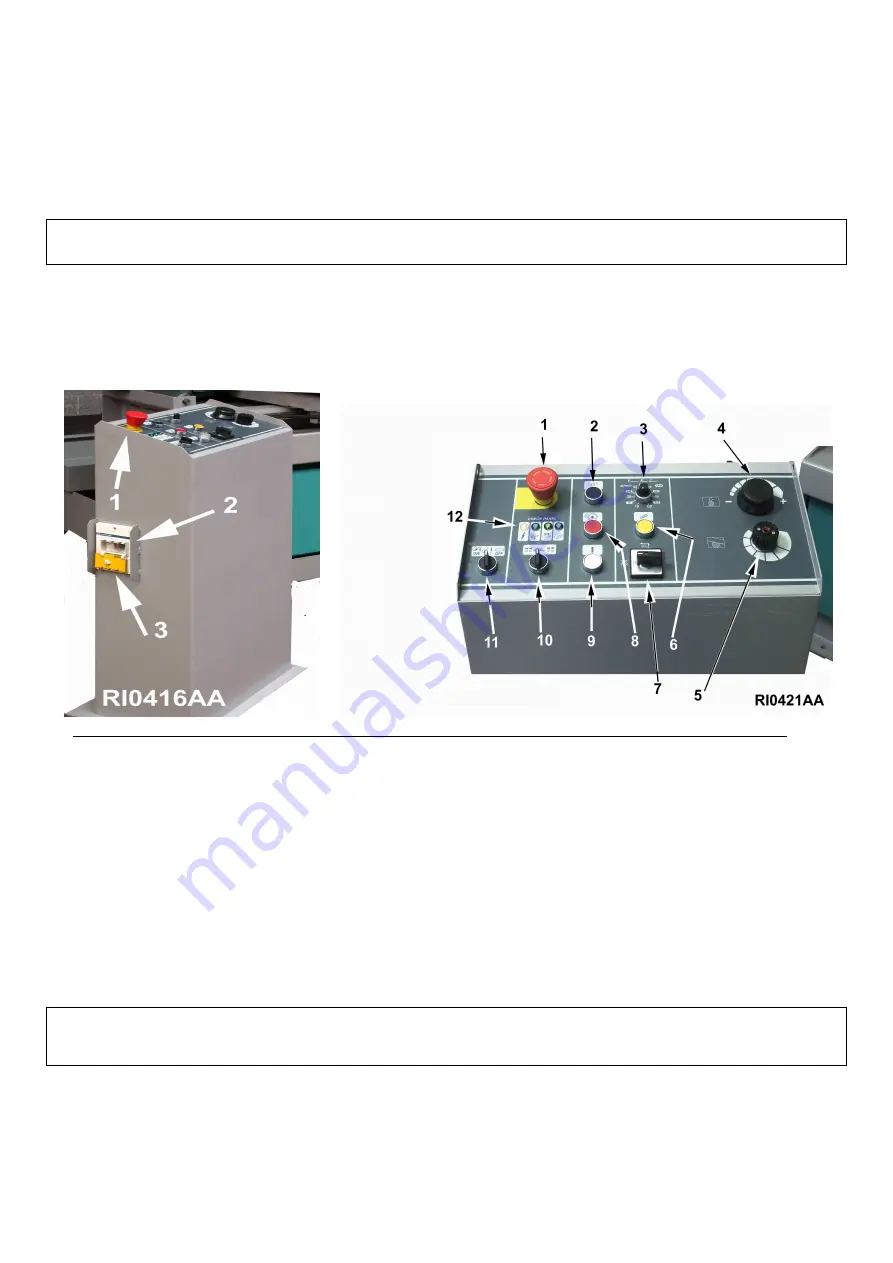
TRADUCTION OF THE ORIGINAL USER’S INSTRUCTIONS
KS450FTeng ED.2011 rev.34
19
13.2 -- ELECTRICAL CONNECTION
Verify that voltage and power frequency are compatible with the range reported on the identification plate. Variations
of more than 10% cause working anomalies, which can be either significant or not.
The power cable is complete with a pin that complies with CEE Norms. If it is not of the same type used in
your premises, it will have to be replaced (this should be done by skilled personnel, for example an
electrician).
The phasing performed by the manufacturer allows to get a correct rotation of all motors by connecting the
wires in the following order: L1=R, L2=S, L3=T,
The control box of the picture below is the “stand alone” model , to be placed at floor . The “built-in machine” model
has the same controls and functining .
Verify the correct working as follows (the blade protection structure must be closed):
a) if the EMERGENCY BUTTON – picture RI0416, No. 1 - is pushed, turn it 1/4 of a round in the direction shown on
the button.
b) push the button ON of the main switch – picture RI0416, No. 2 , the WHITE lamp must turn on.
