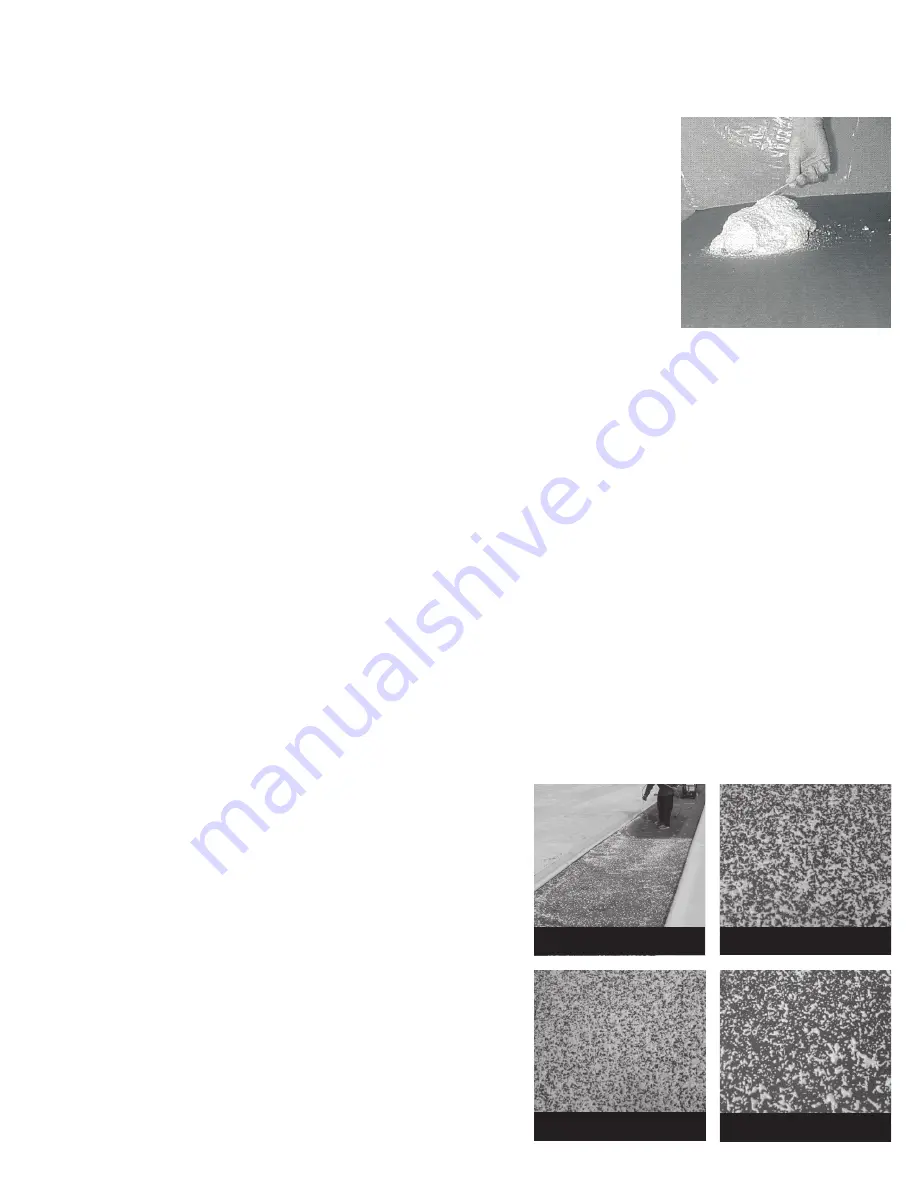
8
STEP 6: TACK-FREE TEST
Tack-free time refers to the time elapsed between when the product is dispensed and when the foam expands and cures initially, so
that it is no longer tacky to the touch. Tack-free time is an important property that can be used frequently before and during a job to
obtain an indication that the product is being dispensed to the proper A/B ratio.
