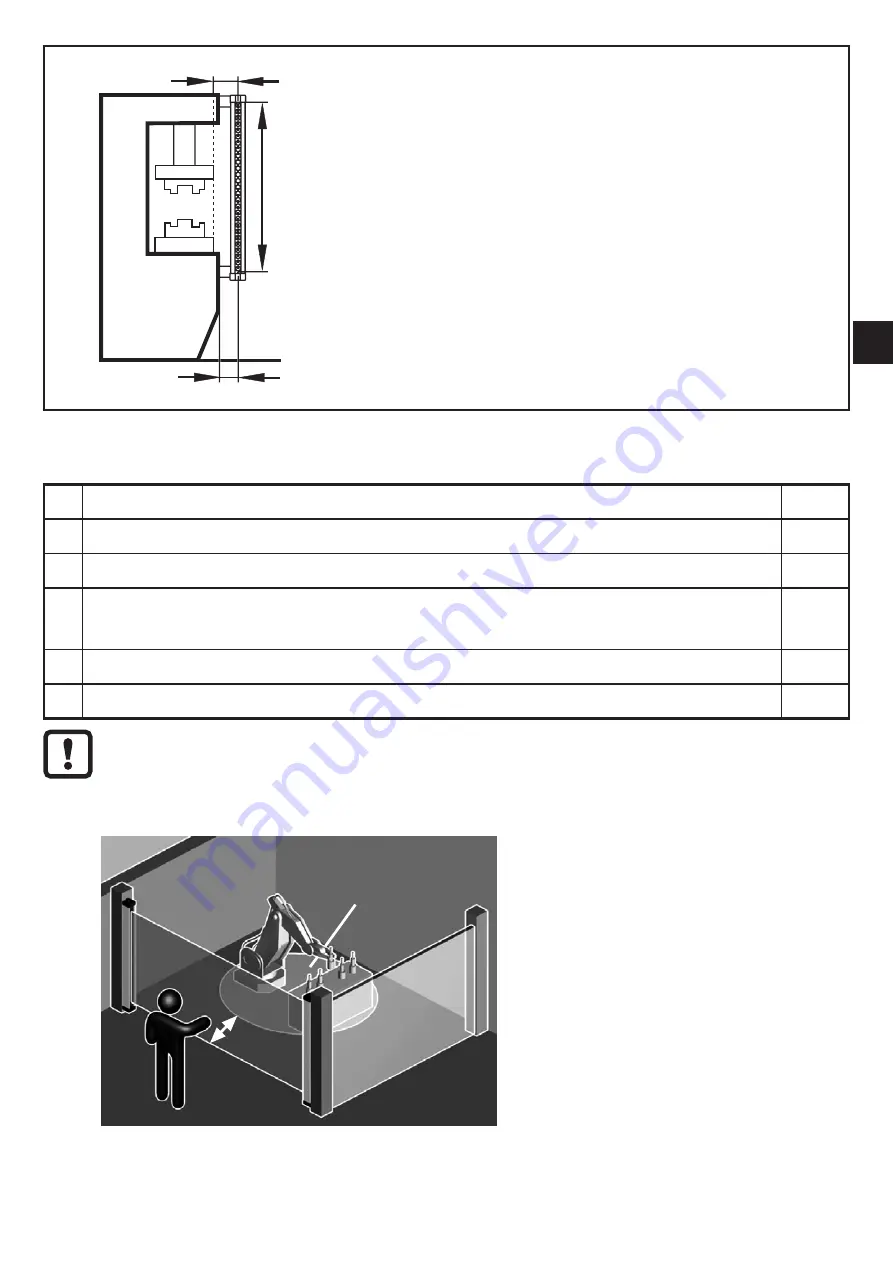
11
UK
►
Install the photoelectric safety sensor at a distance
that is greater or equal to the minimum safety
distance (S) so that the hazardous area (A) can
only be accessed after complete standstill of the
hazardous machine motion.
According to the European Standard ISO 13855 the
following formula is to be used to calculate the minimum
safety distance (S):
S = K (t1 + t2) + C
C = 8 (d - 14)
A = hazardous area
H = protected area height
S = min. safety distance
C = additional distance
S
Minimum safety distance
mm
K
Speed of approach of the object towards the hazardous area
mm/s
t
1
Total response time of the protective equipment, from release to switching off s
t
2
Total response time of the machine, from the stop signal to switching off or to
passing into the state defined as safe
s
C
Additional distance
mm
d
Resolution (detection capability)
mm
Non-compliance with the minimum safety distance may lead to restrictions
to or loss of the safety function.
Application example:
A = hazardous area
S = min. safety distance