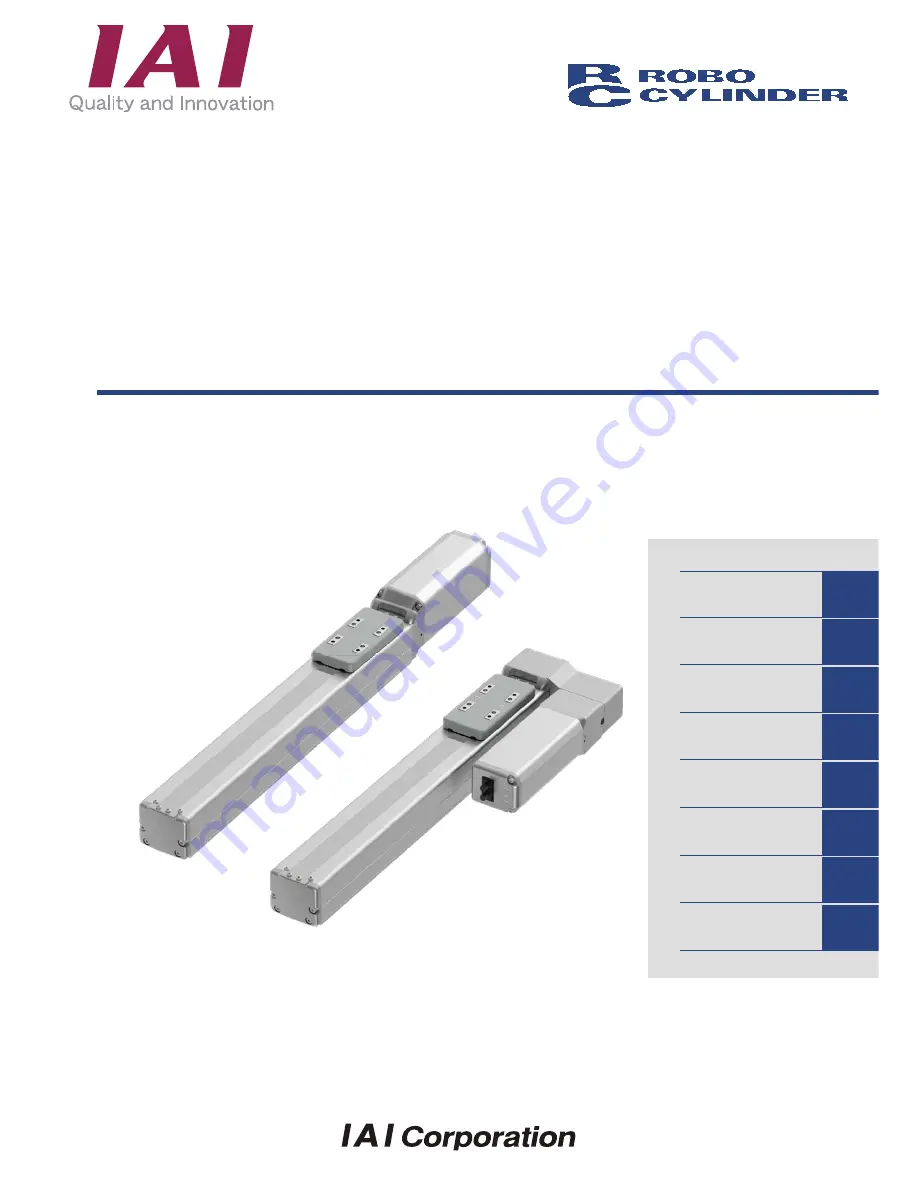
Slider Type
First Edition
ME3769-1A
RCS4- SA4C/SA6C/SA7C/SA8C
SA4R/SA6R/SA7R/SA8R
RCS4CR- SA4C/SA6C/SA7C/SA8C
Specifications
Installation
Maintenance and
Inspection
External Dimensions
Life
Warranty
Appendix
ROBO Cylinder
®
ch.
1
ch.
2
ch.
3
ch.
4
ch.
5
ch.
6
ch.
7
ch.
8
Instruction Manual
Connecting with
the Controller
Summary of Contents for ROBO Cylinder RCS4- SA4C
Page 2: ......
Page 18: ...Names of the Parts Intro 12 Cleanroom Type Motor Straight Type ...
Page 56: ...1 37 1 Specifications ...
Page 78: ...2 21 2 Installation ...
Page 79: ...Connecting with the Controller 3 1 Connecting with the Controller 3 1 ROBO Cylinder Chapter ...
Page 140: ...7 3 7 Warranty ...
Page 141: ...Appendix 8 1 Index 8 1 8 2 Revision history 8 3 ROBO Cylinder Chapter ...
Page 145: ......