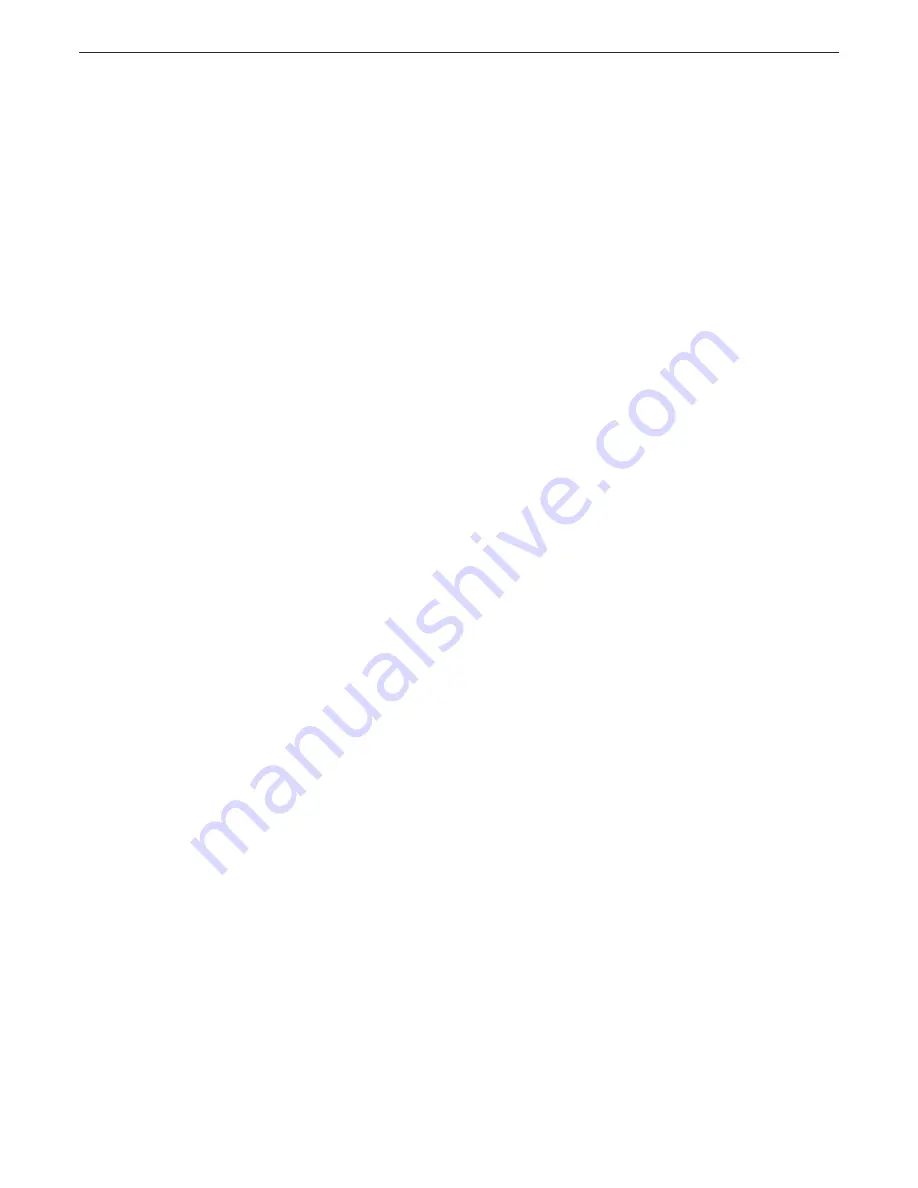
5
Buccaneer GTE -
Installation & Servicing
GENERAL
GAS SUPPLY
The local gas supplier should be consulted, at the installation
planning stage, in order to establish the availability of an
adequate supply of gas. An existing service pipe must NOT be
used without prior consultation with the local gas supplier.
A gas meter can only be connected by the local gas supplier or
by a registered CORGI engineer.
An existing meter should be checked, preferably by the gas
supplier, to ensure that the meter is adequate to deal with the
rate of gas supply required. A minimum working gas pressure
of 17.5mbar MUST be available at the boiler inlet for Natural gas
and 37mbar for Propane.
Do not use pipes of smaller size than the burner inlet gas
connection.
The complete installation MUST be tested for gas soundness
and purged in accordance with the appropriate standards listed
on page 4.
FLUE INSTALLATION
IMPORTANT
It is the responsibility of the installer to ensure, in practice, that
products of combustion discharging from the terminal cannot re-
enter the building or any other adjacent building through
ventilators, windows, doors, other sources of natural air
infiltration, or forced ventilation / air conditioning.
