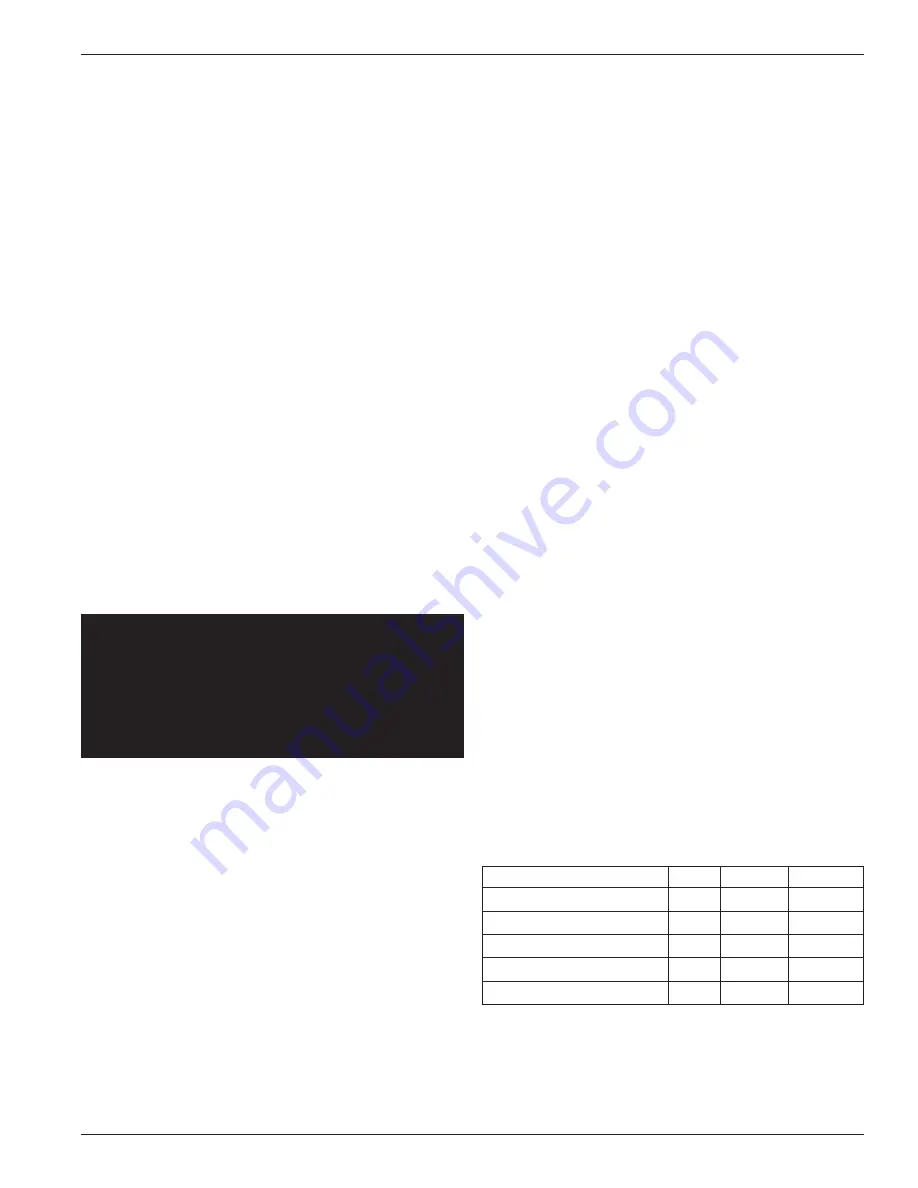
7
Make sure the transfer hoses are not "kinked'' which can
cause excessive pump discharge pressure. Always make
sure your hoses are not out of date.
There are two lubrication points in which to grease the pump
bearings; one zerk per bearing cap located at opposite ends
of the pump. Four grease relief and seal ventilation fittings
have been provided, two at each end of the pump, to prevent
overgreasing the bearings. Overgreasing can cause seal
failure if grease passageways are blocked in some way.
