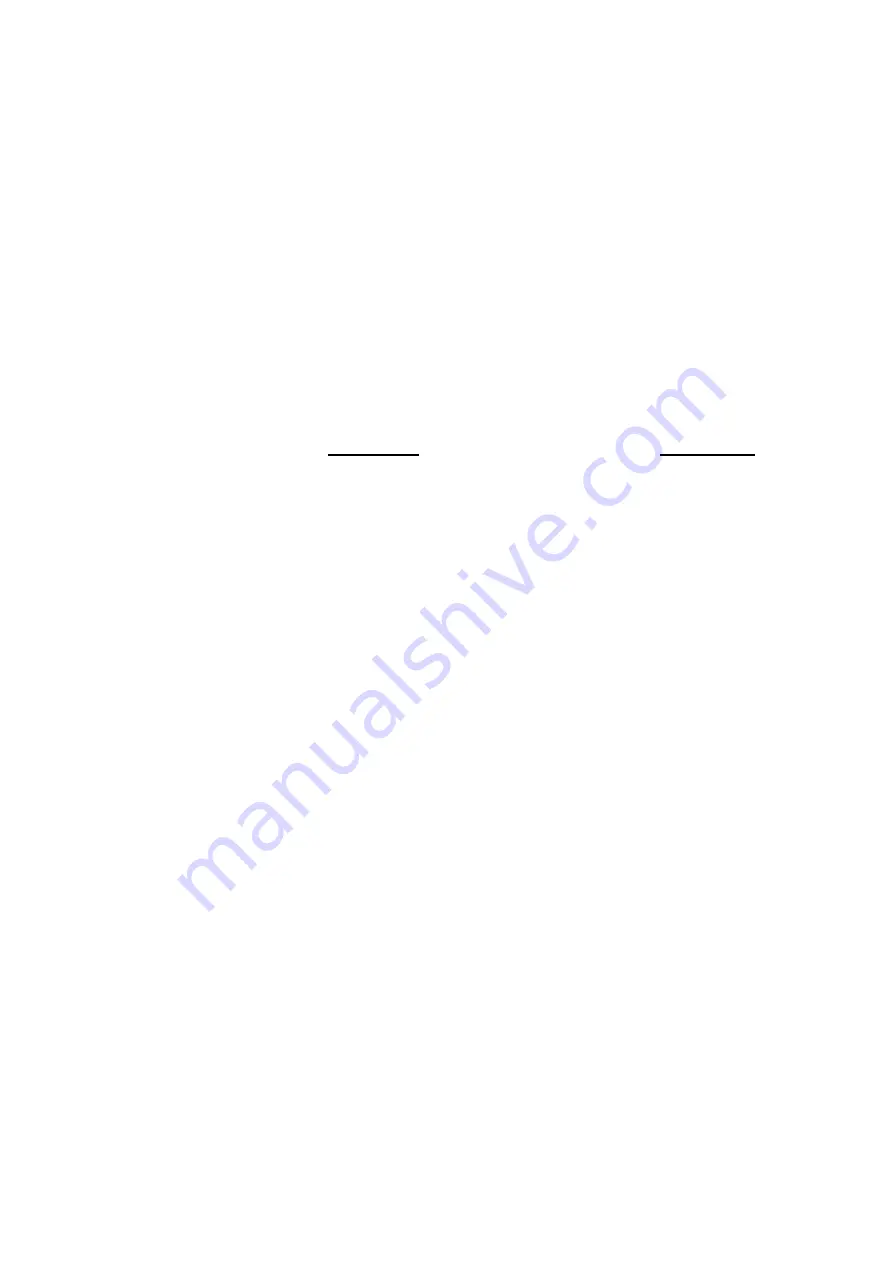
25
9. MAINTENANCE
9-1 DAILY CHECKING
In order to quaratee trouble-free, long use of the machine, it is very important
to elaborately check each part of the machine periodically. If and trouble or
checking. Be sure to immediately remedy it. The daily checking and
maintenance schedule that should be at leaste performed before starting daily
work is shown below.
DAILY CHECKING SCHEDULE
Check up
Frequency
(A)
Before starting machine
2. Planning head operation:
(1)
Velocity changes of main spindle:
To change the velocity, all that is needed to pull the lever, please note that
under no circumstance the velocity should be changed while the motor is
still in motion.
(1) Visually check the appearance of the machine
-Daily
(2) Check if any object is located within the
moveable range of the table
-Daily
(3) Clean the chuck and the circumference or the
spindle table.
-Daily
(4) Check the gib
-From time to time
(5) Check the slide way for damage, score or other
defects. If any damage or score is found,
flatten using an oil stone.
-Daily
(6) Check lubricating lubrication pump using
furnished.
-Daily thank
capacity : 2.2
Summary of Contents for 19002
Page 1: ...HU 200K...
Page 8: ...7 FOUNDATION 2 FRONT HU 200K...
Page 17: ...16 Photo C Photo D Photo C D...
Page 34: ...33 HU200K...
Page 36: ...35 HU200K...
Page 39: ...38 HU200K...
Page 42: ...NOTE 3 4 Coolant ON OFF Switch 5 Ram JOG Button 6 Emergency Stop Button...
Page 48: ...NOTE 9 ELECTRIC CIRCUIT DIAGRAM...
Page 50: ...NOTE 11...
Page 53: ...2019 V1...