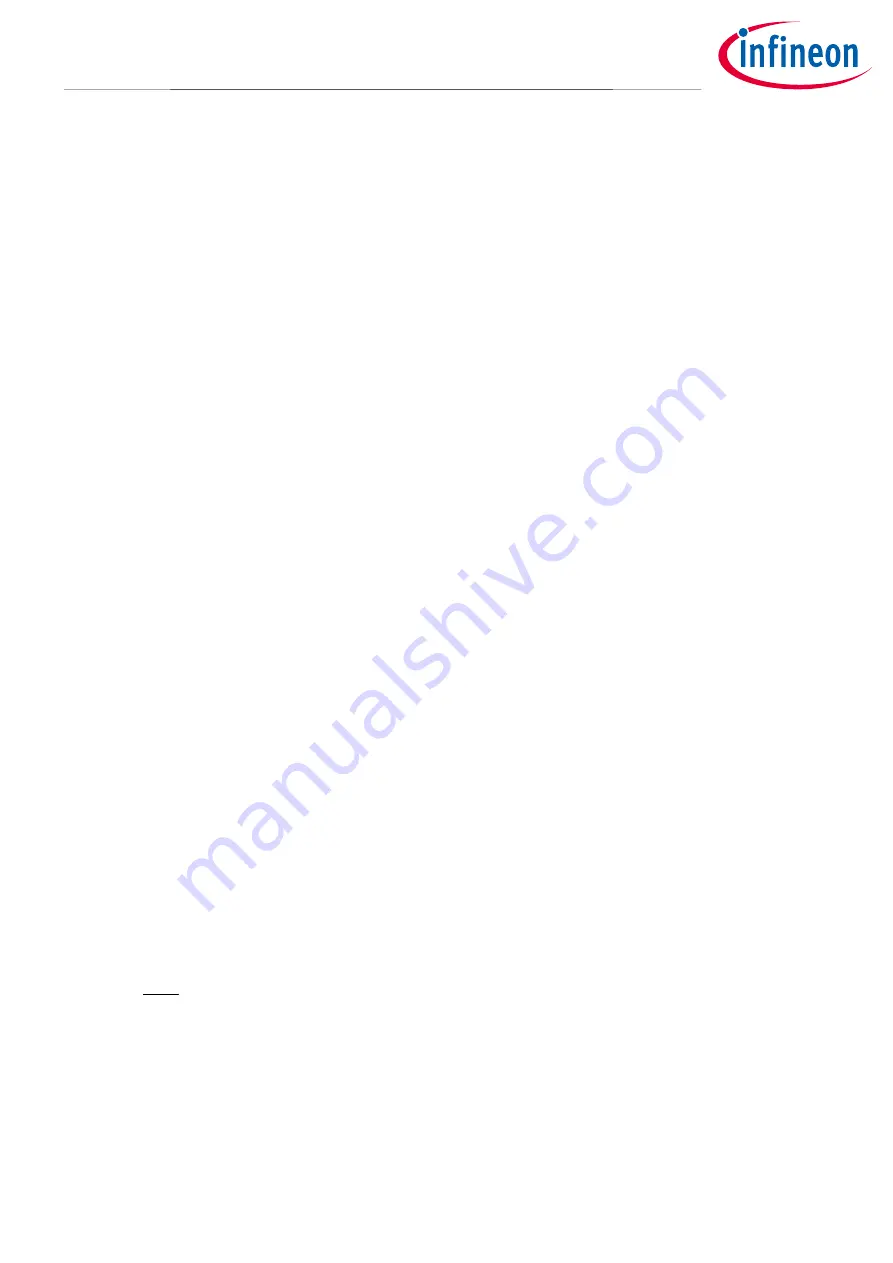
Application Note
43 of 53
V 1.0
2019-04-01
IM393 Application note
IM393 IPM Technical Description
Thermal design
7.5.2
Heat sink characteristics
Heat sinks are characterized by three parameters:
•
Heat transfer from the power source to heat sink
•
Heat transfer within the heat sink (to all the surfaces of the heat sink)
•
Heat transfer from heat sink surfaces to ambient
7.5.2.1
Heat transfer from heat source to heat sink
There are two factors that need to be considered in order to provide a good thermal contact between power
source and heat sink:
•
Flatness of the contact area
−
Due to the unevenness of surfaces, thermal interface material needs to be supplied between heat source
and heat sink. However, such materials have a rather low thermal conductivity (<10 K/W). Hence, these
materials should be as thin as possible. On the other hand, they need to fill up the space between heat
source and heat sink. Therefore, the unevenness of the heat sink should be as low as possible. In addition,
the particle size of the interface material must fit the roughness of the module and the heat sink surfaces.
Particles that are too large will unnecessarily increase the thickness of the interface layer, and hence will
increase thermal resistance. Particles that are too small will not provide a good contact between the two
surfaces, and will lead to higher thermal resistance as well.
•
Mounting pressure
−
The higher the mounting pressure, the better the interface material disperses. Excess interface material
will be squeezed out resulting in a thinner interface layer with lower thermal resistance.
7.5.2.2
Heat transfer within the heat sink
The heat transfer within the heat sink is mainly determined by:
•
Heat-sink material
−
The material needs to be a good thermal conductor. Most heat sinks are made of aluminum (λ
≈
200 W/
(m*K)). Copper is heavier and more expensive, but also nearly twice as efficient (λ
≈
400 W/ (m*K)).
•
Fin thickness
−
If the fins are too thin, the thermal resistance from heat source to fin is too high, and the efficiency of the
fin decreases. Hence, it does not make sense to make the fins as thin as possible to increase the surface
area.
7.5.2.3
Heat transfer from heat sink surface to ambient
The heat transfers to the ambient mainly by convection. The corresponding thermal resistance is defined as
A
α
1
R
conv
th,
⋅
=
(26)
Where α is the heat transfer coefficient and A is the surface area.
Hence there are two important parameters:
•
Surface area:
Heat sinks require a huge surface area in order to easily transfer the heat to the ambient.
However, as the heat source is assumed to be concentrated at a point and not uniformly distributed, the total
thermal resistance of a heat sink does not change linearly with length. Also, increasing the surface area by