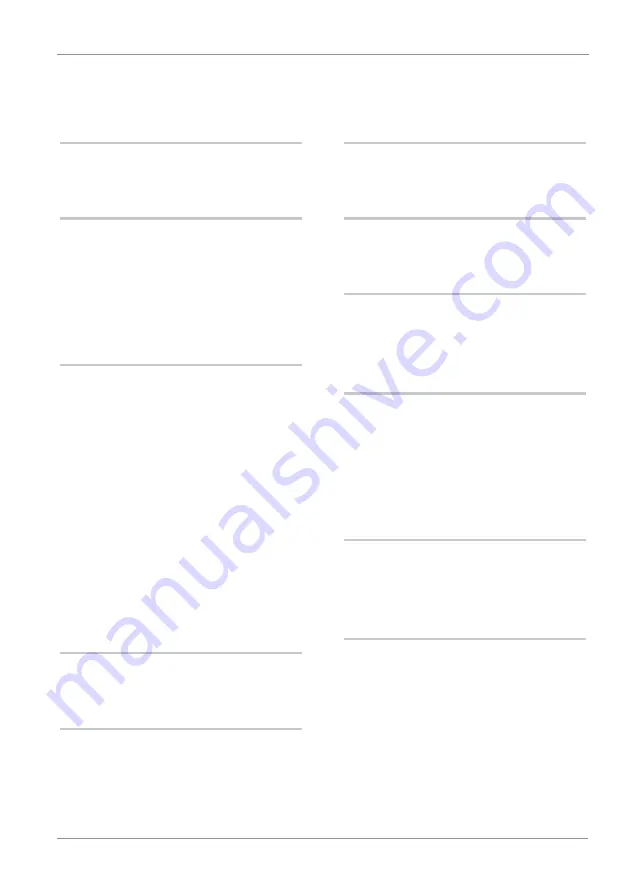
HYDAC FILTER SYSTEMS GMBH
Index
MoWa OLFP-1-T002 4469047 en-us lq
63 / 64
Index
B
Branches
C
calculating pressure loss
Clogging indicator
Differential pressure indicator
D
Differential pressure indicator, electrical
VM x C.x
VM x D.x /-Lxx
Differential pressure indicator, visual
VM x B.x
VM x BM.x
differential pressure/dynamic pressure
dynamic pressure/differential pressure
E
exclusion of liability
H
Hotline
I
Imprint
M
manufacturer
P
Person authorized with the documenta-
tion
S
Service
Servicepartners
siphoning effect
Support
T
Terms and Conditions
Terms of Delivery
W
warranty
Summary of Contents for OLFP-1
Page 64: ......