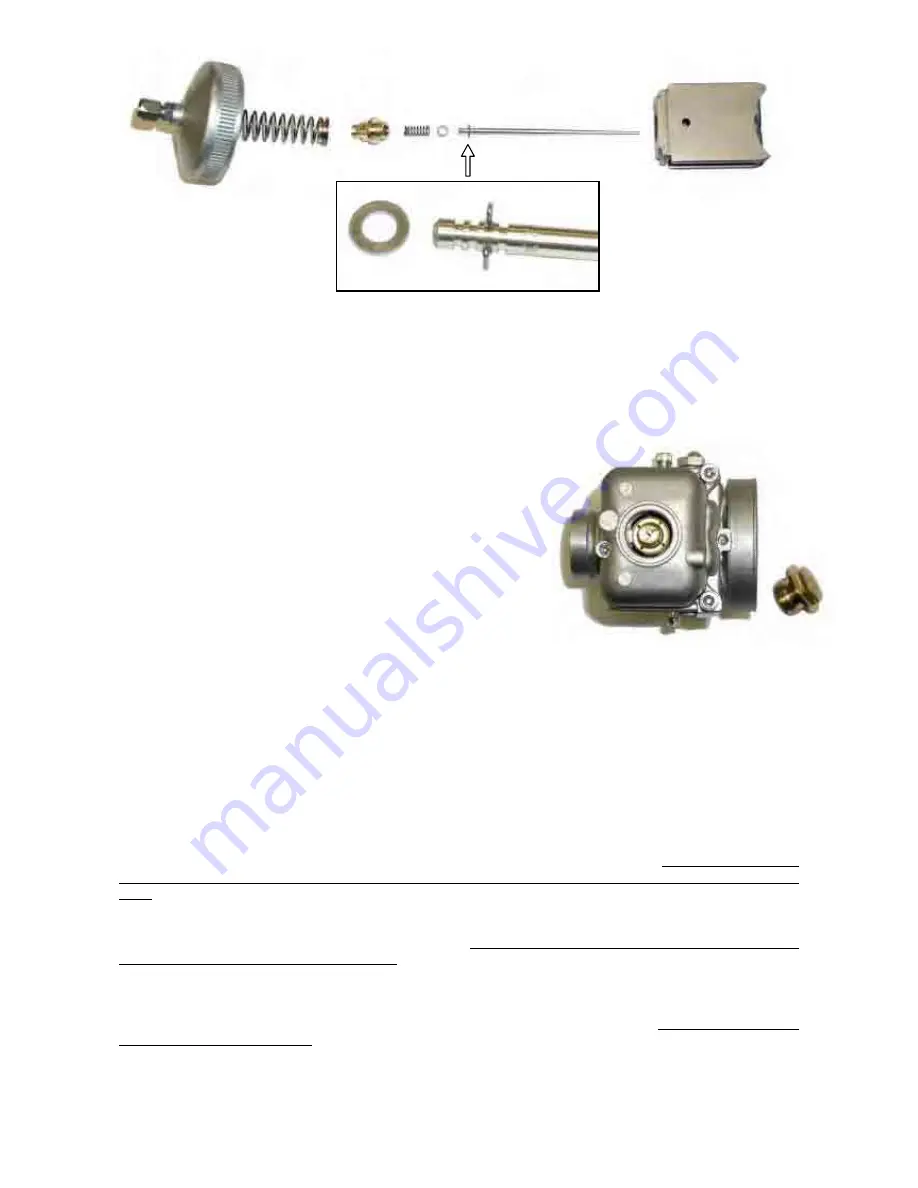
MAN-051 ING
25
We will get a richer carburetion by lifting the needle, that is, by moving down the retainer clip to a lower
notch; and on the contrary, a leaner carburetion is achieved lowering the needle, that is by lifting the retainer
clip to a higher notch (see fig.3). On the picture is shown the basic needle adjustment.
To reach the conical needle proceed as follow: screw out the upper locking ring on the carb., then pull off
the throttle gas together with the needle, release the throttle cable, and screw out the fixing screw on the
throttle gas.
The adjustment of the carburetion
at top RPM is mainly performed by means of:
•
The max. jet
By increasing the "H" max jet size (see fig.2),
we get a richer carburetion, and vice versa, a leaner one,
by decreasing the jet size.
To reach to the max. Jet, screw out the central plug on the
float chamber (see fig.4), or disassemble the float chamber itself.
As anticipated, there is no clear distinction among the areas
of influence of the different components, as they interact
and influence each other.
As a matter of fact, the max. jet affects, not only the
carburetion, at wide open throttle gas, but also the
whole mid range carburetion, even if less sensibly vs. the needle position;
indirectly, the needle position slightly influences the carburetion, at completely opened throttle.
In the same way, when the throttle is slightly opened, the effects of the min. jet and the air screw
superimpose with the effect of the conical needle position.
To properly adjust the carburetion according to the ambient conditions, we are giving some indicative
parameters, to adapt the max. jet size as a function of the variation of the ambient temperature and the
altitude at which the engine is operating.
As you know, carburetion, that is, the exact quantity of fuel to be mixed to a given quantity of air, is
influenced by atmospheric factors, such as temperature and pressure. The more the temperature drops, the
more the air density increases and consequently, there will be more molecules of gas in the same volume.
As the carb. mixes always the same fuel quantity this would be insufficient and the carb. will provide a leaner
mixture. In these conditions, as you are aware, when operating with a leaner mixture, the engine runs the
following risks: overheating, insufficient lubrication, detonation, seizure; for this reason the carburettor setting
must be adjusted by increasing the max. jet size by about 2-3 points for every 6°C external temperature
drop.
Of course, on the contrary, the more the temperature rises, the more the carburetion becomes richer and
gives origin to less critical consequences than the ones experienced with a leaner carburetion. So, also in
this case, it is suggested to optimize the carb. setting , by decreasing the max. jet size by about 2-3 points
for every 6°C external temperature increase.
The variation of the atmospheric pressure, which is significant when varying the altitude at which the engine
is operating, gives origin to such a phenomenon; by decreasing the altitude, the atmospheric pressure
increases, consequently in the same air volume sucked by the engine, more molecules of gas are present
Therefore, in this case too, a carb. adjustment is required; increase the max. jet size by about 2-3 points for
every 350m altitude decrease.
Fig.3
Fig.4