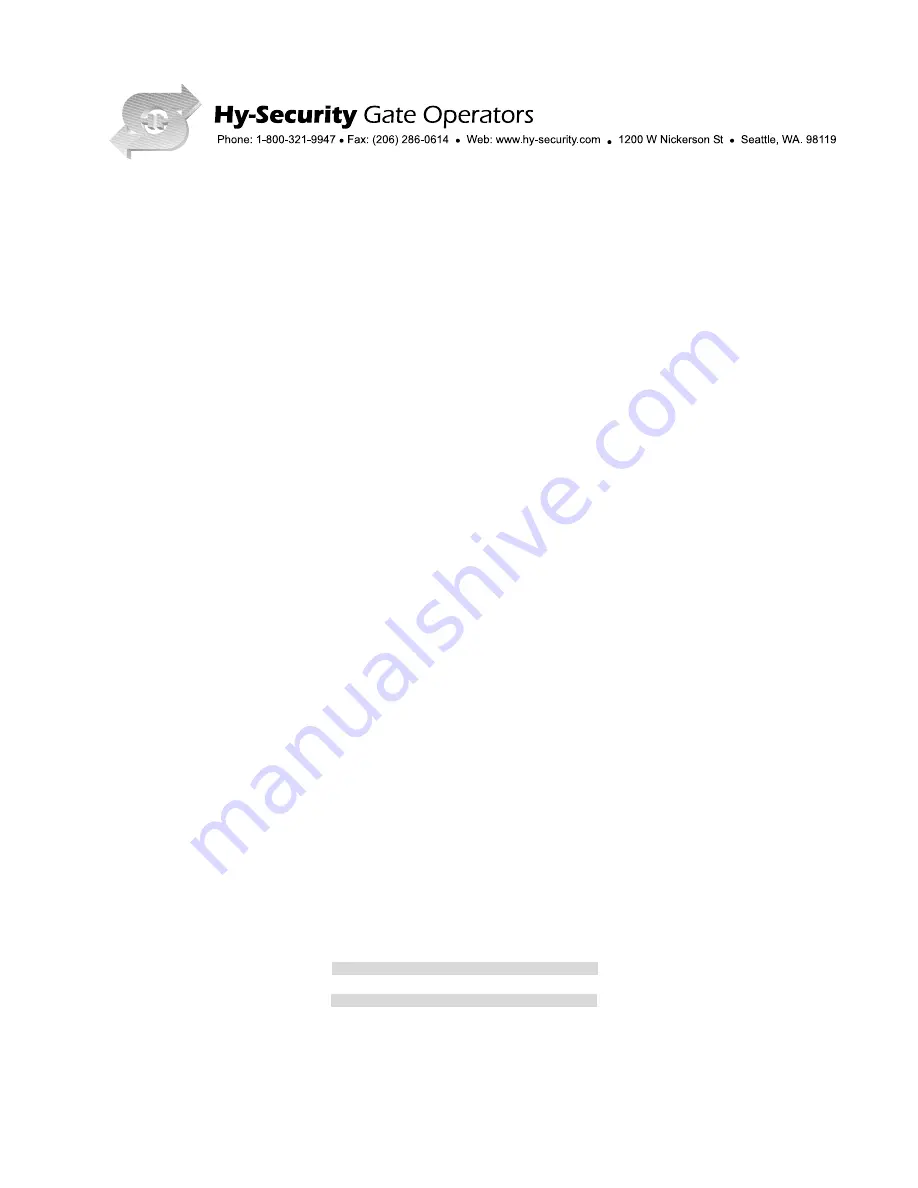
Operator Maintenance
Operator Maintenance
Operator Maintenance
Operator Maintenance
Operator Maintenance
Hydraulic System
Fluid Level:
Under normal conditions, hydraulic systems do not consume oil. Before adding any oil, check the
system thoroughly for leaks. Remove the bright metal plug in the tank, fill to plug level, then replace plug. We
recommend our
Uniflow
hydraulic oil, part number H-004, which is sold in one gallon containers by our distribu-
tors. Automatic transmission fluid may be used, although its performance in cold weather will be sluggish unless
the operator is well heated.
Do not use brake fluid.
Look for leaks:
Occasionally there may be slight seeping at the fittings after some usage. Tightening of the fittings
will usually correct the problem. If the leaking persists, replace "O" rings, fittings or hoses, if required. No further
leaks should occur.
Oil Change:
A hydraulic system does not foul its oil, unlike a gas engine, so oil changes do not need to be frequent.
Rather, heat breakdown is the main concern in a hydraulic system. If the unit is subjected to high use, especially in
a warm climate, change the oil more frequently. In general, we recommend draining the reservoir and replacing the
oil at five or ten year intervals.
There are several ways to change the hydraulic oil, depending on the type of operator being serviced. If you
don’t know how to drain the oil, contact your distributor for directions. Refill with new
Uniflow
hydraulic oil
(available from your distributor). To avoid overfilling, never pour into the port where the black breather cap is
located. Instead, remove only the bright metal plug in the tank. Slowly pour the oil into the tank until the oil is
within one inch of the filler port. Replace the plug and wipe up any spilled oil.
Cold Weather:
1. Check that your reservoir is filled with
Uniflow
high performance oil.
2. Ice can partly or totally jam gate operation. Check by operating the gate manually.
Electrical Controls
Before servicing, turn off power disconnect switch
No routine maintenance is needed for the electrical system or controls. If the environment is very sandy or dusty, seal
all holes in the electrical enclosure. Blow dust out of the electric panel with compressed air. A qualified electrician may
troubleshoot with the aid of the electrical drawings in Appendix 4.
If it is necessary to call a distributor for assistance, be sure to have your model and serial number ready. Other helpful
information would include the name of the job, approximate date of installation, and the service record of the operator,
especially any work that has been done recently. Be prepared to describe as exactly as you can what the machine is or
is not doing. Describe any unusual sounds or location of oil leaks.
How to Adjust the Pressure Relief Valve:
To check your relief valve setting, first disconnect one of the hoses.
Run the operator either open or closed (the gate will not move with the hose disconnected. The relief valve is found
on the rear of the hydraulic power unit. It has a hex adjusting head and lock nut. To adjust, loosen the lock nut and
screw the threaded bolt clockwise for increased pressure, counterclockwise to decrease pressure.
MODEL
FACTORY SETTING
111 Series
750 psi
SS, E Models
1000 psi
EX Model
1300 psi
444 Series
1300 psi
Do not attempt to use the relief valve as an entrapment protection device. Photocells or gate edges are the best
methods to protect pedestrians and reserve power to the drive gate.
5/25/00 G39