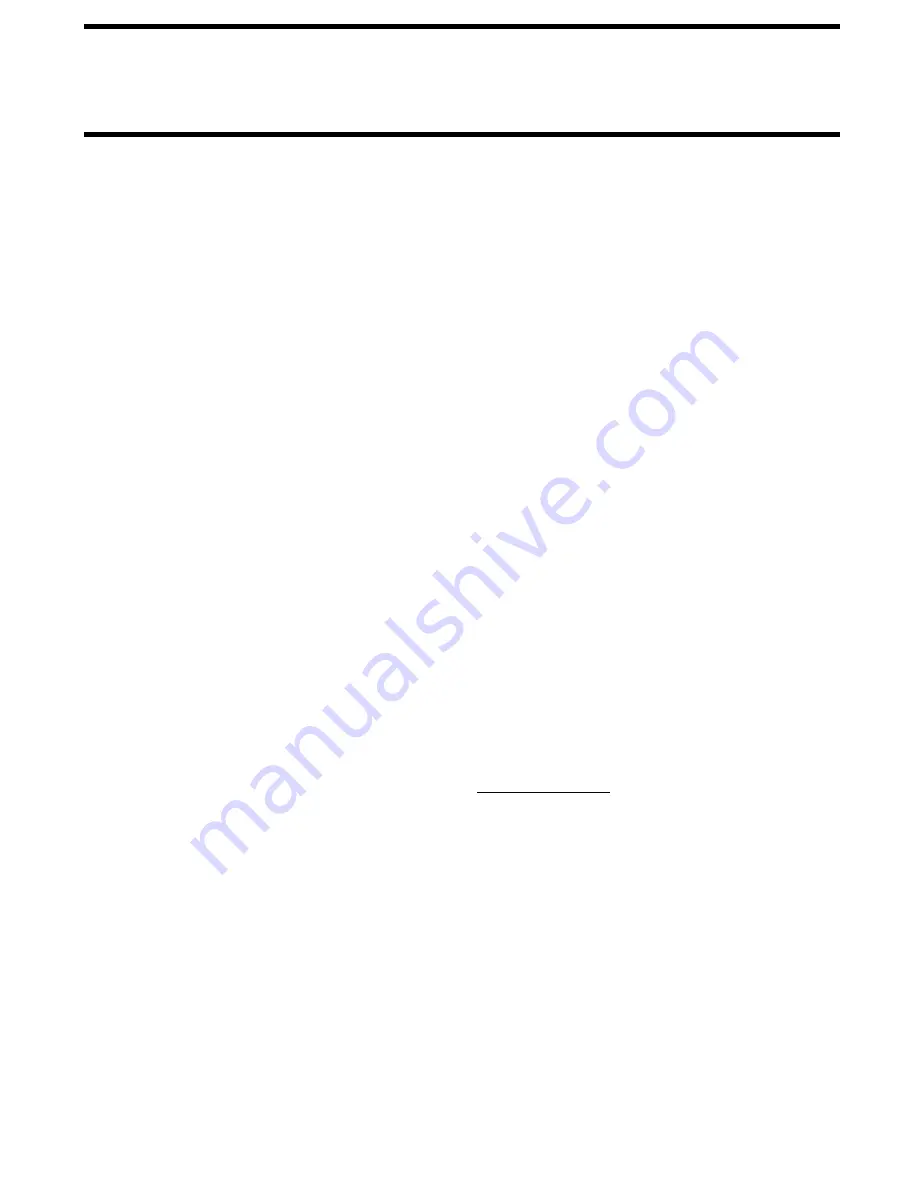
COMPONENT INSTALLATION
MI35.2006
15JAN01
If the valve is to be put near the left front tire, care
should be taken to keep it as far outboard and rearward as
possible. If mounted too close to the tire, the valve may be
struck by the tire on rough or bumpy roads or when turning.
