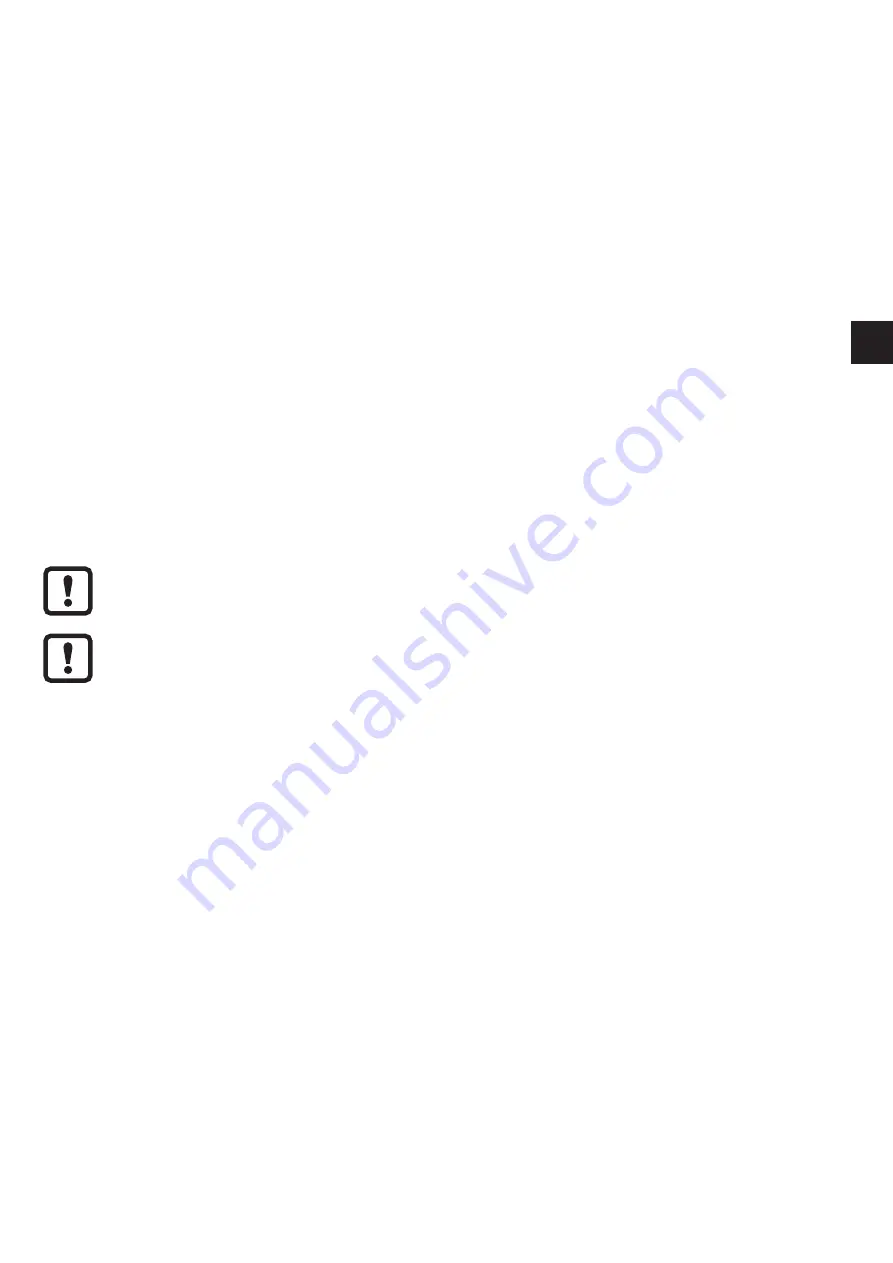
5
UK
• Installation, electrical connection, set-up, operation and maintenance of the
product must be carried out by qualified personnel authorised by the machine
operator�
• Protect units and cables against damage�
• The unit complies with the standards EN 61000-6-4 and EN 61000-6-2� The
unit may cause radio interference in domestic areas� If interference occurs, the
user must take appropriate actions�
3 Functions and features
3.1 Application area
The unit detects without contact metals, almost all plastics, glass, ceramics, wood,
paper, oils, greases, water and all hydrous materials and indicates their presence
by providing a switching signal or a continuous process value from 0���100 %�
The sensor detects the medium through the tank wall� The wall is suppressed by
means of an adjustment function, so that only the medium is detected�
The tank wall must be made of a non-metal material�
Incorrect installation or adjustment may lead to wrong process values being
provided�
►
�
►
Check proper function by an application test�
3.2 Restriction of the application area
• Using the unit in direct contact with the medium, with ionising radiation or in
environments with direct condensation is not allowed�
• This is a class A product� This product may cause radio interference in
domestic areas�
►
If required, take appropriate EMC screening measures
.
•
In case of highly adhesive media (e.g. glue, shampoo), there may be film
formation�
• Highly conductive films or foams may be detected as level