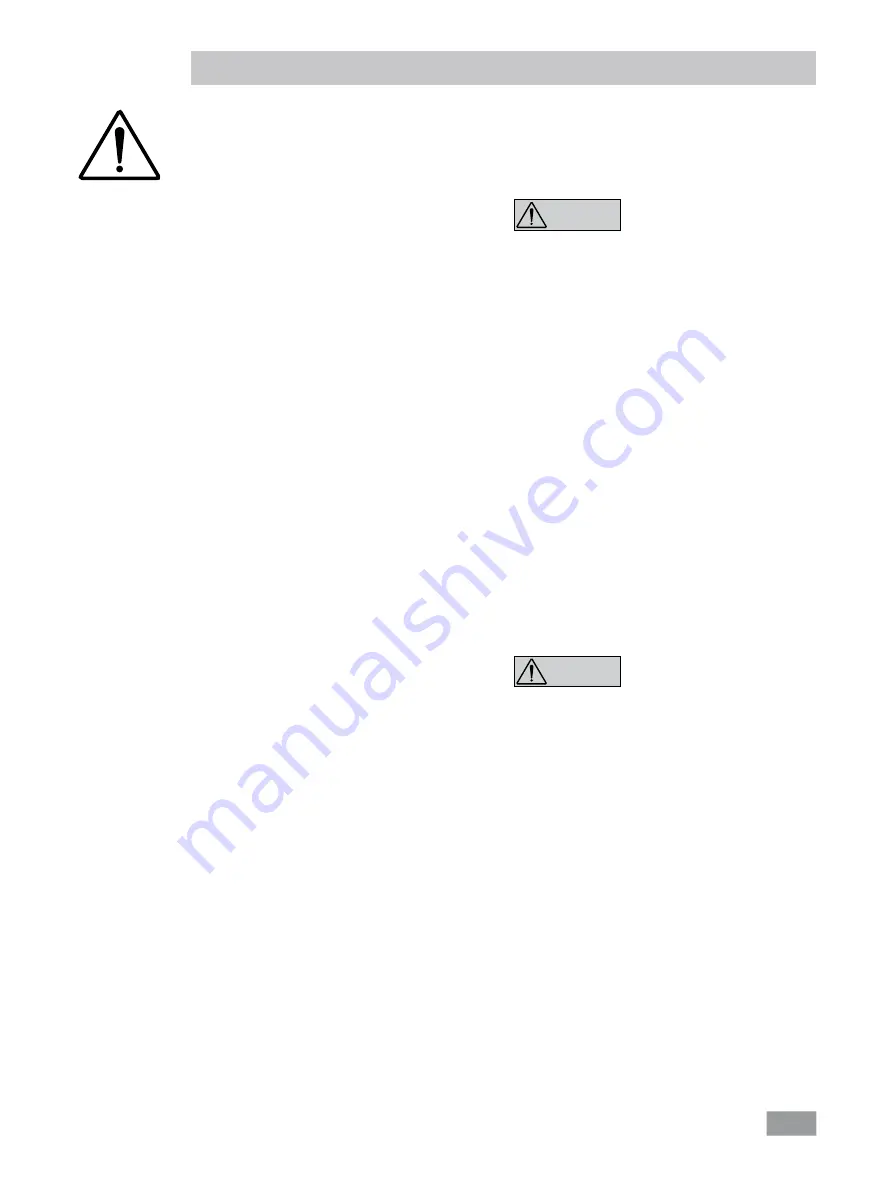
5
Safety instructions
Read the operating instructions in full before
starting up and follow the safety instruc-
tions.
Keep the operating instructions in a place where
they can be accessed by everyone.
Ensure that only trained staff work with the device.
Follow the safety instructions, guidelines, occupa-
tional health and safety and accident prevention
regulations.
The
IKA
®
C 6000 global standards/isoperibol calo-
rimeter system may be used only in conjunction
with the decomposition vessels C 6010 or C 6012
for determination of the calorific values of solid
and liquid substances to national and international
standards (such as DIN 51900, BS 1016 T5, ISO
1928, ASTM 5468, ASTM 5865 and ASTM 4809).
The maximum extra energy added to the decom-
position vessel must not exceed
40,000
J (select
the test mass accordingly). The permitted operat-
ing pressure of
230 bar
(23 MPa)
must not be
exceeded. The maximum permitted operating tem-
perature must not exceed
50 °C
.
When burning substances containing metals, en-
sure that the maximum energy input is not ex-
ceeded!
Only fill the decomposition vessel with oxygen to a
maximum pressure of
40 bar (4 MPa)
. Check the
pressure setting on the pressure reducer for your
oxygen supply. Perform a leakage test before each
combustion process (see section „Leaktightness
testing“).
Some materials tend to explode when combusted
(e.g. due to formation of peroxides), which could
cause the decomposition vessel to crack.
The IKA
®
C 6000 global standards/isoperibol calorim-
eter may not be used for testing explosive
samples
.
If the burning behaviour of a material is unknown,
it must be tested before combustion in the decom-
position vessel (risk of explosion). If you are burn-
ing
unknown samples
, leave the room or
keep
your distance
from the calorimeter.
Benzoic acid may only be combusted in its pressed
form! Flammable dust and powder must be first
pressed. Oven-dry dust and powder such as splints,
hay, straw etc. explode when combusted! Always
wet these materials first! Highly flammable liquids
with a low vapour pressure (e.g. tetramethyl dihy-
drogen disiloxane) must not directly touch the cot-
ton thread!
Furthermore, toxic combustion residue in the form
of gases, ashes or condensation, for example, is
possible in the inner wall of the decomposition
vessel.
Observe the accident prevention
requirements applicable to the
activity and the work station.
Wear your personal protective equipment.
When handling combustion samples, combustion
residue and auxiliary materials, please observe
the relevant safety regulations. The following
materials, for example, could pose a risk:
- corrosive
- highly flammable
- explosive
- bacteriologically contaminated
- toxic
Please observe the relevant regulations when
handling
oxygen
.
Warning: oxygen as a compressed gas is oxidising;
intensively aids combustion; can react violently
with flammable materials.
Do not use oil or grease!
Tubes and screwed joints for oxygen must be kept
free of grease.
Combustion gases are
hazardous to health,
therefore the venting
hose must be connected to a suitable gas
cleaning system or extraction system.
At the end of the work period, close the main
valve for the oxygen supply.
Perform servicing work only when the equipment
is depressurised.
When using
stainless steel crucibles
thoroughly
check their condition after each experiment. If the
material gets thinner, the crucible may catch fire
and damage the decomposition vessel. Crucibles
must not be used for more than 25 combustions
for safety reasons.
DANGER
DANGER
Summary of Contents for C 6000 global standards
Page 2: ......
Page 43: ...43 Sound Activation of the speakers...
Page 61: ......
Page 62: ......
Page 63: ......