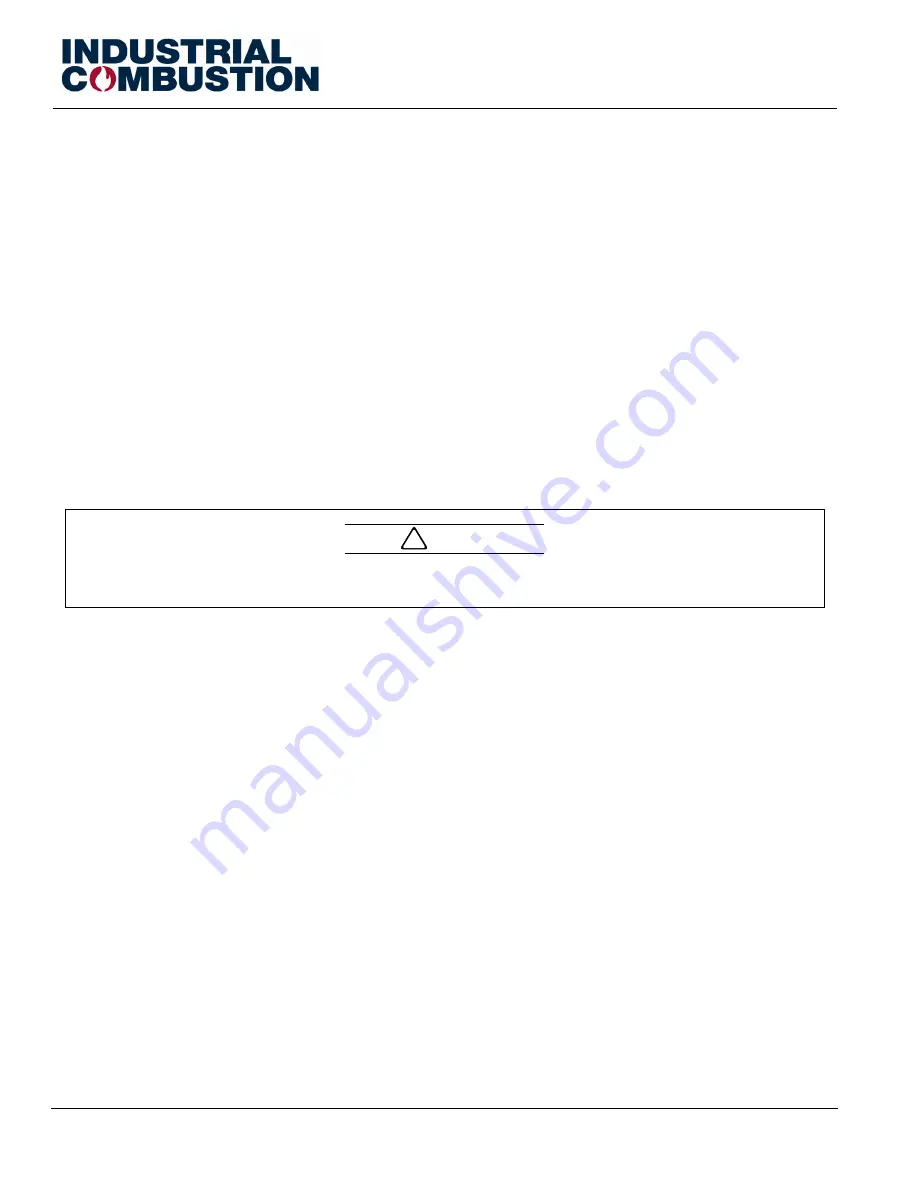
Installation
2-6
IC-SA-1511 (02/2014)
V/LNV Series Manual
Refer to pages 2-2 through 2-5 for combustion chamber dimensions for firetube and watertube boiler
applications. Combustion chamber dimensions should be adequately sized to prevent flame
impingements.
A dry oven refractory is required only to protect surfaces not adequately protected by free circulating water.
Basic objectives include:
•
Provide adequate combustion space
•
Avoid flame impingement
•
Protect surfaces not adequately water cooled
•
Seal openings
The chamber dimensions listed on the following pages are typical for good practice. Satisfactory results
may be achieved with modifications to suit some conditions. Factors such as fuel properties, total
combustion volume, and length of flame travel often make fixed requirements impractical. When in doubt,
consult the factory. Insulation should be provided between the refractory and the boiler base. Mineral wool,
or other material not likely to settle is preferred. The chamber front wall may be constructed of firebrick or
insulating firebrick. Insulation should be used between the refractory and front plate. Firebrick, or insulating
firebrick should be set in high temperature bonding mortar with provision for expansion.
2.5 — Installation
Prepare the boiler front plate as follows:
1.
Determine burner mounting height. Locate and scribe a level horizontal centerline across the mounting
face.
2.
Locate and scribe a vertical centerline. Be sure stud locations line up where studs will have full support.
If they don’t, or if the opening is too large, a steel adapter plate, 3/8” minimum, may be welded or bolted
in place. Suitable anchors should be provided to hold the refractory in place. The adapter plate must be
properly sealed (use insulating rope gasket) to prevent leakage of combustion gases.
3.
Using insulating rope gasket, wrap the rope on the inside of the bolt circle, looping the rope around the
mounting studs.
4.
Set the burner into position for mounting and tighten into place. Standard burners are equipped with a
four-hole mounting flange.
5.
Permanently support the burner using the pipe support connections.
6.
The space between the boiler refractory, water leg, or fire tube and outside diameter of the firing head
must be packed with plastic refractory, Kaiser Refractory Mono T-Air Set or equal. Ram plastic refractory
from front to rear, parallel to the outside surface of the firing head.
The gasket must be resilient to seal any uneven areas between the burner flange and the boiler front plate to
prevent leakage of combustion gases.
!
Caution