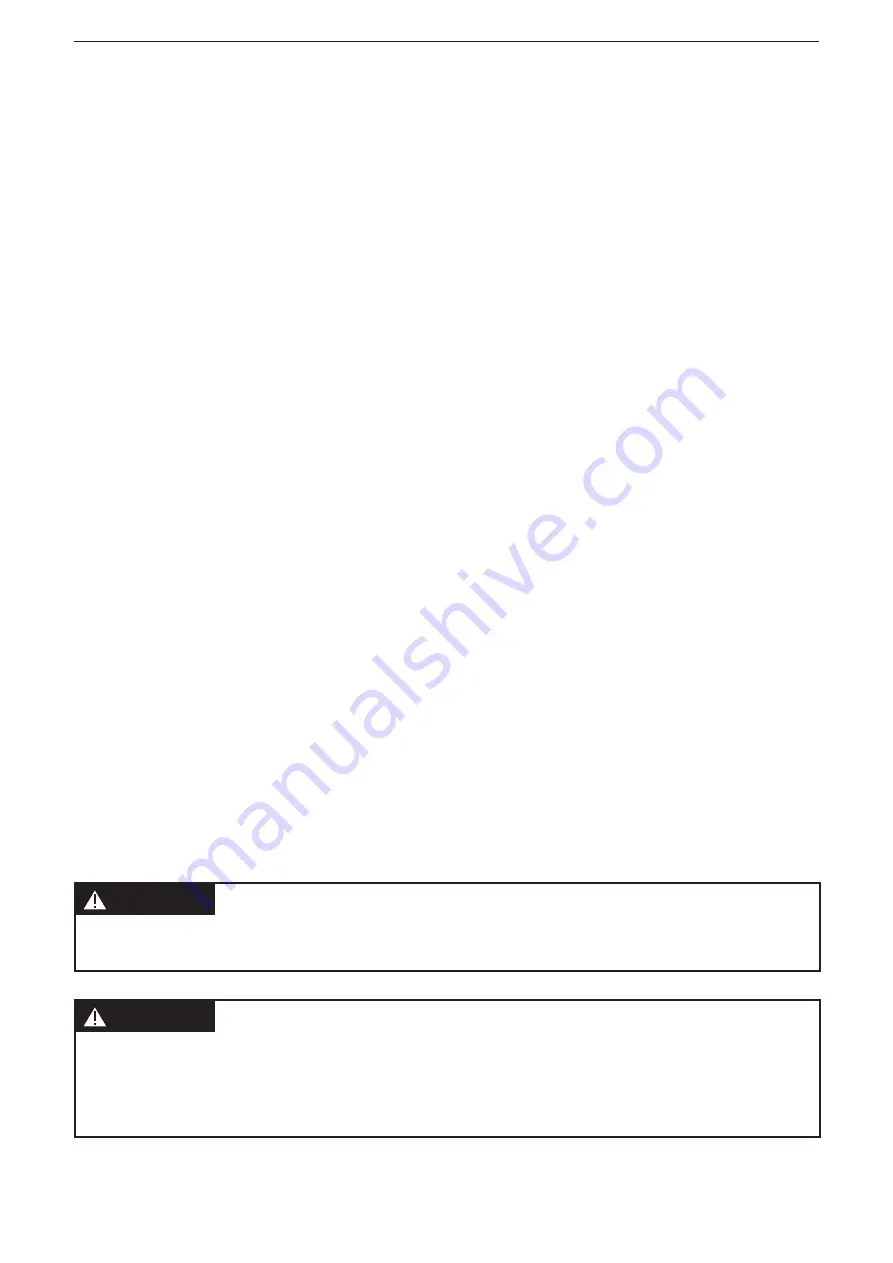
ClassicController CR0053
6
2.5 Tampering with the device
In case of malfunctions or uncertainties please contact the manufacturer� Any
tampering with the device can seriously affect the safety of operators and
machinery� This is not permitted and leads to the exclusion of any liability and
warranty claims�
2.6 Electromagnetic compatibility
This is a class A product� It can cause radio interference in domestic areas� In this
case the operator is requested to take appropriate measures�
2.7 Electrical welding on vehicles and plants
Welding work on the chassis frame must only be carried out by qualified persons�
Remove and cover the plus and minus terminals of the batteries�
Disconnect all contacts of the controller from the on-board system prior to welding
on the vehicle or plant� Connect the earth terminal of the welding device directly to
the part to be welded�
Do not touch the controller or electric cables with the welding electrode or the
earth terminal of the welding device�
Protect the controller against weld slag�
3 Functions and features
The freely programmable controllers of the "ClassicController" series are rated for
use under difficult conditions (e�g� extended temperature range, strong vibration,
intensive EMC interference)�
They are suited for direct installation in machines in mobile and robust
applications� Integrated hardware and software functions (operating system) offer
high protection for the machine�
The controllers can be used as CANopen master�
WARNING
The "ClassicController" series is not approved for safety tasks in the field of
safety of persons�
WARNING
The user is responsible for the safe function of the application programs
which he created himself� If necessary, he must additionally carry out an approval
test by corresponding supervisory and test organisations according to the
national regulations