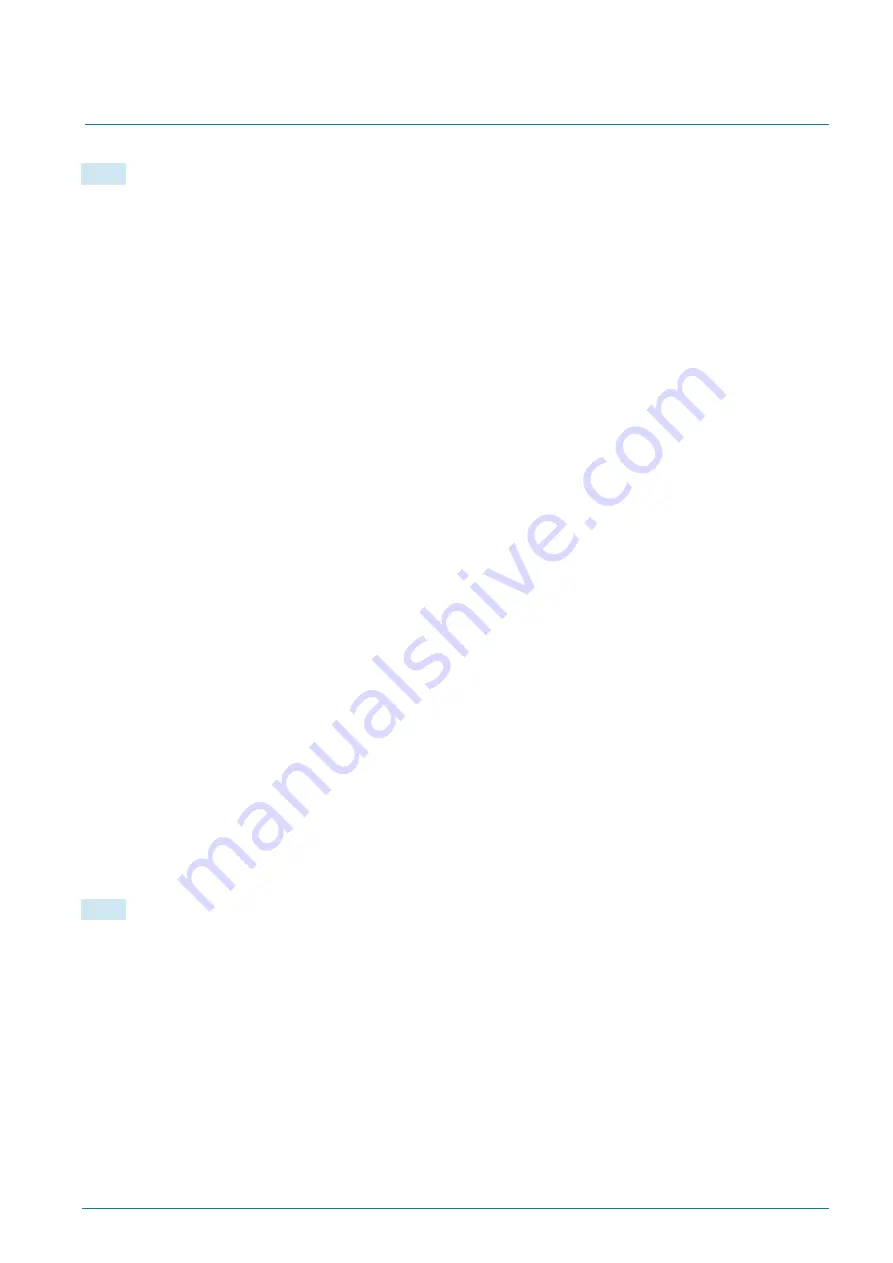
21
5.8 Creating a linear Calibration Curve for a specific Material
The calibration curves Cal1 to Cal15 can be easily created or adapted for specific materials with help of SONO-CONFIG.
Therefore, two measurement points need to be identified with the probe. Point P1 at dried material and point
P2 at moist material where the points P1 and P2 should be far enough apart to get a best possible calibration
curve. The moisture content of the material at point P1 and P2 can be determined with laboratory measurement
methods (oven drying). It is to consider that sufficient material is measured to get a representative value.
Under the menu "Calibration" and the window "Material Property Calibration" the calibration curves CAL1 to
Cal15 which are stored in the SONO probe are loaded and displayed on the screen (takes max. 1 minute). With
the mouse pointer individual calibration curves can be tested with the SONO-probe by activating the button "Set
Active Calib". The measurement of the moisture value (MoistAve) with the associated radar time tpAve at point
P1 and P2 is started using the program SONO-CONFIG in the sub menu "Test" and "Test in Mode CF" (see "Quick
Guide for the Software SONO- CONFIG").
Step 1:
The radar pulse time tpAve of the probe is measured with dried material. Ideally, this takes place during
operation of thedryer in order to take into account possible density fluctuations of the material. It is recommended
to detect multiple measurement values for finding a best average value for tpAve. The result is the first calibration
point P1 (e.g. 70/0). I.e. 70ps (picoseconds) of the radar pulse time tpAve corresponds to 0% moisture content
of the material. But it would be also possible to use a higher point P1´ (e.g. 190/7) where a tpAve of 190ps
corresponds to a moisture content of 7%. The gravimetric moisture content of the material, e.g. 7% has to be
determined with laboratory measurement methods (oven drying).
Step 2:
The radar pulse time tpAve of the probe is measured with moist material. Ideally, this also takes place
during operation of the/dryer. Again, it is recommended to detect multiple measurement values of tpAve for
finding a best average value. The result is the second calibration point P2 with X2/Y2 (e.g. 500/25). I.e. tpAve of
500ps corresponds to 25% moisture content. The gravimetric moisture content of the material, e.g. 25% has to be
determined with laboratory measurement methods (oven drying).
Step 3:
With the two calibration points P1 and P2, the calibration coefficients m0 and m1 can be determined for
the specific material (see next page).
Step 4:
The coefficients m1 = 0.0581 and m0 = -4.05 (see next page) for the calibration curve Cal14 can be entered
directly and are stored in the probe by pressing the button “Set”. The name of the calibration curve can also be
edited. The selected calibration curve (e.g. Cal14) which is activated after switching on the probes power supply
will be adjusted with the button "Set Default Calib”.
Attention:
Use “dot” as separator (0.0581) in SONO-CONFIG, not comma!
5.9 Calculation for a linear 2-point calibration curve
1. Download the Excel-Sheet „SONO 2-Point LinearCalibration_Calculation“ from IMKO´s Homepage /DOWNLOADS/
SOFTWARE.
2. Enter into the Excel-Sheet both TP-values with the respective reference moisture values.
3. Read out both parameters m0 and m1 from the Excel-Sheet.
4. Enter, set and save both parameters m0 and m1 with help of the software „SONO-CONFIG“ in the menu
„Calibration“ in the window „Material Property Calibration“ in the selected calibration curve.