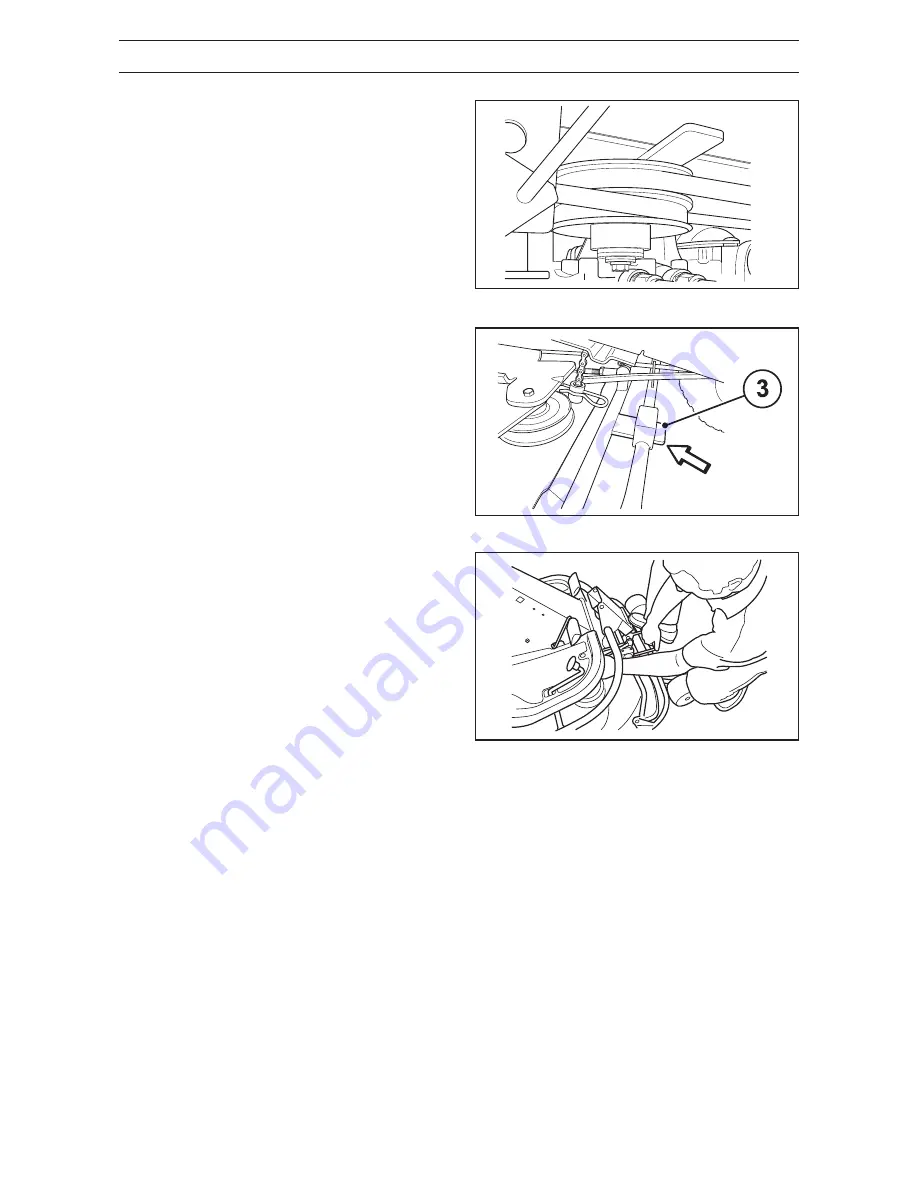
42
– English
2. Fit the centre belt in position on the centre
pulley.
MAINTENANCE
3. Reset the cutting unit in the mowing position.
Make sure that the tongue (3) mates with the
loop on the underside of the machine.
8009-695
4. The belt is fitted on the cutting unit’s drive pulley
once the unit has been pushed back into its rear
position.
8009-595
8009-122
Summary of Contents for Rider Pro 15
Page 2: ......
Page 69: ...English 67 WIRING DIAGRAM 8009 588 Rider Pro 15 18 ...
Page 70: ...68 English WIRING DIAGRAM Rider Pro 18 AWD 8009 679 ...
Page 80: ...78 English SERVICE JOURNAL Action Date mileage reading stamp signature ...
Page 81: ...English 79 SERVICE JOURNAL Action Date mileage reading stamp signature ...
Page 82: ...80 English SERVICE JOURNAL Action Date mileage reading stamp signature z RÆh 6j ...
Page 83: ...English 81 ...