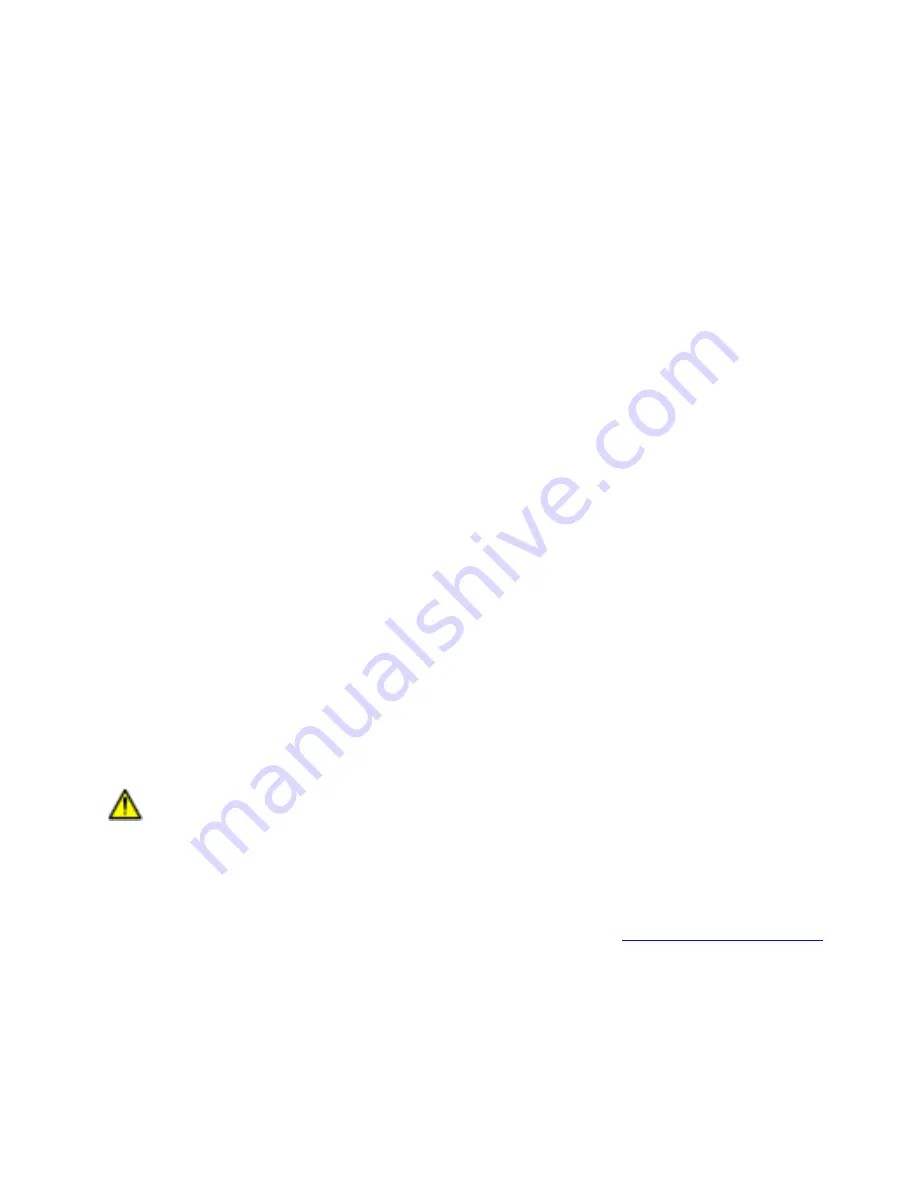
3
ATTENTION NOTES:
IAC Industries takes great care in the packaging of its products, however damage
can occur during shipment. Check all packages and parts for any signs of damage. If
damage is evident STOP and contact the carrier that delivered your order. Request a
freight claim inspector to document the damage and begin the freight claim process.
Tools required to assemble your WM BENCH products are:
7/16” and 1/2” wrench or socket with ratchet.
Phillips screwdriver 8” long.
Utility knife.
Safety glasses and light duty protective gloves.
NOTE: Power tools are NOT recommended unless they are equipped with a torque
limiting device which can limit the torque to 10 foot lbs maximum at aluminum
attachment points, and 15 foot lbs maximum for all other attachment points.
Unpack your order and separate like parts into separate areas. Be careful not to
damage parts as they are being moved around and put into position. Also be sure all
parts are removed from the packing materials before these materials are thrown
away.
Locate the Hardware Kits and keep them in a central area. If the assembly is going to
take more than one day, all individual hardware pieces should be returned to a
central location.
Check all parts and Hardware Kits against the itemized packing list found with the
assembly instructions. If you believe there are parts missing from your order please
contact IAC Industries customer service HOTLINE at 800-989-1422.
If your order has ESD worksurfaces or accessories please review page 35 for helpful
instructions and cautions before you begin assembling the workstations.
WARNING
:
ALL PARTICLE BOARD USED IN IAC INDUSTRIES PRODUCTS ARE SOURCED ONLY FROM VENDORS THAT
ARE CARB ATCM PHASE 2 AND TSCA TITLE VI COMPLIANT WITH VALID CERTIFICATES
.
Drilling, Sawing, Sanding
or Machining Wood products can expose you to wood dust, a substance known to the state of California to cause cancer. Avoid inhaling
dust generated from wood products or use a dust mask to other safeguards for personal protection. This product can expose you to
chemicals, including formaldehyde, which is known to the state of California to cause cancer, and methanol, which is known to the state
of California to cause birth defects or other reproductive harm. For more information please visit,
COPY OF VENDOR CERTIFICATE AVAILABLE UPON REQUEST.