.
c) push the yellow button RESET – picture RI0421, No. 6 - for 6/10 seconds to start the hydraulic unit motor (all the
GREEN lamps can turn on as well) and check the sawframe motions:
BLACK button (picture RI0421, No. 2): the sawframe drops (you can change the down-feed speed by means of the
speed selector – picture RI0421, No. 5).
RED button (picture RI0421, No. 8): the sawframe stops and lifts if you continue pushing.
If this does not happen, turn off the machine by means of the main switch, disconnect the feeding plug in and
reverse the connection of two of the wires inside the pin, with exclusion of the green or yellow earthing cable.
Start again from point a)
d) switch –off the saw by pushing the button OFF on the main switch (picture RI0416, No. 2). You can place as much
as 3 locks – picture RI0416, No. 3 – on this switch to prevent unauthorized access to the equipment
If no button is pushed for 10/15 minutes, the electronic panel disable the hydraulic unit motor.
To start it again, push the yellow button – picture RI0421, No. 6.
In case an external tension transformer is supplied, put it in a safe place away from the
loading/unloading area.
14 - BLADE TENSION
This machine is supplied with a blade which is already tensioned, so as to allow the motor to start (as a
matter of fact, it doesn’t work if the blade doesn’t have the right tension).
Before starting, we suggest you to verify what follows:
Summary of Contents for KS 450 FT
Page 33: ...TRADUCTION OF THE ORIGINAL USER S INSTRUCTIONS KS450FTeng ED 2011 rev 34 33 ...
Page 34: ...TRADUCTION OF THE ORIGINAL USER S INSTRUCTIONS KS450FTeng ED 2011 rev 34 34 ...
Page 35: ...TRADUCTION OF THE ORIGINAL USER S INSTRUCTIONS KS450FTeng ED 2011 rev 34 35 ...
Page 36: ...TRADUCTION OF THE ORIGINAL USER S INSTRUCTIONS KS450FTeng ED 2011 rev 34 36 ...
Page 37: ...TRADUCTION OF THE ORIGINAL USER S INSTRUCTIONS KS450FTeng ED 2011 rev 34 37 ...
Page 38: ...TRADUCTION OF THE ORIGINAL USER S INSTRUCTIONS KS450FTeng ED 2011 rev 34 38 CLOSED ...
Page 39: ...TRADUCTION OF THE ORIGINAL USER S INSTRUCTIONS KS450FTeng ED 2011 rev 34 39 ...
Page 40: ...TRADUCTION OF THE ORIGINAL USER S INSTRUCTIONS KS450FTeng ED 2011 rev 34 40 ...
Page 41: ...TRADUCTION OF THE ORIGINAL USER S INSTRUCTIONS KS450FTeng ED 2011 rev 34 41 ...
Page 42: ...TRADUCTION OF THE ORIGINAL USER S INSTRUCTIONS KS450FTeng ED 2011 rev 34 42 ...
Page 43: ...TRADUCTION OF THE ORIGINAL USER S INSTRUCTIONS KS450FTeng ED 2011 rev 34 43 ...
Page 44: ...TRADUCTION OF THE ORIGINAL USER S INSTRUCTIONS KS450FTeng ED 2011 rev 34 44 ...
Page 45: ...TRADUCTION OF THE ORIGINAL USER S INSTRUCTIONS KS450FTeng ED 2011 rev 34 45 ...
Page 46: ...TRADUCTION OF THE ORIGINAL USER S INSTRUCTIONS KS450FTeng ED 2011 rev 34 46 ...
Page 47: ...TRADUCTION OF THE ORIGINAL USER S INSTRUCTIONS KS450FTeng ED 2011 rev 34 47 ...
Page 48: ...TRADUCTION OF THE ORIGINAL USER S INSTRUCTIONS KS450FTeng ED 2011 rev 34 48 ...
Page 49: ...TRADUCTION OF THE ORIGINAL USER S INSTRUCTIONS KS450FTeng ED 2011 rev 34 49 ...
Page 50: ...TRADUCTION OF THE ORIGINAL USER S INSTRUCTIONS KS450FTeng ED 2011 rev 34 50 ...
Page 51: ...TRADUCTION OF THE ORIGINAL USER S INSTRUCTIONS KS450FTeng ED 2011 rev 34 51 ...
Page 52: ...TRADUCTION OF THE ORIGINAL USER S INSTRUCTIONS KS450FTeng ED 2011 rev 34 52 ...
Page 53: ...TRADUCTION OF THE ORIGINAL USER S INSTRUCTIONS KS450FTeng ED 2011 rev 34 53 ...