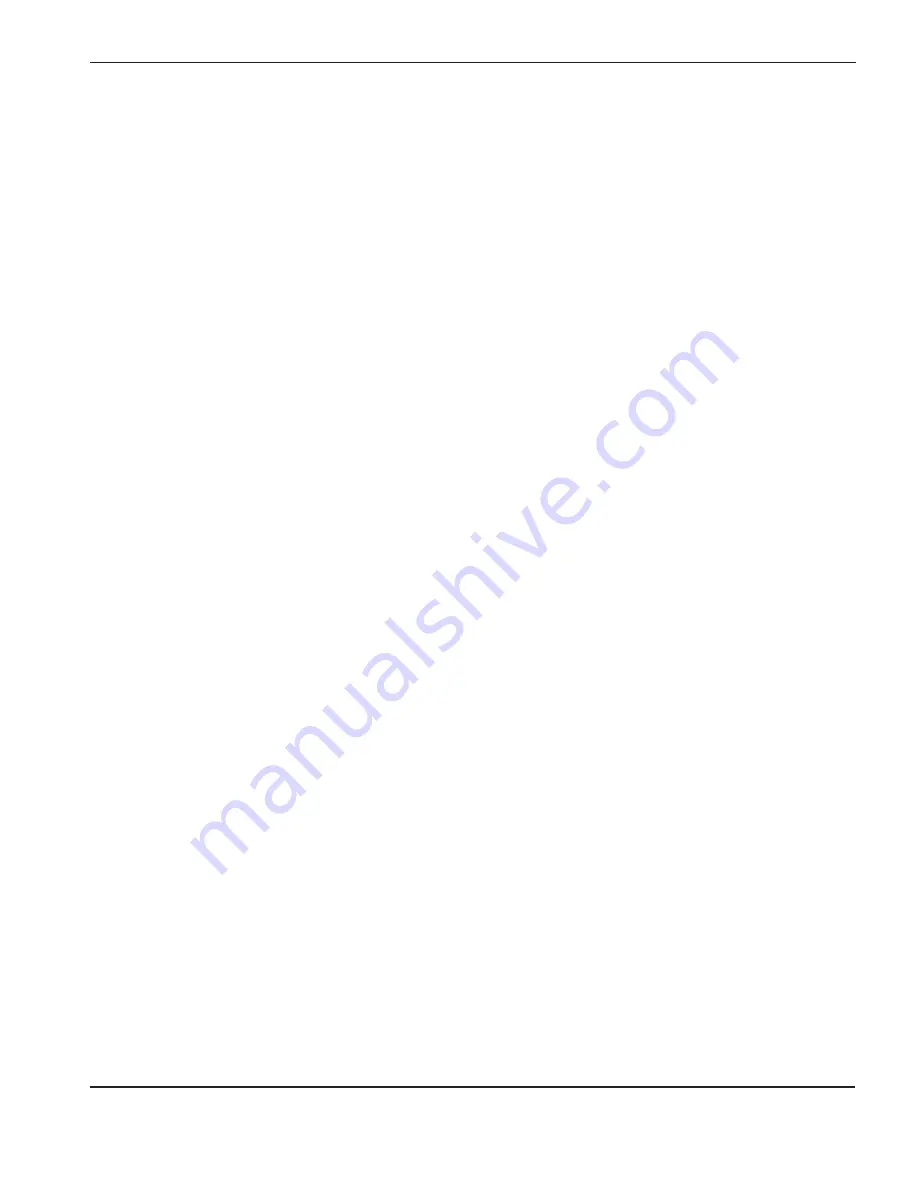
Component ReplaCement
powermax
65/85
Service Manual
6-21
Install the new power board (380/400V CE)
1. Position the left edge of the power board on a slight angle toward the front end panel, so the previously removed
wire connectors will reach their intended locations.
2. If a CNC interface is installed on the power supply, plug the respective wire connectors into the J21 and J33 power
board connectors.
3. Plug the respective wire connectors into the J3, J4, J5, J6, J7, J15, and J20 power board connectors.
4. Slide the power board into the mounting position while routing the gate drive wires through the opening in the
board.
Note: Make certain all power board connection wires (11 wires with metal ring terminals) are positioned in front of
the power board.
5. Install the four board mounting screws using a #2 Phillips screwdriver to tighten to 10 in-lbs (11.5 kg cm).
6. Install the three heat sink mounting screws using a #2 Phillips screwdriver to tighten to 15 in-lbs (17.3 kg cm).
Note: It may be necessary to pull the top of the front panel slightly forward to install the upper left heat sink
mounting screw.
7. Connect the electrode wire (black) to J29 using a #2 Phillips screwdriver to tighten the screw to 20 in-lbs
(23.0 kg cm).
8. Install the two pilot arc IGBT screws, securing the nozzle wire (red) to the board with the left screw. Use a
#2 Phillips screwdriver to tighten both screws to 20 in-lbs (23.0 kg cm).
Note: All screw mounting holes which secure a wire to the power board, except for J29, have a yellow silkscreen
outline on the board depicting the placement of the ring terminal.
9. Install the four diode screws, securing the output inductor wire to the board with the upper left screw. Use a
#2 Phillips screwdriver to tighten all four screws to 20 in-lbs (23.0 kg cm).
10. Install the five input bridge screws, securing the MOV sub assembly with the two screws on the right. Use a
#2 Phillips screwdriver to tighten all five screws to 20 in-lbs (23.0 kg cm).
11. Install the four snubber resistor screws using a #2 Phillips screwdriver to tighten to 15 in-lbs (17.3 kg cm).
12. Verify that the gray dot on each capacitor is visible through the two viewing holes. Start the four capacitor screws
by hand, then use a #2 Phillips screwdriver to tighten to 20 in-lbs (23.0 kg cm).
13. Connect the AC input wires and PFC inductor wires at J1, J2, J13, J23, and J24 using a #2 Phillips screwdriver.
Tighten all five screws to 20 in-lbs (23.0 kg cm).
14. Connect the work lead at J27 and the shorter transformer wire at J30 using a #3 Phillips screwdriver to tighten the
screws to 30 in-lbs (34.6 kg cm).
15. Secure the 3uF capacitor and the remaining transformer wire to the board using the three inverter IGBT screws.
Use a #3 Phillips screwdriver to tighten the screws to 30 in-lbs (34.6 kg cm).
16. Plug the gate drive wires into their respective power board connectors (J18, J19). Gently pull on each wire to
ensure that they are fully seated.
Summary of Contents for Powermax 65
Page 1: ...Service Manual 807120 Revision 1 Plasma arc cutting systems ...
Page 10: ...vi powermax65 85 Service Manual ...
Page 16: ...Table of Contents xii powermax65 85 Service Manual ...
Page 32: ...Specifications 1 16 powermax65 85 Service Manual ...
Page 182: ...Troubleshooting and System Tests 5 56 powermax65 85 Service Manual ...
Page 216: ...Component Replacement 6 34 powermax65 85 Service Manual ...
Page 244: ...Wiring Diagrams 8 2 powermax65 85 Service Manual ...