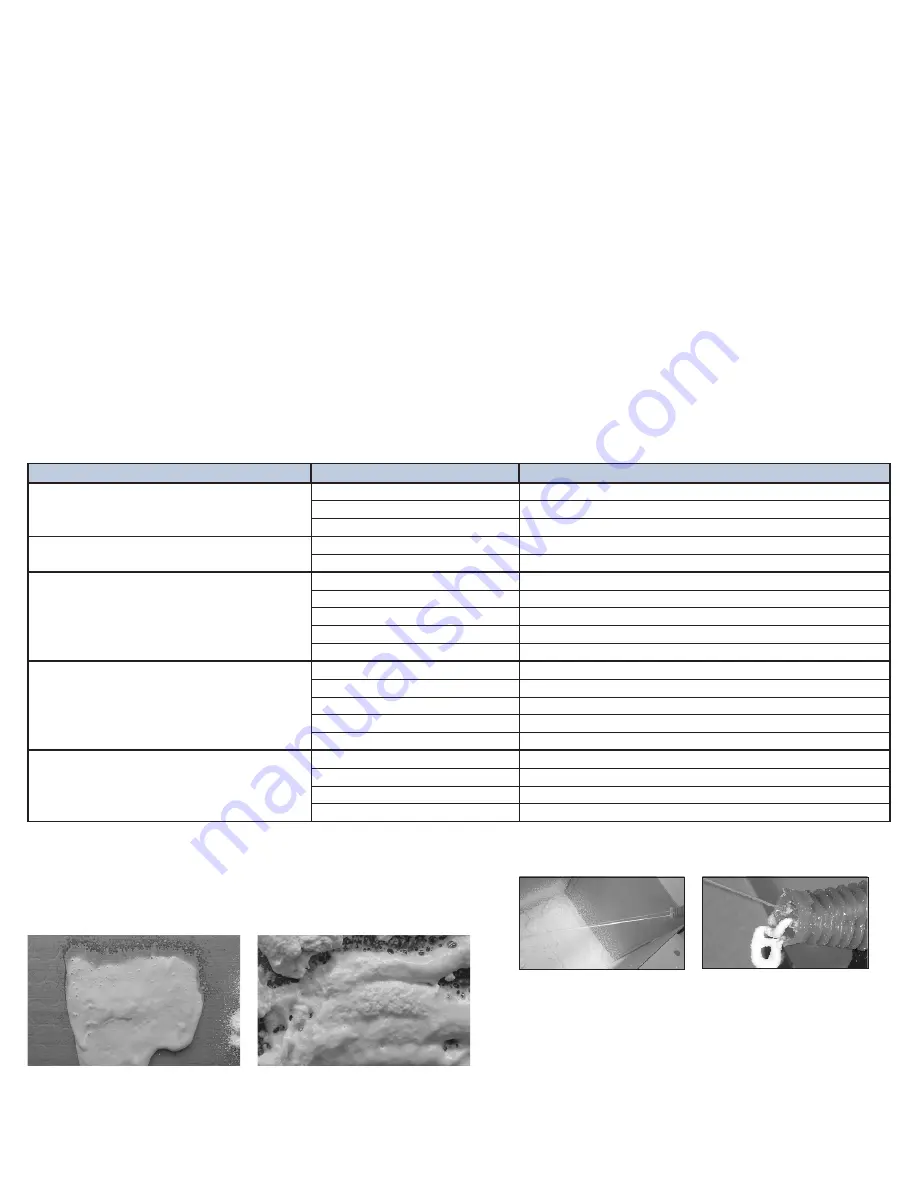
10
STEP 10: SYSTEM STORAGE AND RE-USE CONT.
5. Keep hoses under pressure. Do not flush/clean hoses with air, water or solvent. Depressurizing and/or cleaning hoses may
compromise the adhesive.
TO REUSE DISPENSING UNIT AFTER STORAGE:
1. Remove the used nozzle.
2. Check the face of the dispensing unit to make sure the outlet ports are clear and the face of the unit is free from dirt, chemical
or other debris. If necessary, use a soft cloth or rag to remove any cured adhesive or chemical from the face of the dispensing
unit. Use of enclosed petroleum jelly is recommended to cover the face of the unit in order to prevent further contamination or
if chemical is accidentally leaked into this area.
3. Polyset CR-20 adhesive should be between 70- 90°F (21-32°C). See TDS for formula specific shaking and temperature recom-
mendations.
4. Fully open all cylinder valves.
5. Dispense into waste containter to verify that both chemicals are being dispensed in approximately equal streams. The dis-
pensing unit is a disposable unit not designed for prolonged storage or continuous re-use. To help extend the storage life, it is
recommended to dispense a minimal amount of adhesive from unit at least once every three (3) days to ensure optimum flow
of chemical through hoses. Use of contents within 30 days of initial use is recommended.
VERY IMPORTANT:
As the hoses are exposed to the heat of the sun, especially in the summer months, the pressure in the hoses will
build up. Purging the hoses for a few seconds prior to spraying relieves the excess pressure and allows the chemical to flow in the proper
proportions.
TROUBLESHOOTING
For any technical service, contact ICP with a completed Daily Spray Log (A18015). Equivalent flow of both A-component and
B-component is required with all two-component polyurethane systems in order to obtain proper performance, curing and
optimum yields. If a problem occurs, the cause is typically due to uneven chemical flow that is caused by a blockage of one
of the chemicals.*
Problem
Possible Cause
Solution
Poor chemical flow
Cylinder valves not fully open
Turn cylinder valves counter-clockwise until they stop
Cylinder valves in incorrect position
Place cylinder valves in upright position
Material is too cold
Chemical temperature must be between 70˚- 85˚F (21˚-29˚C)**
Adhesive leaking from hose connections
Hoses not tightened
Tighten all hose fittings
Cross-threaded hose
Replace gun hose assembly
Dark crunchy adhesive/ off-ratio (A-rich)
Material is too cold
Chemical temperature must be between 70˚- 85˚F (21˚-29˚C)**
Clogged nozzle
Replace nozzle
Blockage of B chemical port
Clean gun face and apply petroleum jelly
Gun crossover
Replace hose
Empty cylinder
Replace cylinder
White spongy or shrinking adhesive/off-
ratio (B-rich)
Material is too cold
Chemical temperature must be between 70˚- 85˚F (21˚-29˚C)**
Clogged nozzle
Replace nozzle
Blockage of A chemical port
Clean gun face and apply petroleum jelly
Gun crossover
Replace hose
Empty cylinder
Replace cylinder
Sputtering from nozzle
Cylinders are empty
Switch to new system
Clogged nozzle
Replace nozzle
Hose blockage
Replace hose
Empty cylinder
Replace cylinder
*If system is still not fully operational, stop spraying and contact the distributor where purchased.
**See TDS for specific temperature recommendations.
With the nozzle removed, check that both chemicals
flow with equivalent force.Partial or complete blockage
of one chemical port will result in off-ratio adhesive.
Crunchy, friable, slow or non curing.
Darker brown in color.
“A-Rich” Adhesive:
Softer, white colored adhesive, with
shrinkage.
“B-Rich” Adhesive: