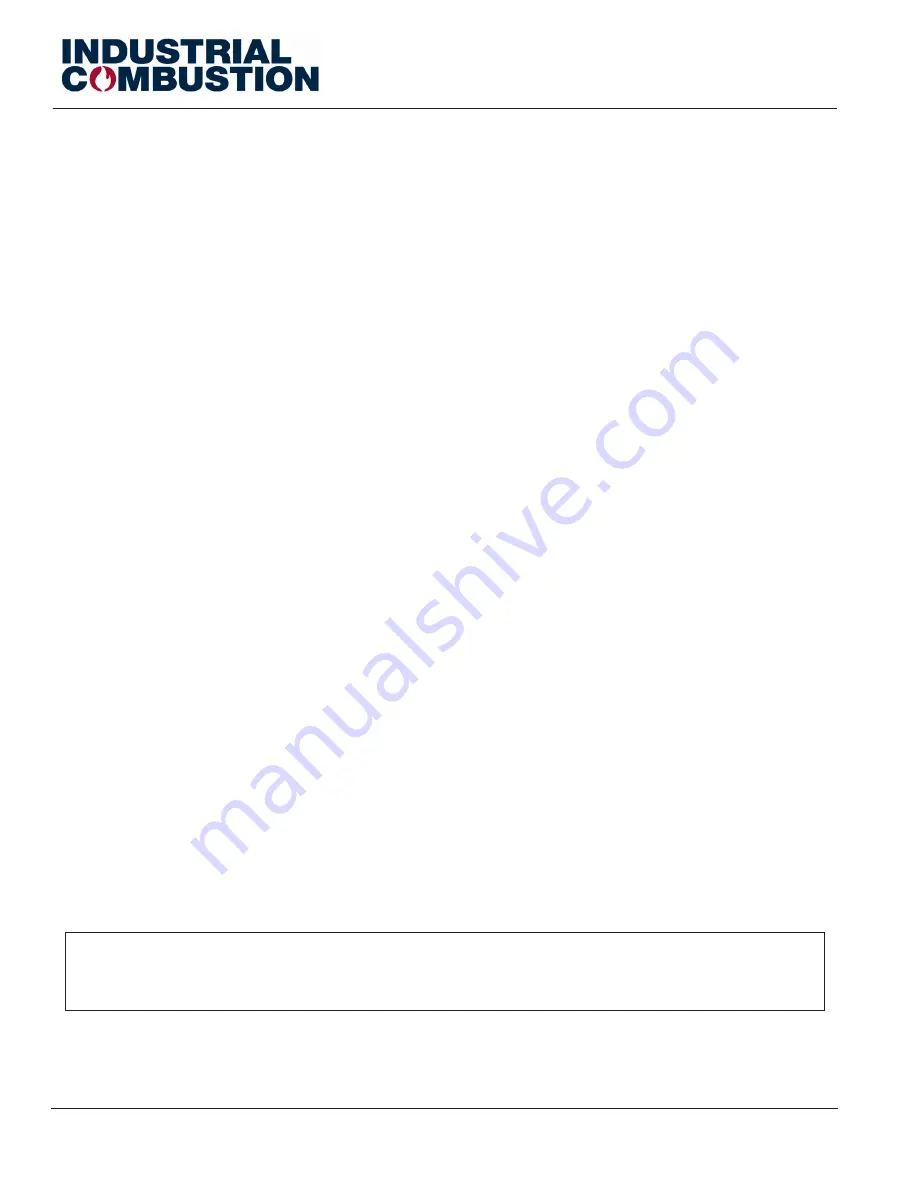
Operation
3-8
IC-SA-1511 (02/2014)
V/LNV Series Manual
2.
Set the “ON-OFF” switch to “ON.” The burner will start and pre-purge. After pre-purge, the ignition
transformer will direct spark. If the flame detector proves the presence of a satisfactory pilot, the
programmer will proceed to main flame ignition.
3.
Make initial air shutter settings for smooth ignition. Return line oil pressure should be set according to
guidelines in Chapter 4. Do not repeat unsuccessful light off attempts without rechecking burner and
pilot adjustment. Vent fuel vapors from the combustion chamber after each unsuccessful light off
attempt. Set the oil low fire rate by adjusting the oil return pressure and air linkage. Using the
combustion analysis instrument, adjust the low fire. Typical combustion analysis for low fire is 5% to 6%
O
2
.
4.
When low fire is adjusted, shut down the burner. Restart several times to be sure the low fire setting is
suitable. Readjust if necessary. Never start the burner with fuel vapor in the furnace. In case of
emergency, open the main power switches and close all fuel valves. After combustion adjustments are
satisfactorily set, allow the heating vessel to slowly reach normal operating pressure or temperature.
5.
After the boiler has reached operating temperature or pressure, turn the potentiometer switch in small
increments to the high fire position. This will cause the metering valve to close, resulting in an increase in
the oil pressure feeding the burner nozzle. In high fire the oil metering valve should be in the fully closed
position and the fuel oil pressure should be about 300 psi. Check high fire at this point using combustion
instruments. High fire combustion analysis typically is 3.5% to 4% O
2
. Verify maximum input rate by
measuring the oil meter if available or by weighing the oil.
The burner should be set up and maintained to yield smoke spot levels less than a #1 spot (ASTM D2156
Shell-Bacharach Scale) to minimize soot buildup in the boiler.
Do not disturb established low fire adjustment. Allow the burner to return to low fire position before
adjusting high or intermediate settings.
When conditions covered above are assured, refer to Sections 3.9 and 3.10.
3.8.3 — Combination Gas-Oil Burners
In general, the combination fueled system is to be started first using oil, because, as a fuel, oil has a greater
combustion air requirement than natural gas.
Refer to the gas burner or oil burner adjustment procedures and Chapter 4.
Once the adjustments are set for oil, shutdown the burner and restart and adjust the natural gas fuel. Do
not readjust the air dampers. The adjustment is made by balancing the fuel input rate against the existing
flow of combustion air.
When conditions covered above are assured, refer to Sections 3.9 and 3.10.
NOTE:
Size 1 & 2 combination gas/oil units use a direct coupling from the blower motor to the oil pump. When
firing gas for an extended period of time, the coupling should be manually removed and replaced only when
firing oil. If the coupling is left connected to the blower motor, ensure that there is proper oil circulation at all
times to avoid damage to and seizure of the pump.