If this should occur the appliance MUST be turned OFF, labelled
as 'unsafe' and corrective action taken.
The flue must be installed in accordance with the appropriate
standards listed on page 4.
WATER CIRCULATION SYSTEM
The system pump MUST be connected to the boiler.
The boiler must NOT be used for direct hot water supply. The
hot water storage cylinder MUST be of the indirect type.
Single feed, indirect cylinders are not recommended and MUST
NOT be used on sealed systems.
The appliances are NOT suitable for gravity central heating nor
are they suitable for the provision of gravity domestic hot water.
The hot water cylinder and ancillary pipework, not forming part of
the useful heating surface, should be lagged to prevent heat
loss and any possible freezing - particularly where pipes run
through roof spaces and ventilated underfloor spaces.
The boiler must be vented.
Draining taps MUST be located in accessible positions, which
permit the draining of the whole system - including the boiler
and hot water storage vessel. They should be at least 1/2" BSP
nominal size and be in accordance with BS. 2879.
The central heating system should be in accordance with the
relevant standards listed on page 4.
Due to the compact nature of the boiler the heat stored within the
castings at the point of shutdown of the burner must be
dissipated in order to avoid overheating. In order to allow pump
operation after burner shutdown the boiler control box
incorporates a pump overrun facility. In order to make use of
this, the pump must be supplied from the terminals inside the
boiler. Note: for pumps requiring greater than 1.0amp current,
they must be connected via a relay.
WATER TREATMENT FOR HOT WATER AND
HEATING BOILERS
There is a basic need to treat the water contained in all heating
and indirect water systems, particularly open vented systems. It
is assumed, incorrectly, that because boilers are operating in
conjunction with what is apparently a closed circuit an open
vented system will not, under normal circumstances, allow
damage or loss of efficiency due to hardness salts and
corrosion once the initial charge of water has been heated up a
few times.
1mm of lime reduces the heat transfer from metal to water by
10%.
In practice the deposition of these salts is liable to cause noises
from the boiler body or even premature boiler failure. Corrosion
and the formation of black iron oxide sludge will ultimately result
in premature radiator failure.
Open vented systems are not completely sealed from the
atmosphere if proper venting and expansion of system water is
to be achieved. The same tank is used to fill the system with
water and it is through the cold feed pipe that system water
expands into the tank when the boiler passes heat into the
system.
Conversely, when the system cools, water previously expelled is
drawn back from the tank into the system together with a quantity
of dissolved oxygen.
Even if leakage from the heating and hot water system is
eliminated there will be evaporation losses from the surface of
the tank which, depending upon ambient temperature, may be
high enough to evaporate a large portion of the system water
capacity over a full heating season.
There will always be corrosion within a heating or hot water
system to a greater or lesser degree, irrespective of water
characteristics, unless the initial fill water from the mains is
treated. Even the water in closed systems will promote
corrosion unless treated. For the reason stated,
Caradon Ideal
Limited
strongly recommend that when necessary the systems
is thoroughly cleaned, prior to the use of stable inhibitor, which
does not require continual topping up to combat the effects of
hardness salts and corrosion on the heat exchangers of the
boiler and associated systems.
Caradon Ideal Limited
advise contact directly with specialists on
water treatment such as:
Betz Dearborn Ltd
or
Fernox Manufacturing Co. Ltd.
Widnes,
Tandem House, Marlowe Way,
Cheshire,
Croydon, Surrey, CRO 4XS
Tel: 0151 424 5351
Tel: 0870 601 5000
ELECTRICAL SUPPLY
WARNING
This appliance must be earthed.
A 230V - 50Hz mains supply is required, fused at 5amps.
Wiring external to the appliance MUST be in accordance with the
current I.E.E. (BS7671) Wiring Regulations and any local
regulations which apply.
The point of connection to the mains should be readily
accessible and adjacent to the boiler.
LOCATION OF THE BOILER
The boiler must stand on a non-combustible floor (i.e. concrete
or brick) which must be flat, level and of a suitable load bearing
capacity to support the weight of the boiler (when filled with
water) and any ancillary equipment.
If the boiler is mounted on a plinth then the dimensions must
exceed the plan area of the boiler by at least 75mm on each side.
The boiler must not be fitted outside.
Summary of Contents for Buccaneer GTE 5
Page 1: ......
Page 38: ...38 Buccaneer GTE Installation Servicing NOTES...
Page 39: ...39 Buccaneer GTE Installation Servicing NOTES...