1. Spray test shot.
2. Start timer as soon as you stop spraying.
3. Take a stick and gently touch the top of the foam. Each time you touch the
foam; do so at a different point on the stick.
4. Watch for the foam to stop adhering to the stick.
5. As soon as the foam is no longer tacky, stop the timer.
6. Check the timer for the tack-free time.
7. Refer to the Technical Data Sheet (TDS) to find the proper tack-free time
for the system being used.
8. For best results, perform a ratio test (see step 4).
9. With the nozzle removed, check that both chemicals flow with equivalent force.
10. Partial or complete blockage of one chemical port will result in off-ratio foam.
STEP 7: ADHESIVE APPLICATION
1. For optimum results, the recommended chemical temperature is 70-85°F (21-29°C), see TDS for product specific process
(core) chemical temperature recommendations.
2. Condition cylinders at ambient conditions to bring chemical that is too warm or too cold to optimal chemical temperature for
several days (see figure 1 on page 3).
3. Release the trigger safety. When pulling the trigger for the first time, it is recommended to trigger the gun only 1/2 to 3/4 open
until the desired output and spray pattern is achieved.
4. Conduct ratio shots (see step 4) before initial daily spray every two hours during the job or when a temperature change of more
than 10°F occurs. Maintain accurate records utilizing Daily Spray Log worksheet – key to troubleshooting and tech service.
5. Perform Adhesive Test Spray (see step 6).
6. Once the trigger is released, it must be reactivated within 30 seconds or a new nozzle must be installed.
7. Failure to do this could result in chemical leakage, spills, splashes or clogs which can ruin the dispensing unit and/or hoses.
Important
: After releasing the trigger of the Handi-Gun
®
, activate the trigger safety to prevent accidental discharge.
APPLICATION METHODS
Polyset
®
CR-20 (HFO) can be used to adhere TPO, PVC and KEE Fleece Back membranes to a variety of substrates including:
polyisocyanurate (Poly-ISO) insulation boards, DensDeck
®
and DensDeck Prime
®
, Securock
®
, structural concrete, smooth and
granulated modified bitumen roof decks (recover).
PREPARATION
All surfaces to be bonded must be clean, dry and free of any debris and smooth with no surface contamination. Broken, delami-
nated, wet or damaged insulation or cover boards must be removed and replaced prior to application of Polyset CR-20 (HFO).
PRODUCT USE - FLEECEBACK MEMBRANE
ADHESION (SPATTER)
Polyset CR-20 (HFO) is a single surface adhesive. It is spray applied
in a “Spatter Pattern” onto the roof, insulation or cover board
substrate by dispensing the adhesive in a spray pattern similar to the
action required when hand watering a flower bed. The spatter pattern
should yield a heavily textured, even coating of approximately ¼” to
½” nominal thickness height on the peaks of the spattered adhesive.
The seams of the membrane and the factory selvage edge must be
protected from overspray of the Polyset CR-20 (HFO). If overspray
does contaminate the seam area, immediately clean the seam area
with seam cleaner or Polysolv while the adhesive is still wet. The
bonding range of Polyset CR-20 (HFO) is approximately 1-10 minutes
from start of spraying and will vary according to ambient as well as
substrate temperature. The amount of substrate area that the
adhesive is applied to ahead of the membrane should be monitored
to prevent dry laid membrane. Care must be taken, particularly in
high temperature environments [90°F (32°C) and above], to ensure
that the adhesive has not dried or skinned over prior to embedding
the membrane.
NOTE: Membranes can be applied once the adhesive has achieved
sufficient bond strength to the immediate substrate to which it is adhered.
It is recommended that the contractor inspect the installed insulation for
proper adhesion and re-adhere any boards and/or corners that are not
adequately attached.
HEAVY SPRAY PATTERN
SUGGESTED SPRAY
PATTERN
LIGHT SPRAY PATTERN
SPATTER PATTERN
APPLICATION EXAMPLE