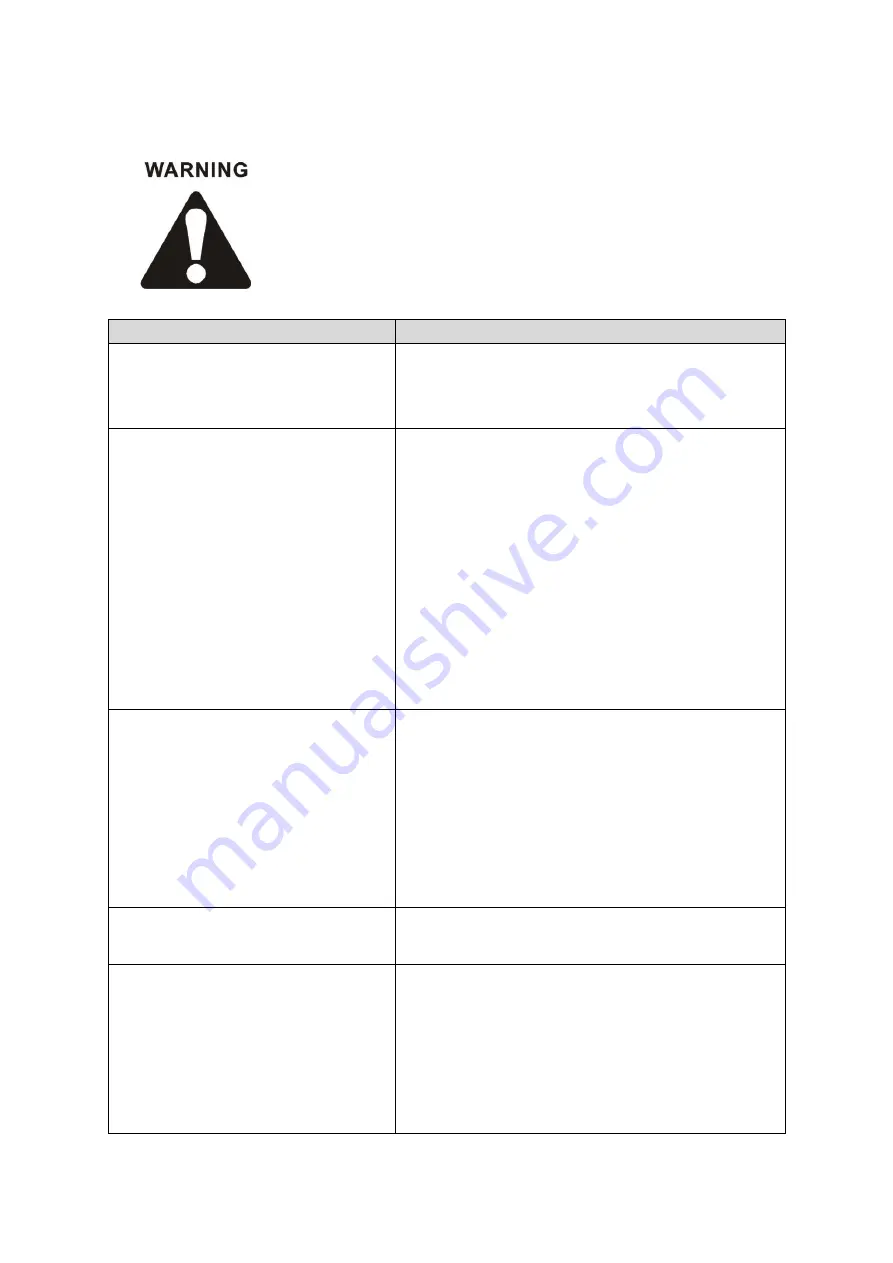
17
The following operation requires sufficient professional
knowledge on electric aspect and comprehensive safety
knowledge. Operators should be holders of valid qualification
certificates which can prove their skills and knowledge. Make
sure the input cable of the machine is cut off from the electricity
utility before uncovering the welding machine.
(1)
Check
periodically
whether
inner
circuit
connection is ok (esp. plugs). Tighten the loose connection. If
there is oxidization, remove it with sandpaper and then
reconnect.
(2) Keep hands, hair and tools away from the moving
parts such as the fan to avoid personal injury or machine
damage.
(3) Clean the dust periodically with dry and clean
compressed air. If welding in environment with heavy smoke
and pollution, the machine should be cleaned daily. The
pressure of compressed air should be at a proper lever lest the
small parts inside the machine be damaged.
(4) Avoid rain, water and vapor infilter the machine. If
there is, dry it and check the insulation with a megger (including
that between the connections and that between the connection
and the case). Only when there is no abnormal phenomena can
welding be continued.
(5) Check periodically whether the insulation skin of all
cables are perfect. If there is any dilapidation, wrap it or replace
it.
(6) Put the machine into the original packing in dry
location if it is not to be used for a long time.
10. TROUBLESHOOTING
PROBLEM
CAUSE
The LCD can’t light up, no wire feeding
during welding, and fan is not working.
•
Check if the power switch is on.
•
Check if the connected power supply is working.
•
Check if the power supply cable is broken.
The LCD is on, fan is working; No wire
feeding during welding.
•
Check if the internal wires are well connected.
•
Check if any disconnection at the output terminals.
•
Check if the control wire or switch on the torch is
broken.
•
Check if the control circuit is broken.
•
Check if the welding cable is well connected to the
machine.
•
Check if the torch type selector is at the right
position for the torch in use.
•
If the over-heat light is on, please wait to recover.
The machine output is ok, gas comes
out, but the wire is not feeding
•
Check the wire feeding is working or not; if it’s
working, please make sure the wire roller is correct
according to the welding wire.
•
Check if the wire tube or nozzle is stuck.
•
Make sure the electrode is the right size.
•
Check if the torch type selector is at the right
position for the torch in use.
The wire feeding is ok, and welding is
ok, but the gas outlet is abnormal.
•
Please check the gas regulator or gas hose.
•
Check if the torch is stuck, or any gas leakage.
Welding arc is not stable.
•
Please check if the input voltage is correct.
•
Please check if the polarity cable connection is
correct.
•
Please change the torch head consumables if
they are not in good condition.
•
Check if the gas pressure is correct.
Summary of Contents for MIG-200M
Page 5: ...4 2 1 Flow Diagram 2 2 Schematic Diagram...
Page 20: ...19 11 DIAGRAM...