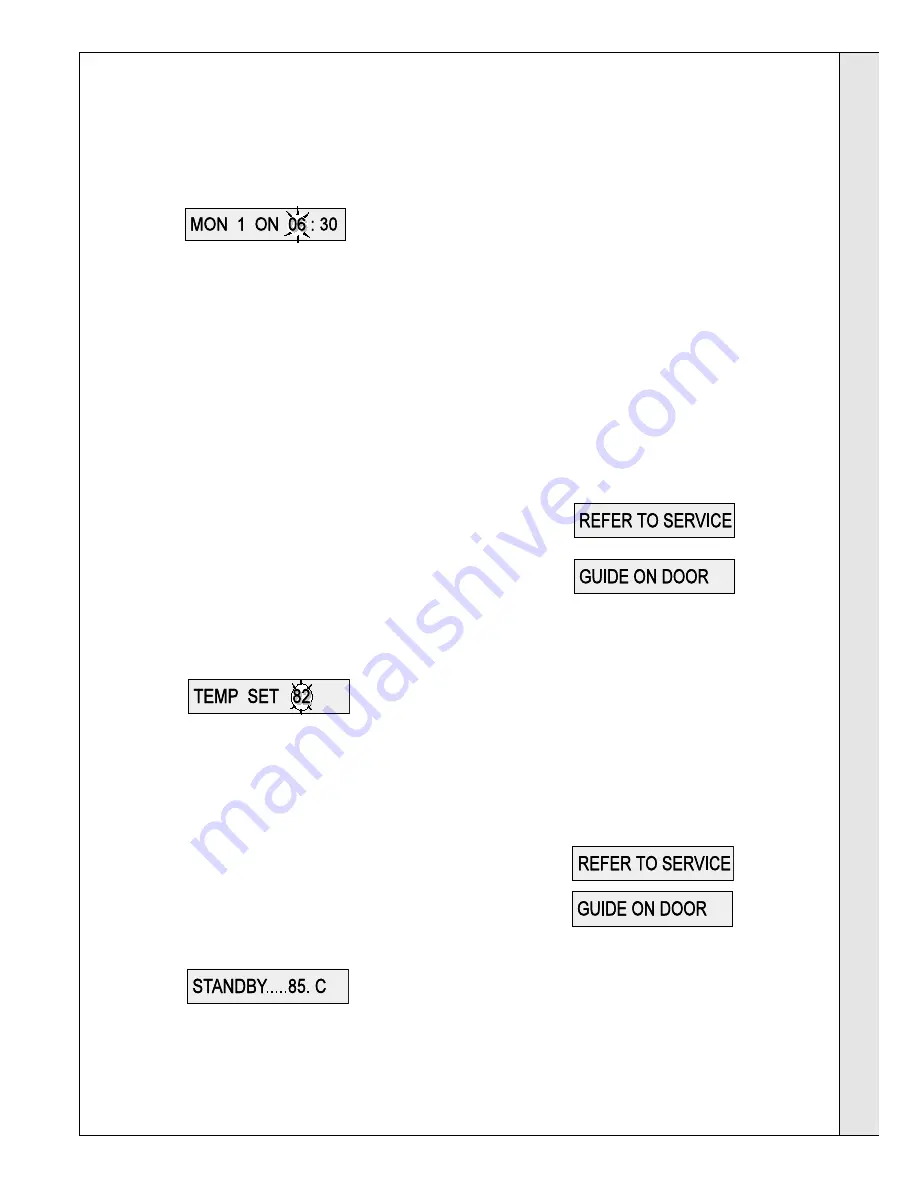
23
Concord CXSD/H -
Installation & Servicing
INSTALLATION
30 DESCRIPTION AND OPERATION OF BOILER CONTROLS - continued
Delayed High Rate Gas valve Operation
When the boiler is started from cold the high rate gas valve
will be delayed for 3 minutes and then energised. If the boiler
flow temperature is equal to or greater than 55
0
C then this
delay will NOT occur.
Notes.
1.
If a fault occurs with the boiler thermostat the fault
display screen will show "C/H Sensor Fault".
2.
When the low rate gas valve is de-energised as the
temperature required has been obtained the boiler will
go into an anti-cycle route for 2 minutes. The display will
indicate anti-cycle and the current flow temperature.
SERVICING
The SERVICE option is intended as a memory aid to the more
comprehensive servicing instructions to be found in this
manual.
Using the [UP] or [Down] button select SERVICE from the menu
and press [ENTER]. The following display will be available:-
The 2 screens will alternate to display this whole message.
When using this option, arrow keys will be in evidence to
indicate if the UP or DOWN buttons should be used.
It is
IMPORTANT that these instructions are carried out precisely
and in the order displayed.
COMMISSIONING
The "Commissioning" option is intended as a memory aid to
the more comprehensive commissioning instructions to be
found in this manual.
Using the [UP] or [Down] button select "Commissioning" from
the menu and press [ENTER]. The following display will be
available:-
The 2 screens will alternate to display this whole message.
When using this option arrow keys will be in evidence to
indicate if the [UP] or [DOWN] buttons should be used.
It is
IMPORTANT that these instructions are carried out precisely
and in the order displayed.
FAULT DIAGNOSIS
In the unlikely event of a fault condition, the microprocessors
will identify the fault area and display a message indicating the
nature of the fault, to assist a speedy and effective repair.
See "Fault Finding" section for more details.
procedure should be followed but the [NO] button pressed.
PROGRAMME HOURS
Enables a user-timed programme to be entered.
The following display will be available:-
with the hours, 06, flashing
Using the [UP] or [DOWN] button select the correct hour and
press [ENTER]. The
minutes
will now flash and the correct
minutes should be selected, using the [UP] or [DOWN] button
followed by pressing [ENTER]. This will cause the hours to
flash and if the correct ON time has been entered the [EXIT]
button should be pressed. The display will now show the OFF
for time zone one.
This procedure should be repeated for all 3 time zones for
Monday.
After the last [EXIT] the display will ask if this day's programmes
require to be copied to Tuesday. If the [YES] button is pressed
Tuesday's programme will be the same as Monday. This action
can be repeated for all the days or as many as required,
If the [NO] button is pressed then all 3 time slots will need to be
programmed with the required times.
TEMPERATURE SET POINT
Enables the temperature at which the boiler is required to
operate to be set. It has a range of 60
0
C - 85
0
C.
Using the [UP] or [Down] button select the TEMP SET from the
menu and press [ENTER]. The following will be displayed:-
with the temperature flashing
The [UP] and [Down] button should be pressed until the
correct temperature is selected then the [ENTER] button
should be pressed; the temperature selected will become
stationary. Pressing the [EXIT] button will ensure that the
control accepts the new setting and return to the menu.
High / Low Operation
In the example above, when the boiler flow temperature is
equal to 82
0
C the high rate gas valve will close, allowing the
boiler to run at low rate. When the flow temperature exceeds
the set temperature by 3
0
C, in the example above 85
0
C, the
low rate gas valve will close and the boiler will be off. The
information screen will display
The boiler will remain OFF for a minimum of 3 minutes or until
the boiler flow temperature has dropped by 3
0
C, whichever is
the greater time.
If the boiler load is such that it cycles between high and low
operation the boiler will fall through 3
0
before the high rate gas
valve is energised.
INST
ALLA
TION
Summary of Contents for Concord CXSD 40/H
Page 1: ......