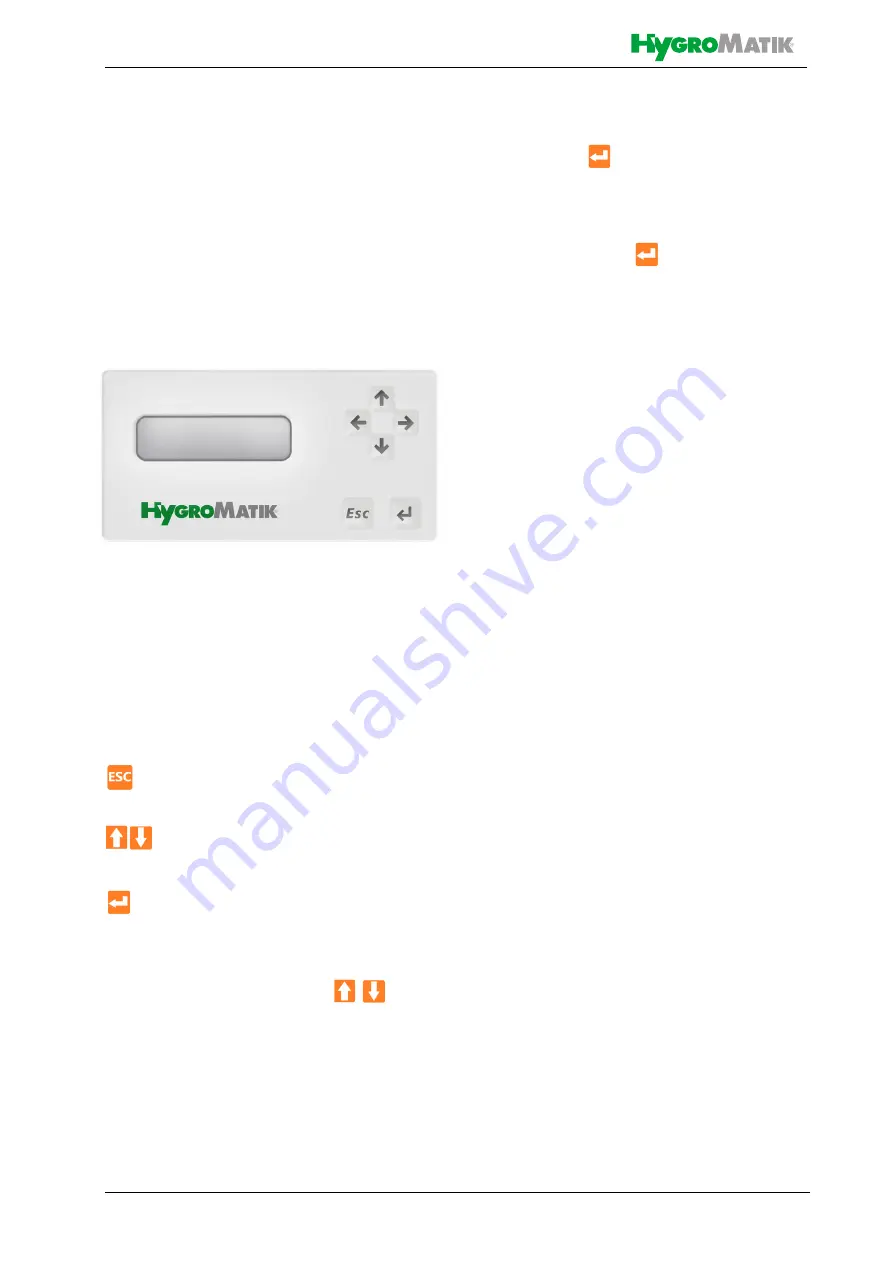
Page 38
11. Control
The whole operation of the reverse osmosis
unit WL-ROL is controlled by a microproces-
sor.
The control-system enables the production
process and the control of the RO-unit. The
measured values are shown on a LC-display.
The control has the protection class IP65.
11.1 The control panel
The control panel is separated into three
zones:
•
the 2 operating keys ESC, ENTER
•
the 4 arrow keys
•
LC-display
The
operating keys
are used to navigate
through the menus and submenus. The func-
tion of the keys is:
„ESC“: Cancel or return to the previous
level
Arrow keys: Move within a menu, a
submenu or a selection list
„ENTER“: Acceptance and storage of a
selected setting
By pressing the arrow keys
you can call up the read values:
•
Permeate conductivity
•
Operating hours
•
Remaining time (hours) until the next
service
Access to the main menu:
»
press
or about 2 sec, the dis-
play shows “PASSWORD 0000“
»
enter the password using the arrow
keys (0077)
»
confirm with
The control system regulates the automatic
sequence for start-up, production, process
shut-down, as well as for periodic rinses by
controlling the following actuators:
•
Feed water valve (V
FEED
)
•
Permeate flush valve (V
PER
)
•
High pressure pump (P
HP
)
•
Dosing pump Antiscalant (P
ASC
)
•
Fault signal/alarm (potential-free
changeover relay)
The controller is equipped with the following
digital inputs for monitoring the process:
•
Overpressure switch (PS
HIGH
)
•
Low pressure switch (PS
LOW
)
•
Level of permeate vessel low (PS
Min
)
•
Filling level permeate vessel full ( PS
MAX
)
•
External stand-by signal (IN
SB)
•
Error dosing pump antiscalant (IN
PASC
)
•
Malfunction feed water pre-filter (IN
FIL
)
Furthermore, the controller has a conductivity
measurement (not temperature compen-
sated) for monitoring the permeate quality,
with a freely adjustable limit value.
This means that the unit is switched off and a
fault message is output if the limit value of the
permeate conductivity is exceeded during
operation.
Summary of Contents for WL-ROL 160-1200 Series
Page 1: ...FlexLine Reverse osmosis plants MANUAL WLROL EN E 8881184 WLROL ENj WL ROL 160 1200...
Page 62: ...Page 62...
Page 65: ...Page 65 13 Declaration of Conformity...
Page 66: ...Page 66...
Page 72: ...Page 72 This page intentionally left blank...
Page 73: ...SPA Page 73 This page intentionally left blank...