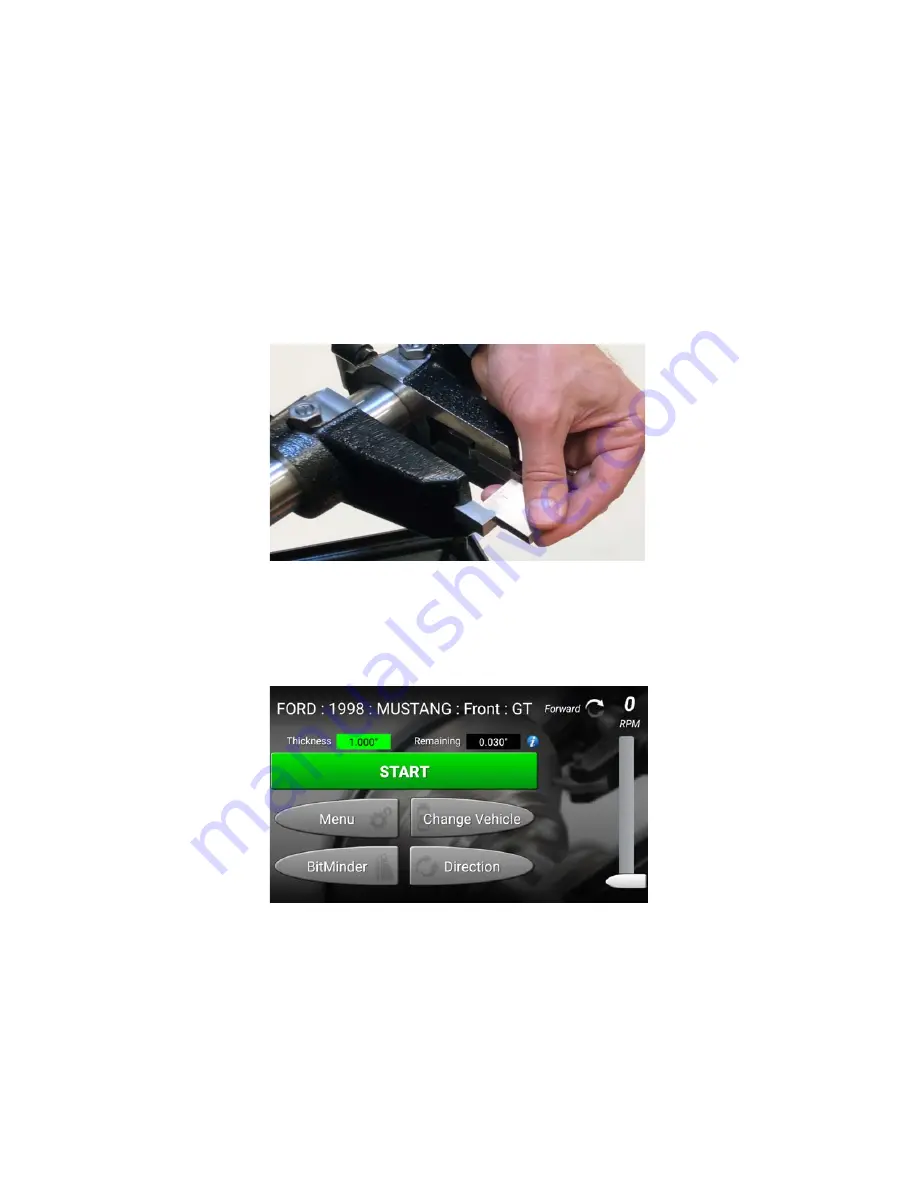
1
DIGI-CAL OPERATIONS
Calibration
1.Select Calibrate Digi-Cal from Menu.
2.Separate the tool holders so the gage block can easily pass between the cutting bits. Then lock
one tool holder in place. Place the calibration block between the cutting bits. Move the cutting bits
together until they both barely touch the calibration block. Press “OK” to continue.
Figure 1:
3. Calibration is complete. Push OK.
On Car Operation
1. Begin by selecting the appropriate vehicle from “Change Vehicle”.
Figure 2:
2. Select a vehicle manufacturer.
3. Select year.
4. Select make of vehicle.
5. Select front or rear.
Summary of Contents for AutoComp Elite
Page 12: ...8 GETTING STARTED...
Page 26: ...22 GETTING STARTED...
Page 28: ...24 TROUBLESHOOTING...
Page 30: ......