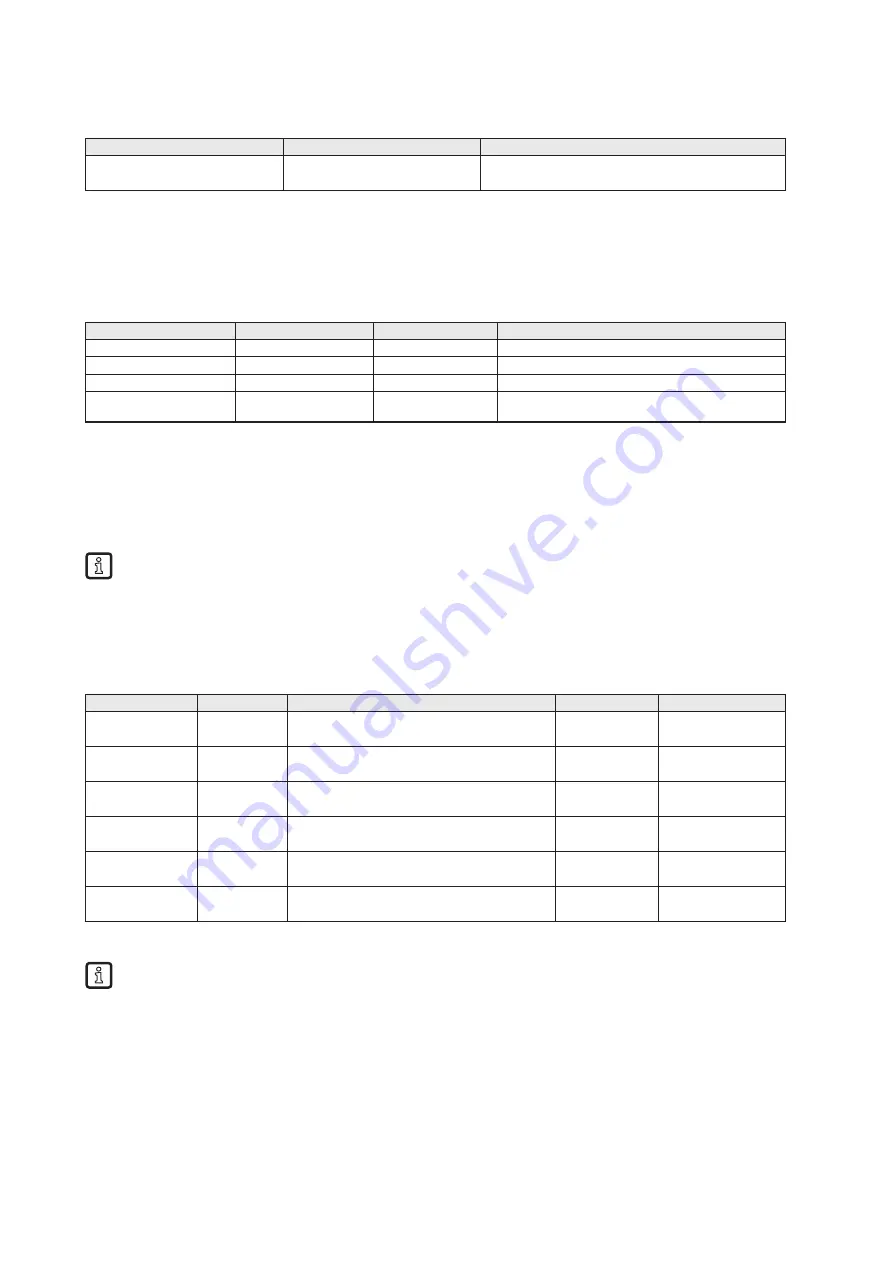
30
9.8 Number of the CIP connections
Connection type
Number
Access
IO-Messaging
3
1 * Exclusive Owner (Multicast)
2 * Listen Only
Table 5: Number of CIP connections
9.9 RUN/IDLE flag functionality
When establishing the connection between the EtherNet/IP scanner and the evaluation unit the 32 Bit
realtime header is exchanged via the EtherNet/IP connection manager . Within the header the RUN/IDLE
flag is transmitted which allows to control the functions of the evaluation unit .
EtherNet/IP Connection
Run/Idle flag
Parameter failsafe
Function
Active
Off
Not relevant
Channel IO-1 … IO-4 deactivated
Active
On
Off
Channel IO-1 … IO-4 activated
Active
On
On
Channel IO-1 … IO-4 activated
Switch from
active to inactive
Off
On
Channel IO-1 … IO-4 remain activated, the outputs
keep the last received state .
Table 6: Assembly 100 (Output image of the PLC)
9.10 Setting the Requested Packet Interval (RPI)
It is recommended to set the RPI within the PLC to half of the desired update time of the evaluation unit .
Example: Requesting the transponder UID every 60 ms => RPI = 30 ms
The outputs / RFID communication of the evaluation unit have a data update rate of 12 ms,
therefore the shortest sensible RP interval is 6 ms .
9.11 Configuration assembly 102 structure
The assembly 102 is used to transfer the configuration- and parameter data of the evaluation unit . The
length of the configuration data is fixed to 64 bytes (32 words), only the first 40 bytes are used . Each
channel requires 8 bytes (4 words) .
Assembly
Byte
Content
Dataflow
Access
102d
00…07
Channel IO-1
Konfiguration/Parameter
O->T
T->O
Read/Write
Read
08…15
Channel IO-2
Konfiguration/Parameter
O->T
T->O
Read/Write
Read
16…23
Channel IO-3
Konfiguration/Parameter
O->T
T->O
Read/Write
Read
24…31
Channel IO-4
Konfiguration/Parameter
O->T
T->O
Read/Write
Read
32…39
Parameter evaluation unit
O->T
T->O
Read/Write
Read
40…63
not used
O->T
T->O
Read/Write
Read
Table 9: Assembly 102 (PLC configuration output)
On PLCs manufactured by Schneider Electric it is possible to create the configuration assembly via
the ESD file .
On PLCs manufactured by Rockwell this is only possible if the version of the programming
software RSLOGIX is > 19 .
If the PLC does not support configuration via an EDS file, the user is required to program the PLC
(→ 9.11.1 Coding of the channel configuration)
(→ 9.12 Examples of configuration data for the configuration assembly 102)