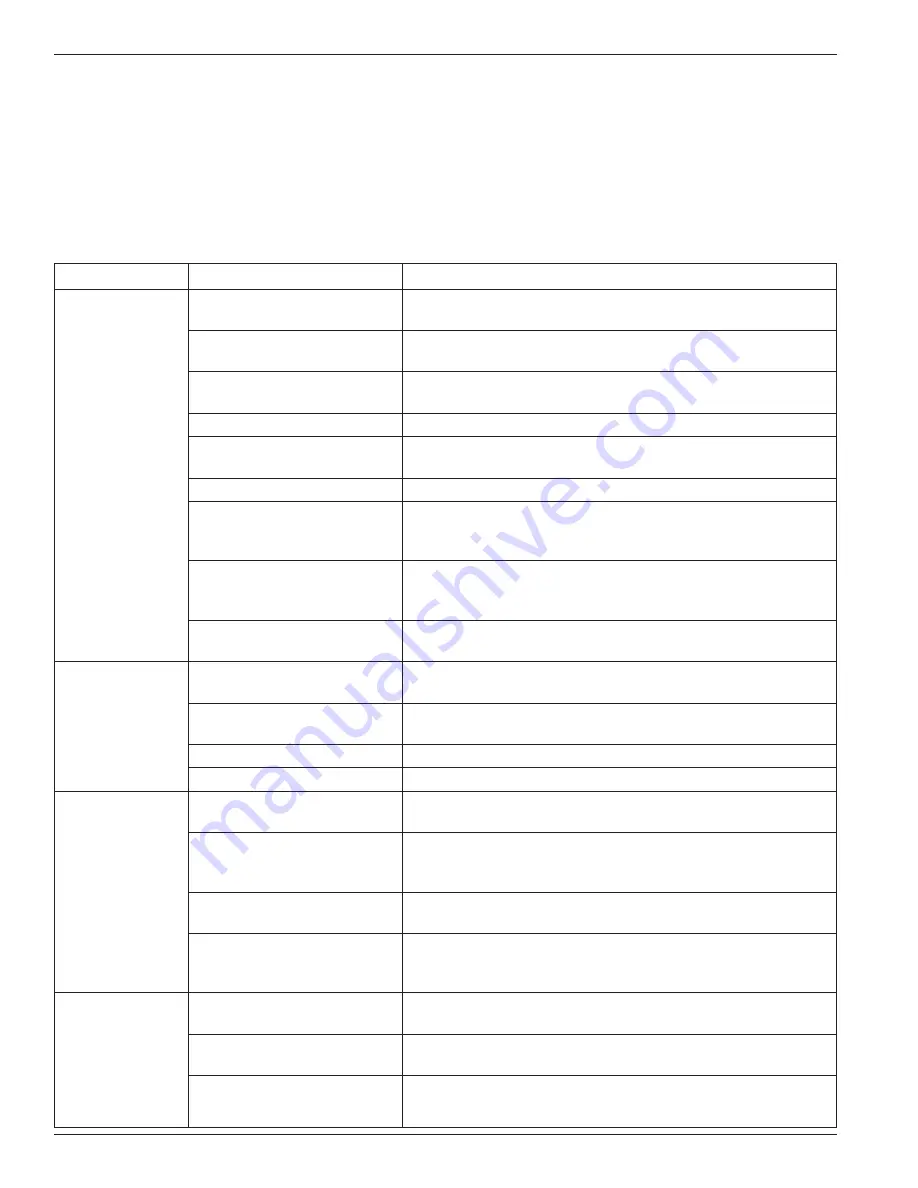
28
Appendix F—Troubleshooting Guide
In diagnosing pump and system troubles, record the
following data during product transfers:
1. Pressure at pump suction.
2. Pressure at pump discharge.
3. Pressure in truck tank.
4. Pressure in tank being filled.
5. Pipe size and length of suction and discharge lines.
6. Size and length of vapor equalizing line.
7. Pump speed if practical.
Problem
Cause
Solution
Low capacity
Pump speed too slow
Check engine speed and PTO ratio. Consult pump performance
curve. Use tachometer on pump if speed is questionable.
High differential pressure
Restriction in discharge piping or hose too small. Vapor
equalization lines too small or not used.
External bypass valve
Readjust, repair, or replace valve.
stuck open or set too low
Clogged strainer
Clean strainer.
Suction pipe too small
Indicated by pump inlet pressure dropping several pounds when
or restricted
pump is started. Remove restriction or modify piping.
Worn vanes
Replace.
Pump without vapor return
Without vapor equalization, a pump can remove only about 3%
of the truck tank capacity per minute without severe cavitation
and capacity loss.
Worn sideplates
Reverse or replace sideplates. Check universal drive assembly
to make sure angularity is within limits, yokes are parallel and
slip-joint is greased. Check bearings.
Vanes sticking
Remove vanes and clean out foreign matter (check
strainer). Replace vanes if swollen.
Pump runs
Valve closed
Check valves. Make sure internal tank excess flow valve is
but no flow
open! Refer to manufacturer’s instructions.
Excess flow valve slugged
Stop pump until valve opens. If problem continues, slow pump
down or install a new or larger excess flow valve.
Broken shaft
Disassemble and inspect pump. Repair if necessary.
Defective meter
Service meter.
Pump will not
Foreign matter in pump
Clean out the pump—check strainer in suction line.
turn–locked up
Vanes broken
Clean out pump carefully and replace vanes. Has
pump been operated dry? Then, check for damage to cam and
rotor shaft assembly.
Bearing seized
Replace pump bearings. Grease monthly. Use ball bearing
grease manufactured for intended service.
Moisture frozen in pump
Let thaw and break loose carefully. Add alcohol to tank (on LP-
Gas). Check with product supplier about possibility of water
in gas.
Will not build
pressure
Poor suction conditions
Clean inlet strainer. Increase pipe size.
External bypass valve
Set valve for higher pressure—see instructions.
set too low
Worn vanes
Disassemble, inspect and repair as necessary. Do not run
and/or sideplates
pump dry!
Summary of Contents for Corken Z-Series
Page 31: ......