Clean each fitting before lubricating the bearings. This
practice helps to prevent foreign material contamination of
the bearings and accidental over-pressurization of the
mechanical seals. Use only ball bearing grease (MIL-G-
10924C) with a temperature rating of -70°F.
Normal wear parts are the mechanical shaft seals, bearings,
vanes and sideplates. All of these parts plus O-rings and
grease seals are offered in the Corken "repair kit" listed in
this manual directly after the Seal Replacement Instruction
on page 9. Use only genuine Corken replacement parts
when repairing your Corken Z-Series pump. Follow the
instructions provided with the parts.
When it becomes necessary to repair your pump or remove
it from the system, you must be absolutely certain that all
propane, anhydrous ammonia or whatever product being
pumped is bled from the pump and connecting piping. Once
all the product has safely been bled from the pump and
connecting piping, make certain no pressure is left in the
system. SPECIAL CARE MUST BE TAKEN DURING THE
BLEED DOWN PROCESS TO AVOID DANGER TO
PERSONNEL AND PROPERTY IN THE AREA. Bleeding
a system too fast is a common mistake and may result in
"refrigerated" liquid being left in the pump and piping even
though the pressure gauge shows no pressure. As the
"refrigerated" liquid begins to warm, more gas will escape
causing a dangerous condition. Take your time in bleeding
your system and make proper provisions to vent or capture
the gas in accordance with local regulations. ONLY A
PROPERLY TRAINED INDIVIDUAL SHOULD BE
ALLOWED TO BLEED A PUMPING SYSTEM.
Pump Maintenance Schedule
Truck pumps can lower the truck tank pressure from 5
psi to 10 psi (below the starting tank pressure) if there
is no means provided for equalizing—and then the
trouble starts! As the weather gets colder, the worse
this condition will become. You can detect this ''pull
down'' in pressure by observing your truck tank pressure
gauge as the pump is operating.
To prevent this violent liquid boiling, pressure in some form
must be introduced into the truck tank. The simple way to
accomplish this is to "equalize'' between the truck tank and
the receiving tank. Equalizing takes the higher pressure
vapors from the receiving tank and returns them to the truck
tank. As a result, the void left by the receding liquid is filled.
This in turn lessens the need for the liquid to boil excessively.
The equalizing principle is necessary for volatile liquids.
NOTE: EQUALIZING BETWEEN TANKS OR THE
ADDITION OF PRESSURE IS NOT A LEGAL
TRANSFER IN MOST STATES. IF EQUALIZING LINES
ARE NOT PERMITTED REMEMBER THAT A QUIET
PUMP IS AN EFFICIENT PUMP. A NOISY PUMP IS NOT
EFFICIENT AND THE CONDITIONS THAT CAUSE THE
NOISE ALSO CAUSE WEAR TO INTERNAL PARTS.
OPERATE THE PUMP AT SPEEDS THAT RESULT IN
A ''QUIET" TRANSFER.
Maintenance of Your Z-Series
Coro-Vane
®
Truck Pump System
Your Corken Z-Series Pump requires regular maintenance
and care like all mechanical equipment. A neglected or
improperly repaired pump will result in premature failure
and cause unsafe conditions. To promote product longevity
and safety, maintenance must be performed by properly
trained technicians. Make sure all safety systems are in
place and the system pressure has been relieved before
attempting ANY maintenance.
All repairs to the pump must be performed by
qualified personnel in a safe manner, utilizing tools
and/or equipment that are free of hazards, and
follows the applicable safety codes of practice set
by the local authorities having jurisdiction. Make
sure the system pressure has been relieved before
attempting any repair to the pump.
Daily
Monthly 3 Months
Lubricate bearings
X
Inspect drive coupling
X
Clean inlet strainer
X
Check for leaks
X
Inspect hose and fittings
X
Figure 3
Summary of Contents for Corken Z-Series
Page 31: ......