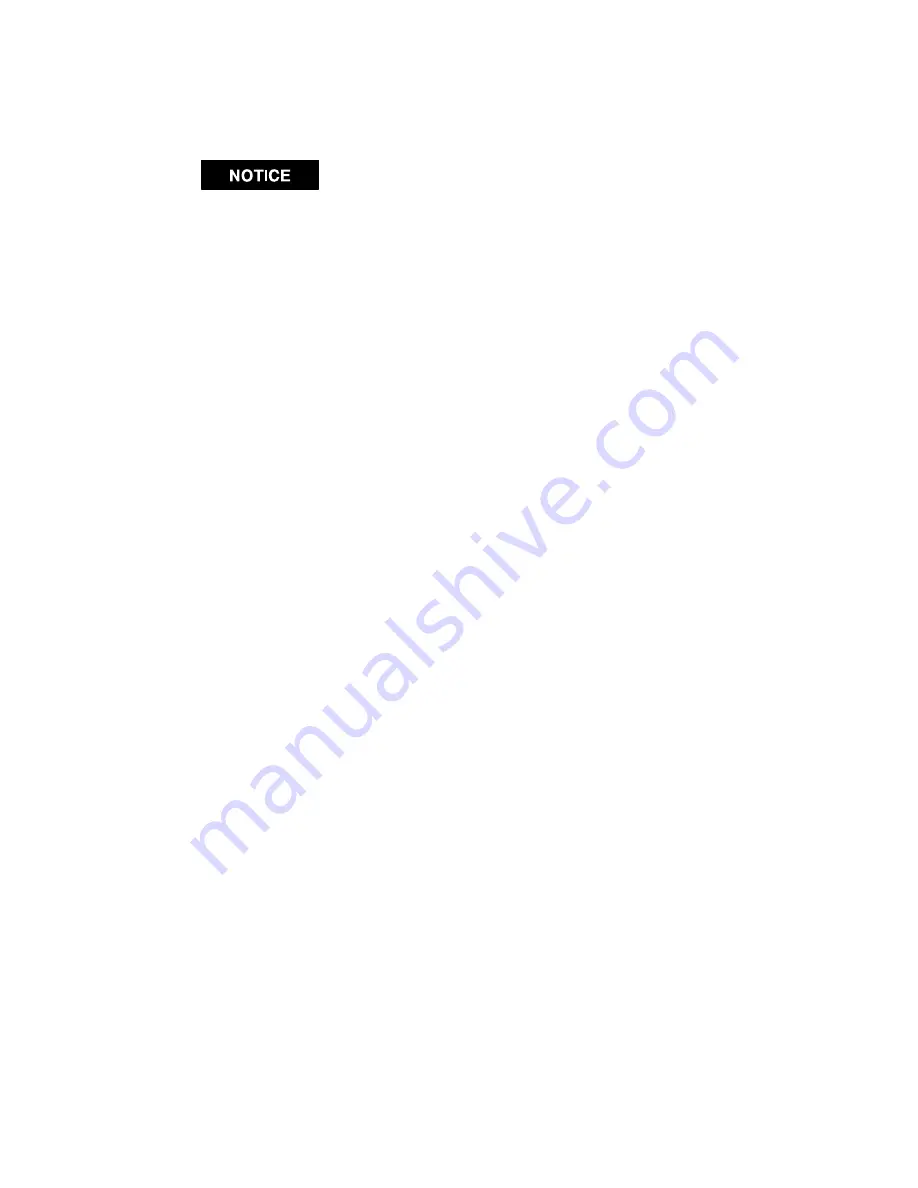
16
MAINTENANCE SECTION
Assembly of the Motor
1.
Lightly clamp Motor Housing (25) in copper–covered
or leather–covered vise jaws with handle end upward.
Excessive clamping pressure will distort the Motor
Housing and make motor installation extremely
difficult. Do not insert the hammer case end of the
Motor Housing more than 1” (25 mm) into the vise
jaws.
2
.
Coat inside surface of Housing and outer edge of
Front End Plate (22) with a light film of oil.
3.
Using a long tee hex wrench as an alignment pin,
insert Front End Plate, copper face trailing, into
Motor Housing. Align dowel hole in End Plate with
dowel hole at the bottom of motor bore.
4.
Lubricate and insert a new fiber Air Port Gasket
Retainer (28) in one of the air ports inside Motor
Housing.
5.
Install an Air Port Gasket (27) in air port against
Gasket Retainer with flat end of Gasket away from
Retainer.
6.
Repeat Steps 4 and 5 to install remaining Gasket and
Retainer in the other air port.
7.
Coat outside of Cylinder (21) with a light film of oil
and using the long tee hex wrench as an alignment pin
to align holes in Cylinder with holes in Front End
Plate and Housing, insert Cylinder into Housing.
8.
Coat inside of Cylinder and Rotor (19) with a light
film of oil and insert the splined hub of Rotor through
Cylinder into Front End Plate.
9.
Coat each Vane (20) with a light film of oil and insert
a Vane into each slot in the Rotor. Vanes must be
installed with curved edge toward center of Rotor.
Spin the Rotor to settle Vanes into position.
10. Using the long tee hex wrench to align hole in Rear
End Plate (17) with hole in the Cylinder, insert Rear
End Plate, copper face leading, into Motor Housing
against the Cylinder. End Plate is properly seated
when the large trailing face of the End Plate is
slightly below face of Motor Housing.
11. Grease Rear Rotor Bearing (18) and install it in recess
of Rear End Plate.
12. Remove alignment pin from assembled motor and
install Cylinder Dowel (24). The Dowel is properly
seated when end of Dowel does not protrude above
End Plate.
13. Install Motor Clamp Washer (16) against Rear End
Plate so that large outer edge of Washer contacts End
Plate.
Assembly of the Reverse Valve
1. Inject a small amount of grease into hole in Motor
Housing (25) where Reverse Lock Plunger (35) will
be installed. With the grease to hold them in position,
install Reverse Lock Plunger Spring (36) and Lock
Plunger.
2. Install a new Reverse Valve Bushing Seal (38) in the
annular groove on Reverse Valve (37).
3. Coat Reverse Valve with a light film of oil and install
it in Motor Housing with the side hole nearest to the
Seal pointed toward the Rotor (19).
4. Position Reverse Lever (34) on Reverse Valve and
while using a thin blade screwdriver to depress the
Reverse Lock Plunger, push Lever onto Reverse
Valve.
5. Place a new Handle Gasket (15) on Motor Housing.
6. Examine Reverse Valve Seal (13) located inside
Handle and if it is nicked, deformed or worn, remove
it and install a new Seal.
7. Fill rotor cavity in Handle with the recommended
grease and position Handle on the Motor Housing.
8. Install four Handle Cap Screws (44) and Lock
Washers (45) and using an alternate tightening
pattern, tighten Screws between 14 and 17 ft–lb
(19 and 27 Nm) torque.
9. Move Reverse Lever through the forward and reverse
positions to make certain the Lever locks in position.
10. Turn assembly in vise jaws and clamp on Handle with
rotor shaft upward.
11. Grease Front Rotor Bearing (23) and place it over
rotor shaft.
12. Select a socket or piece of tubing that will fit over the
outside race of the Bearing and tap it with a hammer
to seat Bearing into Housing.
13. Pack Bearing with additional grease and rotate rotor
shaft. If shaft does not rotate smoothly, rap end of
rotor shaft with a soft hammer to set motor and try to
rotate shaft again.
Summary of Contents for 2934B2SP
Page 10: ...MAINTENANCE SECTION 10 Dwg TPA1249 2...
Page 19: ...19...