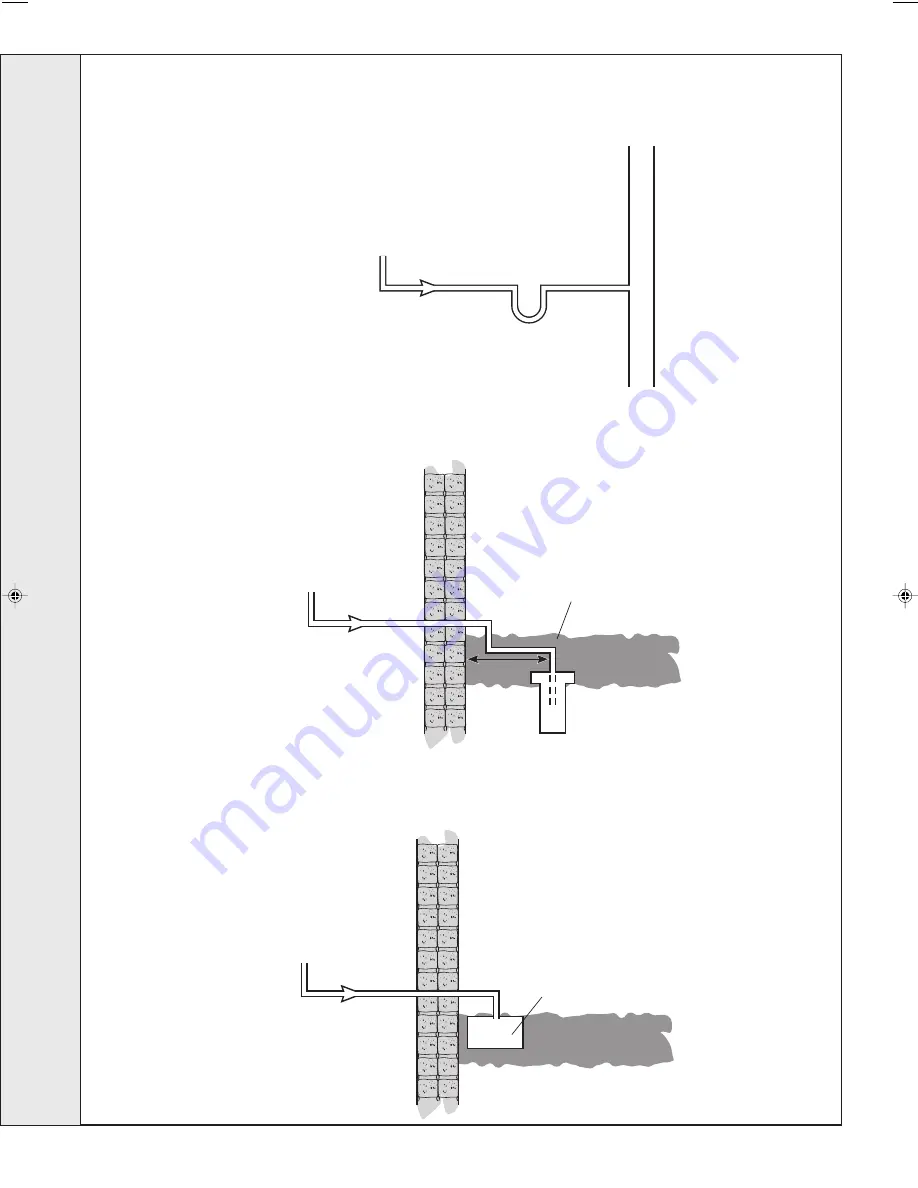
22
INSTALLATION
icos system -
Installation and Servicing
INST
ALLA
TION
24 CONDENSATE PIPE TERMINATION CONFIGURATIONS
. . . continued
BOILER
cla777
3
3. INTERNAL CONNECTION TO SOIL AND VENT STACK
* Make connection to SVP using a solvent welded saddle
BOILER
External
wall
Ground Level
Termination
to Soak away
cla7774
minimum
500
mm
BOILER
External
wall
Ground Level
Open end of pipe
direct into gulley
below grating but
above water level
DRAIN
cla777
5
4. TERMINATION TO SOAK AWAY
5. TERMINATION TO DRAIN / GULLEY
200214-11.pmd
17/11/2006, 09:35
22