2. MOUNTING THE VALVE
1. LOCATING THE VALVE:
the left of the driver’s seat. This location is not vital but is most
convenient. If the need arises the valve can be put elsewhere
such as alongside the couch or chair. Be sure to check under-
neath to see that the bottom of the valve will be accessible
It is not advisable to put the valve in a compartment or in the
dash.
The joystick (200 Series) light panel may be flush mounted in
a flat surface such as the dash or may be surface mounted
on the floor or other convenient locations by using the 1.75"
tall spacer box. When surface mounting the light panel ad-
jacent to the valve be sure to orientate the panel so the yellow
lights coincide with the coach. Drill a 1" hole beneath the light
panel to pass the wiring through. Do not mount the light panel
until all wiring is complete. Always leave enough wire length
in the spacer box to allow lifting the panel for repair. Be sure
to seal the 1" hole when finished. Never flush mount a panel
in the floor. The panel must always be protected from dirt and
and water. When flush mounting the light panel, a rectangular
hole with 45 degree corners matching the back of the panel
will need to be cut in the mounting surface.( See Template at
the end of Part III.) There must be a minimum clearance of 2"
behind the mounting surface to allow for the panel and the
from the top. Secure valve and cover plate at the same time
using four #10 x 3/4" Phillips head screws. Caulk around the
underside of the valve where the box meets the floor.
3. LOCATING AND MOUNTING THE PUMP:
4. HYDRAULIC HOSES
Do not attach hoses or wiring to any fuel
CAUTION:
When connecting hoses and wiring harnesses to the
kick down jacks always check that the jack can swing from the
horizontal position to a position 45 degrees beyond the ver-
tical position, without kinking the hose or without tight wires.
The jack must also be able to freely fold back to its stored
position.
Straight Acting Jacks:
wiring harnesses must have enough slack to allow free move-
ment of the jack.
There are different lengths of hoses to be routed to the four
leveling jacks. (Refer to the Hydraulic Hookup Diagram)
Straight Acting Jacks:
and connect it to the hose fitting. 90 degree swivel fittings are
available if needed for clearance.
IMPORTANT:
A LEAKING HOSE CAN POSE A FIRE HAZARD.
A KICK DOWN JACK WILL
SWING UP ABRUPTLY WHEN IT IS RELEASED.
EXTREME CAUTION:
PART III
Can pivot several inches. Hoses and
Route the hose to the top of the jacks
The valve is normally placed to
:
not always possible, it is desirable to put the pump assembly
under the hood compartment where it is easily accessible for
service or fluid check and refill. The distance of the pump from
the valve is limited by the 7’ hose provided and the battery
cable although a longer hose and cable may be used if available.
: It is important to keep the ends of
the hoses plugged during installation to prevent any dirt from
entering the system. Hoses should be routed away from any
heat emitting items such as engine or exhaust components.
A good location is along the outside of the frame rail. It may
be necessary to build a heat shield and/or adequately insul-
ate the hoses. Care should be taken to avoid sharp edges.
NOTE:
NOTE:
The pump and pump relay should be protected from direct
NOTE: Do not remove fitting caps until attaching the hose
to the valve.
The joystick valve (200 Series)
requires a 3.25 inch by 7.00 inch hole cut at the desired lo-
cation. The valve should be mounted so that the front and the
aft movement of the control lever is in line with the coach.
Be sure there is adequate clearance for full movement of
all levers. Before cutting the hole, be sure to check underneath
road dirt.
wiring.
The joystick valve (200 Series) will drop through the hole
Although it is
or brake lines. Do not run hoses across the transmission
crossmembers on front control coaches.
for wiring, structural parts, or other items that may create a prob-
lem. Also be sure to leave enough room to connect all hy-
draulic hoses.
existing hose end, tighten the hose end to snug plus 1/4
tighten the hose end 1/3 turn (2 FLATS). If tightening an
make the hose end snug (finger tight) on the fitting, then
Tightening of hose ends: If tightening a new hose end,
turn (1 FLAT).