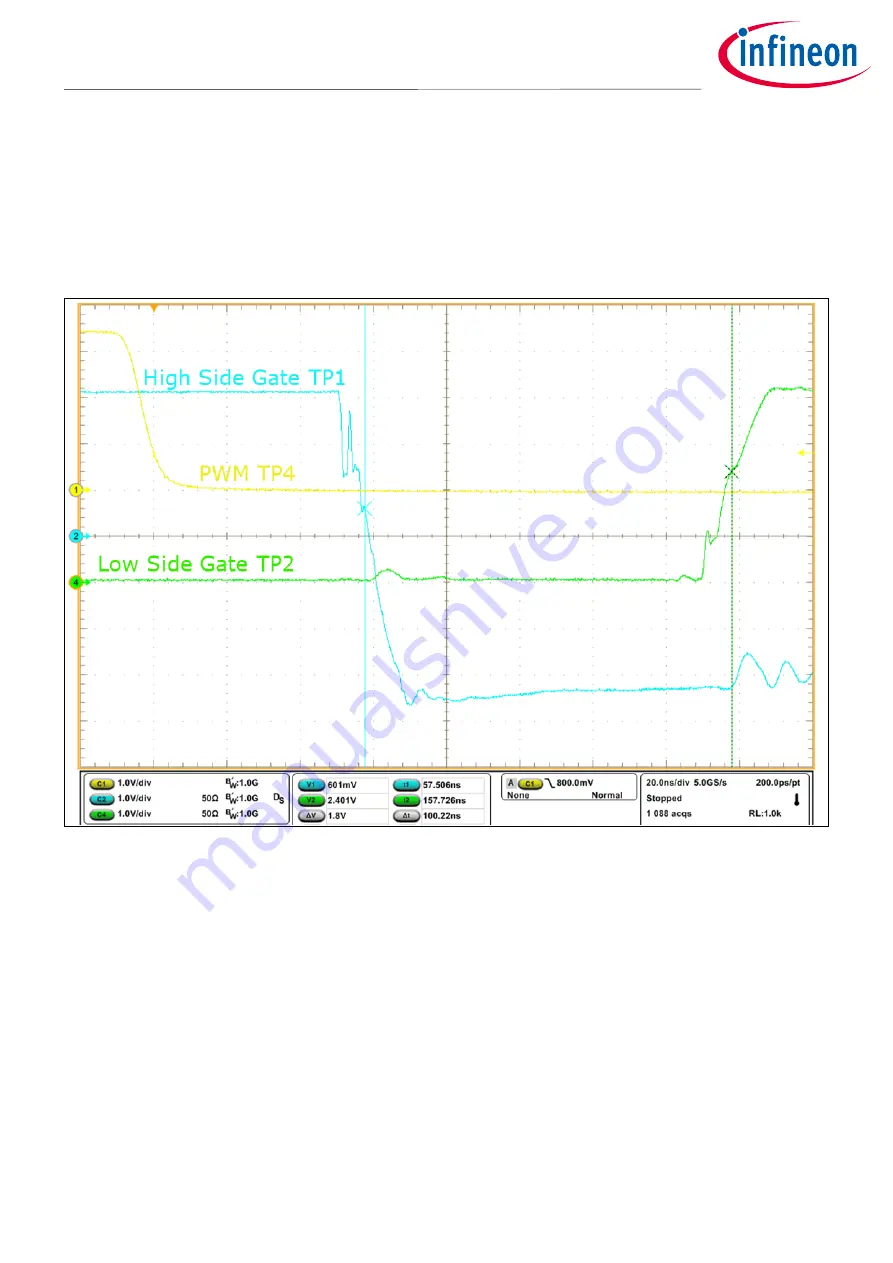
Application Note
15 of 23
V 1.1
2020-11-09
CoolGaN™ 600 V half-bridge evaluation platform featuring GaN
EiceDRIVER™
Setup and use
Apply power to the board and trigger on the rising edge of TP4. You should have a signal that looks similar to
. The cursors assume that turn-off is complete when TP2 crosses 0 V, and turn-on is assumed to begin
when TP1 reaches about 2.5 V. Adjust R11 (trimpot) to achieve the desired deadtime (factory preset is 100 ns).
For the falling edge, set the scope trigger for the negative edge of TP4, and you should see a waveform similar
to
. Adjust trimpot R21 to dial-in the deadtime to the desired value on the falling edge of PWM.
Normally the rising and falling edge deadtimes are set to the same value. Turning the trimpots clockwise
increases the deadtime.
Figure 13
Measuring deadtime on the falling-edge of PWM
4.7
Test inductor recommendation
For best results, it is recommended that a good high-frequency capable inductor is used for testing. We
recommend a Micrometals T200-2B toroidal core, with 34 turns of 14 gauge HPN enameled copper magnet wire
in a single-layer. This provides a very linear, low-loss 25 µH inductor with a self-resonant frequency >20 MHz
and a high saturation current, well beyond the rating of the 70 mΩ GaN peak current rating. While this may not
provide the most space-efficient inductor, it will not “color” the measurement results. Lower performance
inductors may have high self-capacitance and multiple resonaces that can mask or confuse the performance
measuremet of the GaN half-bridge.