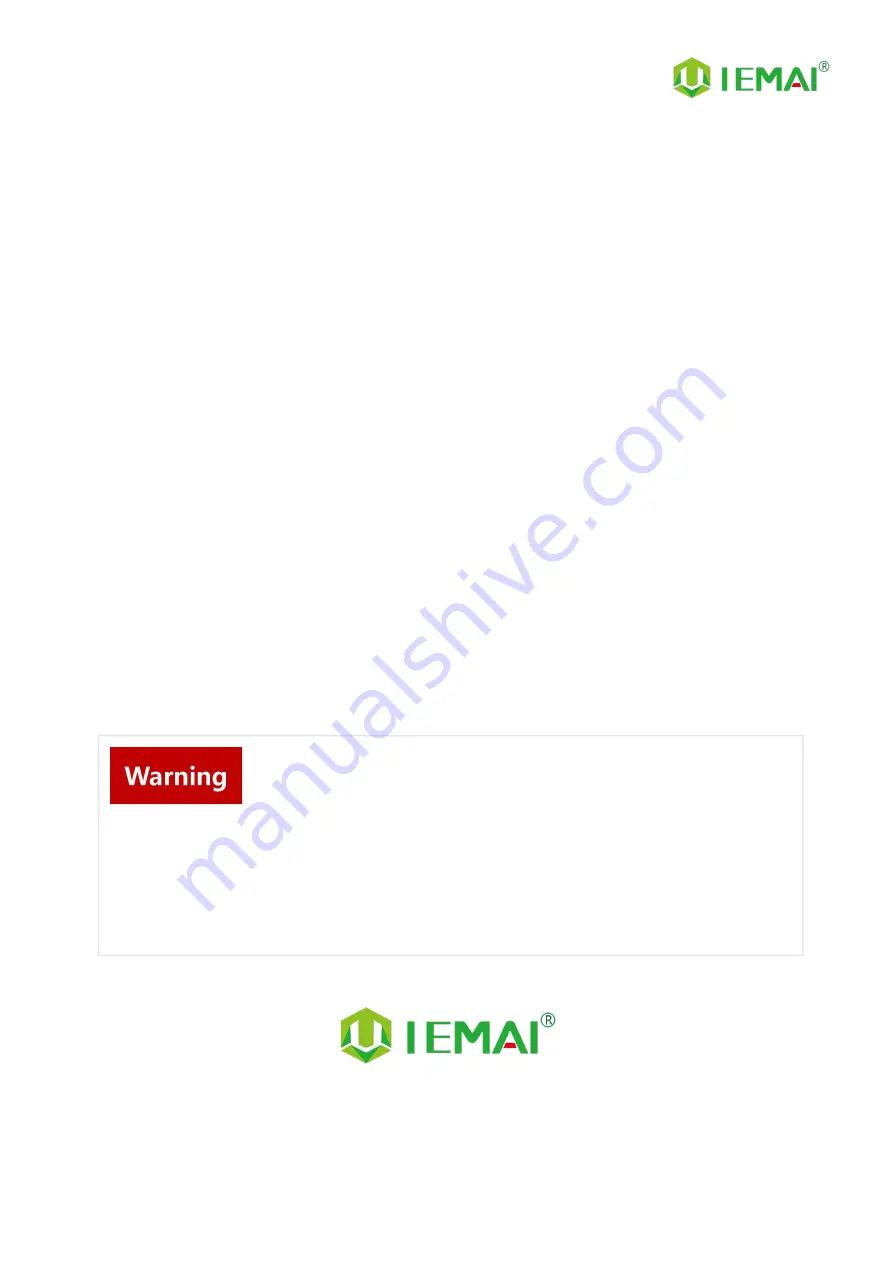
Print More Materials, All For Application
Large Scale
3D Printer
YM-NT-1000
Operating Instructions
* Please read this manual carefully before starting to operate.
This device is a Class A product. Use in a general indoor environment may
cause radio interference and therefore requires the user to take appropriate
protective measures.